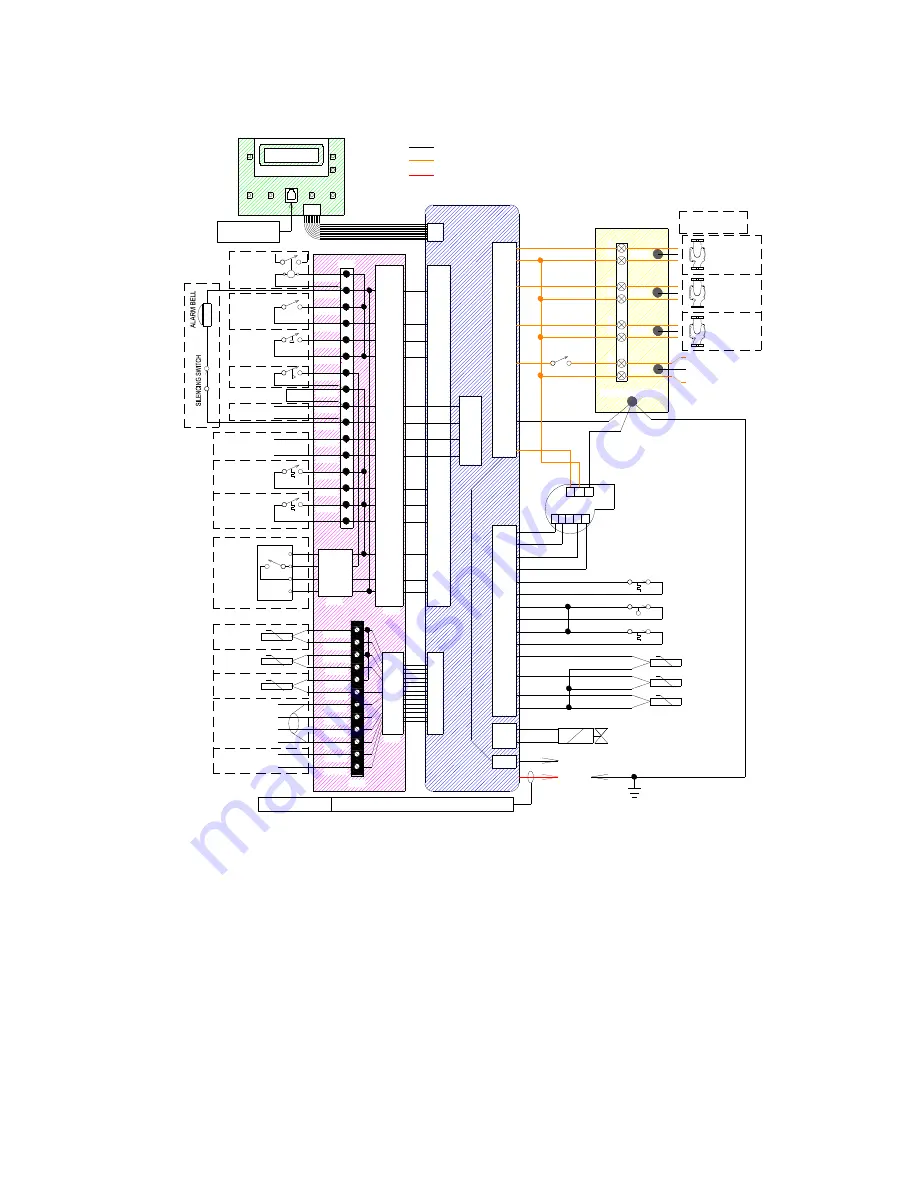
30
11.6
WIRING DIAGRAM
S3
S1
S2
S5
S4
S6
BELL JUMPER
CN3
CN4
CN5
CN2
CN1
CN2-16
CN2-15
CN2-14
CN2-13
CN2-12
CN2-11
CN2-10
CN2-9
CN2-8
CN2-7
CN2-6
CN2-5
CN2-4
CN2-3
CN2-2
diagrams to troubleshoot unit.
3. Actual connector block locations may vary from those shown on diagrams. Refer to actual components for proper connector block locations when using
or ribbon cables can lead to operational problems which could result in non-repairable damage to the integrated controller or other components.
minimum of 105°C. Exceptions: Replacement high voltage spark lead and ribbon cables must be purchased from the factory. Use of a non-approved spark lead
2. If any original equipment wire as supplied with the appliance must be replaced, it must be replaced with wire having same wire gauge (AWG) and rated for a
1. All wiring must be installed in accordance with I.E.E. Regulations and any local regulations that apply.
Notes:
CN1-1
CN1-2
CN1-3
CN1-4
CN1-5
CN1-6
CN1-7
CN1-8
CN1-9
CN1-10
CN1-11
CN1-12
CN4-14
INTERFACE
PC
X3
HIGH VOLTAGE
LOW VOLTAGE
230 VAC
X8
TR1
GND
GND
GND
GND
N
L
N
L
N
L
COM
24 VAC
CN5-2
CN5-4
CN5-3
HIGH VOLTAGE SPARK LEAD
CAUTION
HI-LIMIT
AUTO RESET
CONTROL
EXTERNAL
R
GY
BL
X6-6
X6-2
CN4-13
CN4-7
CONTROL
ZONE
THERMOSTAT
ROOM
W
X6-1
CN4-5
THERMOSTAT
DHW
Y
X6-8
CN4-8
SUPPLY
PILOT
DEVICE
AUX.
PR
PR
R
R
X3-2
X3-4
X3-3
X3-1
CONTACTS
RUN-TIME
CONTACTS
ALARM
CN4-4
CN4-10
CN4-12
CN4-11
OR
BK
P
Y
BR
X6-10
X6-5
X6-4
X6-3
X6-9
CN4-2
CN4-3
CN4-9
CN4-1
CN4-6
CN5-1
CUT-OFF
WATER
LOW
PROVING
DEVICE
AUX.
SWITCH
PRESSURE
GAS
SWITCH
FLOW
Y
BK
SHIELD
SHIELD
N
GND
L
SWITCH
ON/OFF
N
L
W
W
W
BR
BK
PR
W
OR
BR
BK
PR
W
OR
TERMINAL STRIP
BOX
JUNCTION
PUMP
PUMP
DHW
PUMP
230V
X1-4
X1-6
X1-2
X1-5
X1-3
X4
CN3
CONNECTION BOARD
B
A
RS485
-
+
0-10V
SENSOR
OUTDOOR
SENSOR
AUXILIARY
SENSOR
SYSTEM
3
5
4
2
1
GY
OR
P
OR
PR
BL
GY
OR
P
OR
PR
BL
Y
W
R
BK
X5-10
X5-4
X5-3
X5-11
X5-14
X5-7
X5-9
X5-2
X5-1
X5-8
DRAIN
BLOCKED
HI-LIMIT
MANUAL RESET
SENSOR
FLUE
SENSOR
OUTLET
SENSOR
INLET
OPTIONAL ITEMS
BOX DEPICTS
G
W
2 3
1
R
G
BK
W
T
R
R
G
W/R
ROD
SPARK
ROD
FLAME
VALVE
GAS
X1-7
X2-1
X2-2
X1-1
FAN
INTEGRATED CONTROL
X5-12
X5-6
X5-13
X5-5
X1-8
DISPLAY
PRIMARY
SECONDARY
MAINS
FIGURE 11.4 WIRING DIAGRAM