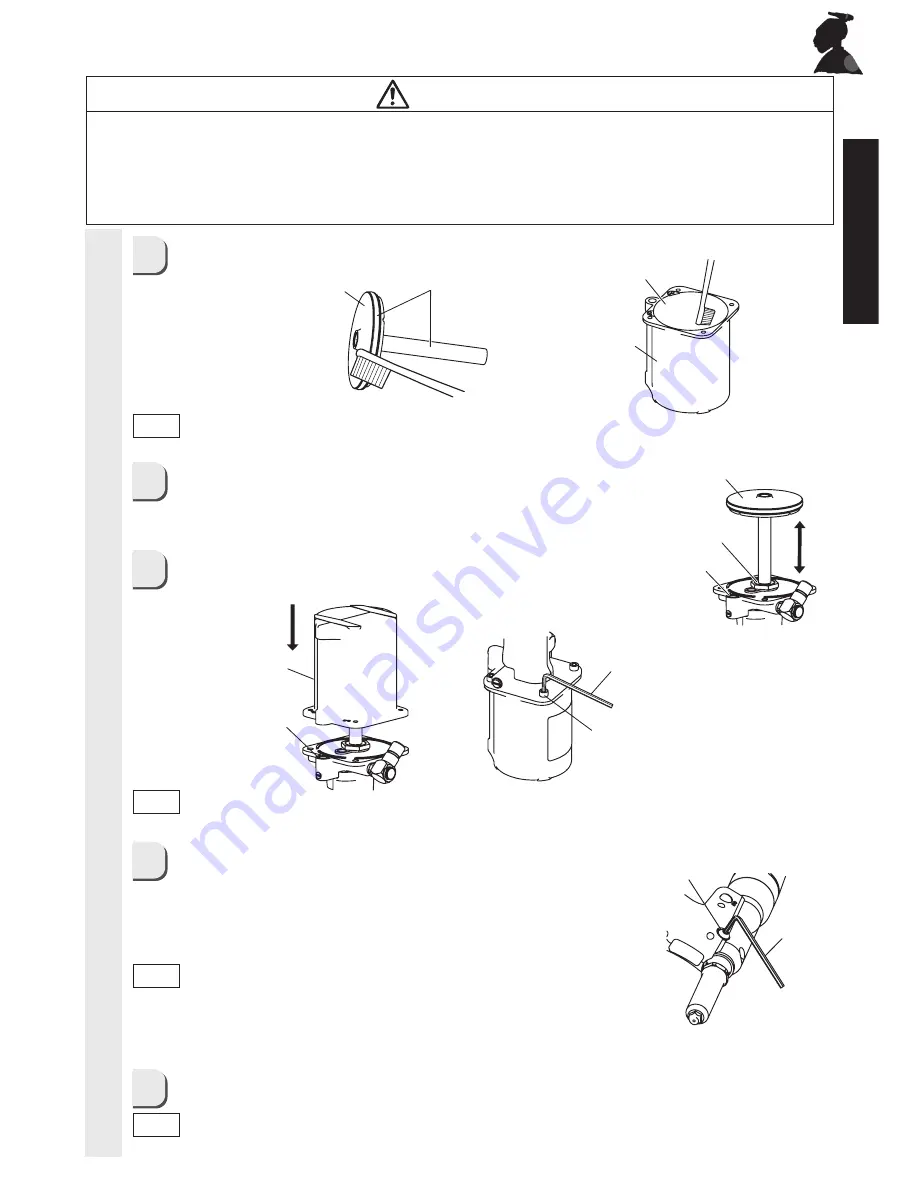
ⱥㄒ㸭(1*/,6+
12
RE-ASSEMBL
Y
9
Push and insert the Air Piston Unit into the oil supply
port and manually perform a piston motion for several
times. Wipe off hydraulic oil spilling out of the oil
supply port.
Attach the Cylinder Cup on the Air Piston Unit, and
keeping pressing it down tighten the 4 hex socket
screws.
After assembled Frame Head with Frame A, turn the unit
as the Bleed Plug (hex socket bolt) comes to the upper side.
Then, loosen it using a hex key wrench (AF 4mm) in order to
let excessive hydraulic oil and air (bubble) out.
After making sure that hydraulic oil no longer comes out,
tighten the Bleed Plug again.
Wipe off hydraulic oil adhering to the main body or spilling out before use.
10
11
12
Air Piston Unit
Oil supply port
Cylinder Cup
Bleed Plug
Hex key
wrench
(AF 4mm)
O-ring SS9.5
Hex socket screw
(x4)
O-ring
Hex key wrench
(AF 4mm)
8
Apply grease to the O-Ring and rod of Air Piston Unit and to the inside of Cylinder
Cup using brush.
Cylinder Cup
Apply grease
Apply grease
Air Piston Unit
ە
Avoid skin contact with substances such as hydraulic oil, lubricating oil and grease.
Such substances may cause inflammation of the skin. If they come into contact with your skin,
wash the affected area thoroughly.
ە
Maintain the tool with due care.
Refer to the Instruction Manual for details on replacing parts and attachments, otherwise injury may
occur.
CAUTION
ە
Before assembling, be sure to apply lubricant such as grease to each sliding section.
ە
Recommended grease is Grease
JUDGH
1~2.
Note
ە
Assemble in reverse order of disassembly.
ە
Make sure the O-ring SS9.5 is surely set in the counterbore.
Note
ە
Note that hydraulic oil may squirt out when you loosen the
ࠉ
Bleed Plug.
ە
The work should be done by necessity after feeding hydraulic
oil. Otherwise there may be detrimental to the tool in loading
rivet or breakage of Frame.
Note
ە
During disassembly/assembly, be careful to prevent cutting dusts of metal and
other objects from getting into the hydraulic oil and Air Cylinder.
Note