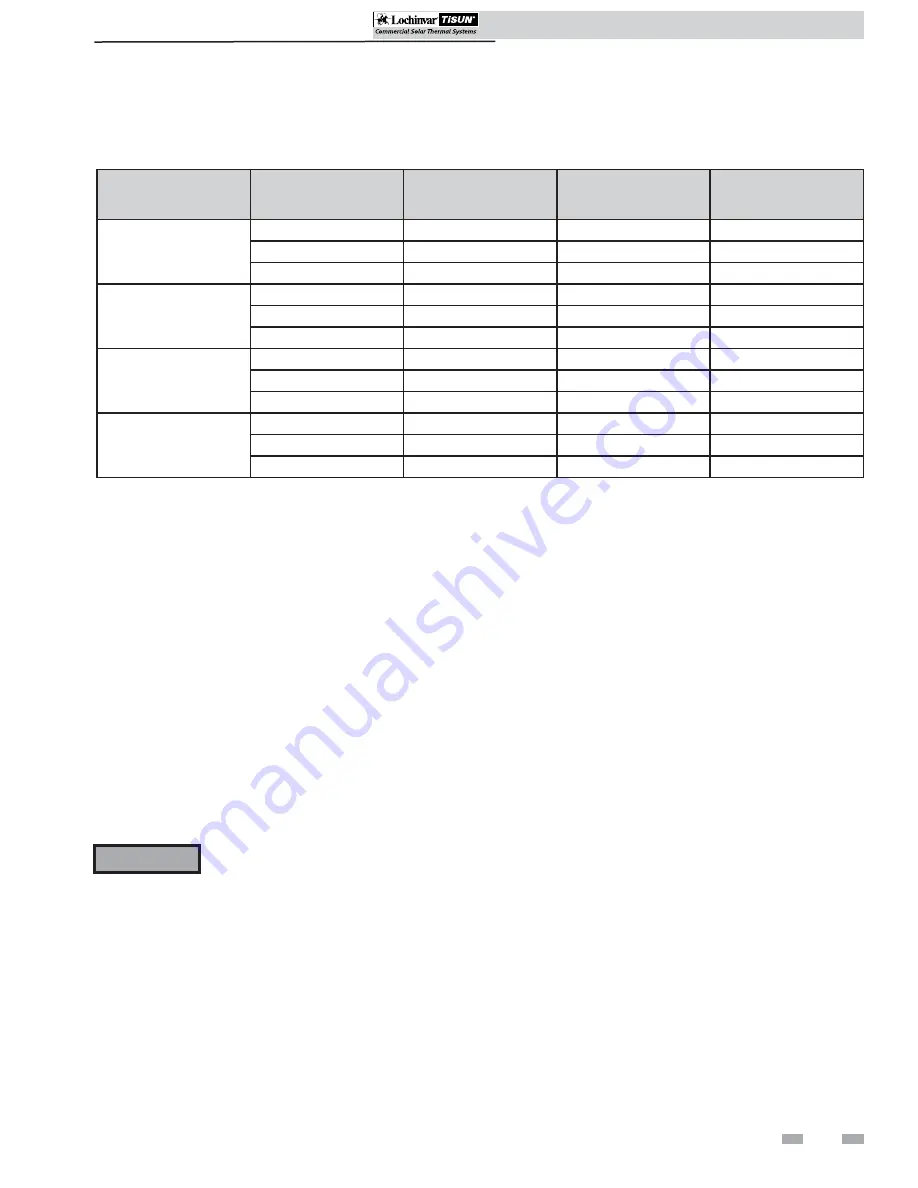
43
Typical properties of Aqueous So
(Glycol percentage by volume)
7
Maintenance
(continued)
Physical
Property
Temp.
°F
30% Glycol
Solution
40% Glycol
Solution
50% Glycol
Solution
Thermal
Conductivity
Btu/(hr•ft
2
)(°F/ft)
40
0.247
0.225
0.204
180
0.279
0.249
0.221
325
0.268
0.238
0.210
Specific Heat,
Btu/(lb•°F)
40
0.894
0.847
0.794
180
0.947
0.916
0.878
325
1.002
0.987
0.965
Viscosity,
Centipoise
40
5.75
9.63
14.28
180
0.68
0.85
1.08
325
0.31
0.39
0.40
Density,
(lb/ft
3
)
40
65.30
66.03
66.68
180
62.60
63.09
63.50
325
57.89
58.18
58.41
SCH Collectors Installation & Operation Manual
Solar circuit
1. Verify all system components are correctly installed
and
operational.
2. Check for leaks - inspect all water lines for signs of
leakage and correct any problems found.
3. Check System Pressure - monitor system pressure as the
circuit heats up (during testing) to ensure that the
pressure does not rise above the designed system
pressure. Excessive pressure rise indicates expansion
tank sizing or performance problems. See the expansion
tank manufacturer’s instruction manual for required
maintenance. See the expansion tank manufacturer
recommendations for sizing and pressure settings.
4. Check Relief Valve - Inspect the relief valve and lift the
lever to verify flow.
Before operating any relief valve ensure
that it is piped with its discharge in a safe
area to avoid severe scald potential.
WARNING
5. Check Freeze Protection Fluid - ensure that the heat
transfer fluid has the proper concentration of glycol as
recommended in this manual.
6. Remove any air that may have accumulated in the
system.
7. Check Flow Rate - ensure that the minimum
recommended flow rate can be achieved as described in
this
manual.
8. Visually inspect the dirt separator (if installed) and clean
if
necessary.
Collector
1. Visually inspect the collectors to ensure that they are in
proper working condition.
2. Visually inspect the collector substructure to ensure that
no components have become loose or disconnected.
3. Visually inspect the collector piping to ensure that there
are no leaks.
4. Visually inspect roof penetrations to ensure that
environmental elements can not enter the building.
5. Visually inspect the piping insulation to ensure the
proper orientation around piping.
Pump / control function
1. Check to ensure that the pump station is in working order
and creates the minimum flow recommended in this
manual.
2. Check control sensors to ensure that they are fully inserted
into the appropriate sensing well.
3. See
pump
manufacturer’s
recommendation
for
required
maintenance
procedure.
Control settings
1. Check sensor readings to ensure that the values being
displayed are accurate.
2. Check control settings to ensure that they are programmed
per the control specification.
3. See
controller
manufacturer’s
recommendations
for
the
required maintenance procedure.