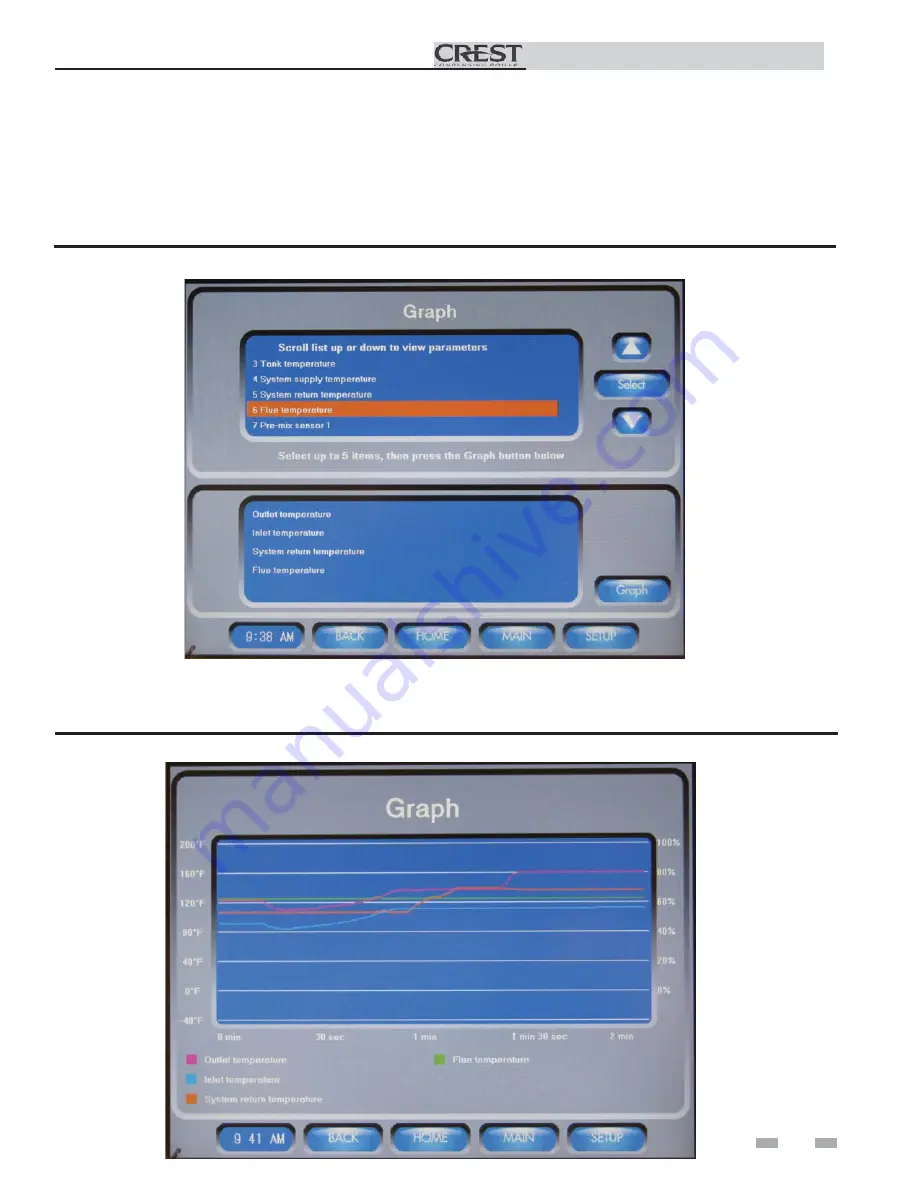
1
Service
(continued)
Service Manual
27
The Graph Screen consists of two (2) different screens. The First screen is the Parameter Selection Screen. By pressing the up and
down arrow keys the desired parameter can be selected. When the SELECT button is pressed the parameter will appear in the
bottom half of the fi rst screen. If a parameter is selected by mistake, it can be de-selected by highlighting the parameter and pressing
the SELECT button. A maximum of fi ve (5) items can be graphed at one time.
Figure 1-9 Graph Screen_Parameter Selection
Graph Screen
Figure 1-10 Graph Screen
The Second screen is accessed by pressing the GRAPH button. Once the items to be graphed are selected, press the GRAPH button to
view the graph. Each item graphed will have a different color line to represent it. The items selected will be shown below the graph
along with their corresponding color. Press the BACK button to return to the Parameter Selection Screen.
Summary of Contents for Crest 1.5
Page 54: ...3 Troubleshooting 54 NOTES ...
Page 55: ...55 NOTES ...