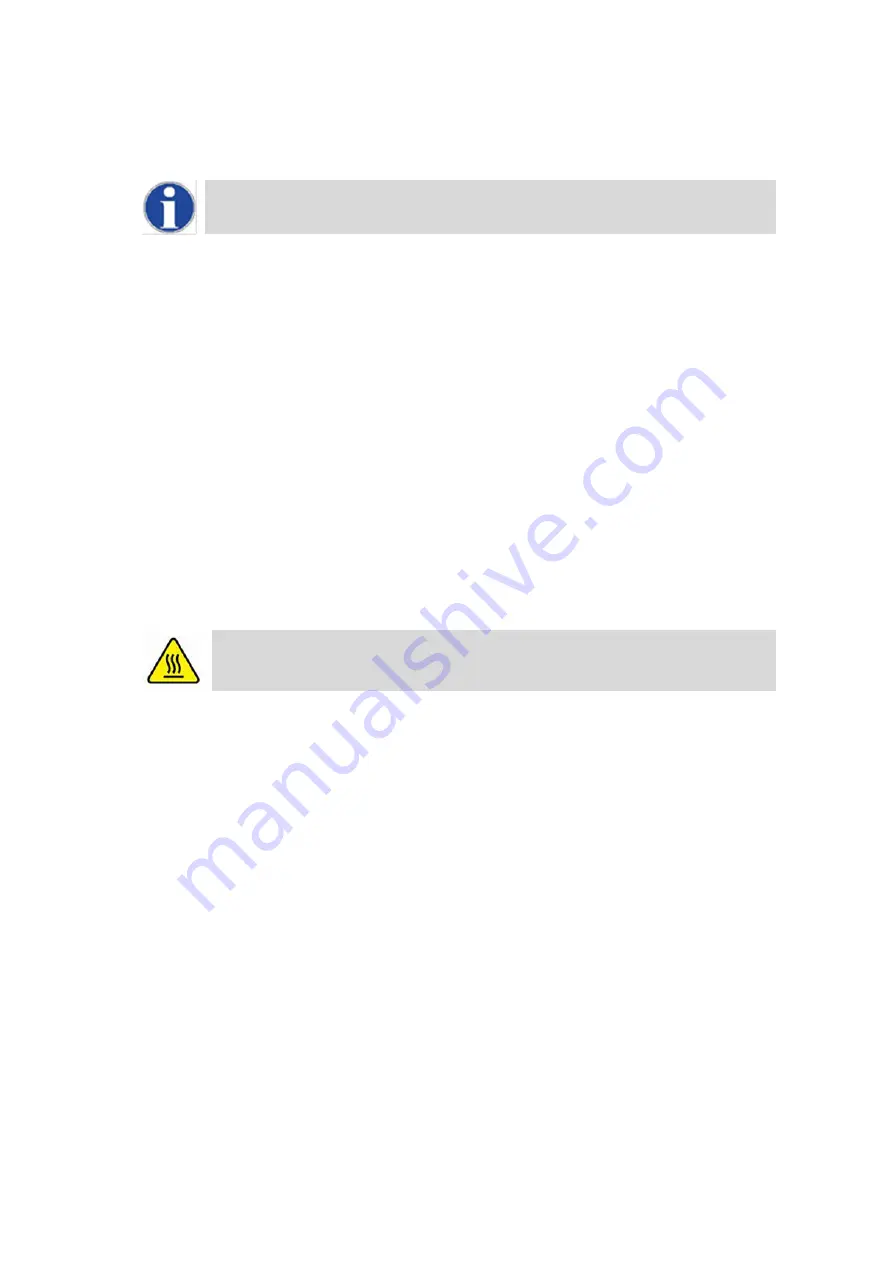
65
19.0
MAINTENANCE
19.1
GENERAL
Keep appliance area clear and free from combustible materials and flammable vapours and
liquids.
A competent person should check and ensure that the flue, its support and terminal, the ventilation to the boiler house,
safety valve, drain, pressure gauge etc. are in a serviceable and working condition and still comply with the relevant
standards and codes of practice, as detailed in Section 5: GENERAL REQUIREMENTS.
Servicing is recommended at intervals no greater than 12 months to aid trouble free operation. Even if a maintenance
schedule is determined to be less than annually, it is important that all controls and safety features are checked for
correct operation on an annual basis.
Measuring flue gas CO
2
and flue gas temperatures will give an indication of the state of the flue and burner. Results of
the flue gas analysis should be compared with previously measured values to identify any changes in operational
characteristics.
19.2
MAINTENANCE SCHEDULE
The boiler has a built in function that reminds the user that routine maintenance is due. As a default, this is set to 12
months 10,000 operational hours or 10,000 ignition cycles. Lochinvar Limited recommends that this be the maximum
service interval.
19.3
BURNER INSPECTION
The heat exchanger has a sight glass for inspection of the flame picture.
If the appliance has been in recent operation, this area may be hot. Appropriate precautions
should be taken to prevent personal injury.
To check the flame picture at high and low fire, the following procedure should be followed:
1.
Place the boiler into service mode. This is done by depressing the small button below the Enter/Reset button
for 5 seconds.
2.
The boiler should shut down and relight.
3.
Depress the service button momentarily, this should ramp the boiler up to full rate.
4.
Check the flame condition.
5.
Depress the service button momentarily, this should ramp the boiler down to low rate.
6.
Check the flame condition.
7.
Press and hold the service button for 5 seconds to take the unit out of service mode.
Summary of Contents for HERALD HCB116CE
Page 8: ...8 3 1 2 PRINCIPLE PARTS TO BE USED IN CONJUNCTION WITH TABLE 3 1 1...
Page 31: ...31 Max distance between brackets...
Page 32: ...32...
Page 33: ...33...
Page 37: ...37...
Page 53: ...53 15 8 WIRING DIAGRAM 15 8 1 WIRING DIAGRAM...
Page 54: ...54 15 9 LADDER DIAGRAM 15 9 1 LADDER DIAGRAM...
Page 92: ...92...