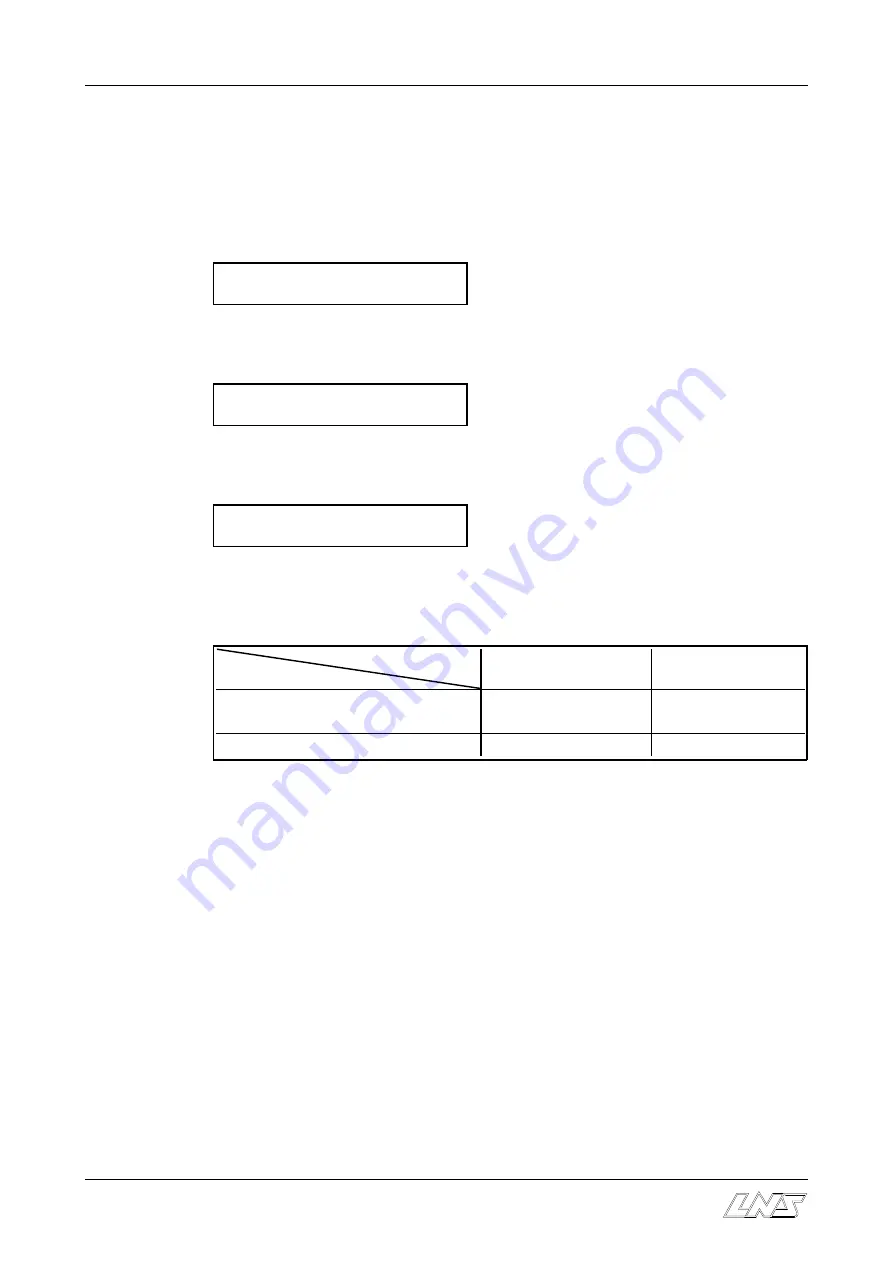
4
START UP MANUAL
HYDROBAR EXPRESS 326 S2
End of bar setting :
Important : Before handling the barfeeder, stop the lathe at the end of part cycle.
1. Press the key
[STOP]
.
2. Press the key
[MENU]
.
The display reads :
PARAMETERS RELATED
TO START UP
3. Press twice the key attributed to the icon
[PAGE DOWN]
.
The display reads :
SETTINGS FOR
POSITIONING
4. Press the key attributed to the icon
[ENTER]
.
The display reads :
POSITION OF THE END OF THE
BAR **** MM
5. Press the key attributed to the icon
[SET]
.
Depending on which sequence the bar feed is in when the parameter is selected, the
available functions and icons can change :
Functions
Conditions
By offset correction
By teaching
- Guiding channel closed
- No bar stock in the guiding channel
icon
: [+/-]
icon :
[TEACH IN]
- Guiding channel open
icon
: [+/-]
---
[+/-]
By offset correction
C
Press the key attributed to the icon
[+/-]
.
The display reads the current end of bar position.
C
Enter the correction value with the numerical keys. Then, press the key attributed to
the icon
[+]
to add the value, or the key attributed to the icon
[-]
to substract it. The
display reads the new end of bar position.
C
To exit the end of bar set mode, press the key attributed to the icon
[ESC].
[TEACH IN]
By teaching
C
Press the key attributed to the icon
[TEACH IN]
.
The display reads the current end of bar position
C
Press the key
[FWD]
and advance the pusher to the desired position (see previous
page).
C
To validate the new end of bar position, keep
[ENTER]
pressed until the icon
disappears
.
6. To exit the set mode, press the keys
[MENU]
or
[STOP]
.
Summary of Contents for 326 S2
Page 1: ...ENG...