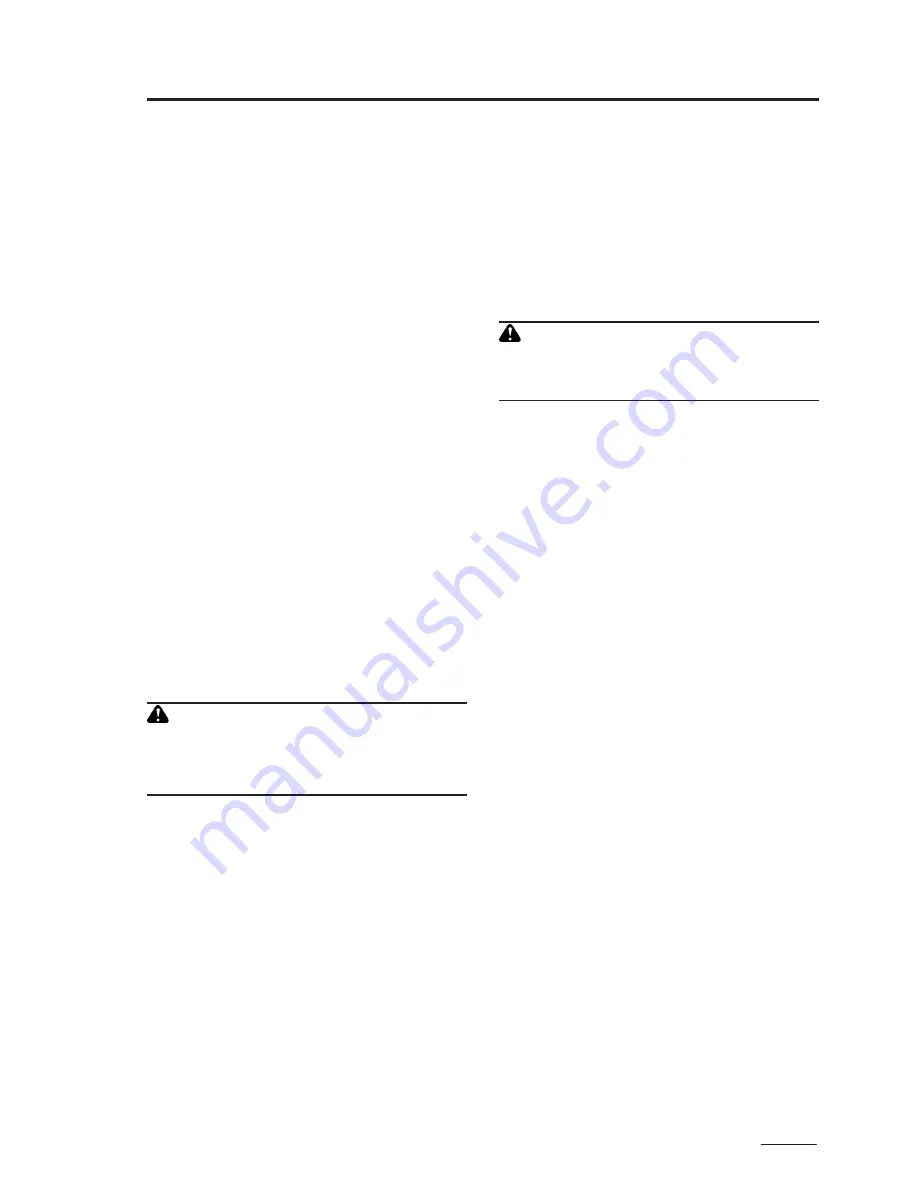
page 55
02.42 THE FANSHROUD - TS/TR
An aluminium fanshroud is fitted to all engines
except Build 16 which has one of sheet metal.
Removing the Fanshroud
1. Remove the flywheel.
2. Remove the two nuts and then remove the rectifier/
regulator cover.
3. Carefully noting the position of the electrical cables,
disconnect all four cables.
4. Remove the two nuts, washers and distance pieces
and remove the rectifier/regulator unit from the
fanshroud.
The unit will be fitted to either, the manifold side of
the shroud or above the starter motor.
5. Remove the cable clip securing the cable inside
the fanshroud.
6. Remove the six screws securing the stator and
remove it, gently easing the cable through the
fanshroud.
7. Remove the two bolts that are fitted through the
lower end of the fanshroud securing it to the sump.
8. Remove the self-lock bolts.
a. On older engines ease back the tab washers and
remove the bolts.
9. Lift off the housing.
Refitting the Fanshroud
Refitting is carried out in the reverse order and it is
recommended that new tabwashers are fitted and
correctly locked after the bolts have been torque
loaded to 43.5Nm (32.0lbf ft).
The tabwashers and bolts can be replaced with
the current self-locking setscrews which must be torque
loaded to 88.0Nm (65.0lbf ft).
CAUTION
If the sump has been removed, the procedure detailed
in "Replacing the Oil Sump" must be followed when
refitting the fanshroud to prevent the possibility of distorting
it resulting in excessive flywheel to shroud run-out. This is
particularly important on Build 16 engines.
Section 02
Engine Servicing and Adjustments
- flywheel fanshroud and housing
02.43 FLYWHEEL HOUSING - TX
Removing the Flywheel Housing
1. Remove the flywheel.
2. Remove the six self-locking setscrews.
3. Remove the fanshroud, noting that it is secured to
the sump by two bolts.
Refitting the Flywheel Housing
Refitting is carried out in the reverse order with the
self-locking setscrews torque loaded to 88.0Nm
(65.0lbf ft).
CAUTION
If the sump has been removed, the procedure detailed
in "Replacing the Oil Sump" must be followed when
refitting the fanshroud to prevent the possibility of distorting
it resulting in excessive flywheel to shroud run-out.
Summary of Contents for TR1
Page 1: ...TS TR TX Workshop Manual Edition 12 May 2005 Publication P027 08221 ...
Page 2: ...page 2 ...
Page 80: ...page 80 Section 05 Routine Maintenance TS TR wearing parts TS TR Wearing Parts ...
Page 81: ...page 81 Section 05 Routine Maintenance TS TR wearing parts TS TR Wearing Parts ...
Page 82: ...page 82 Section 05 Routine Maintenance TX wearing parts TX Wearing Parts ...
Page 83: ...page 83 Section 05 Routine Maintenance TX wearing parts TX Wearing Parts ...
Page 90: ...page 90 Section 07 Flywheel Charge Windings Syncro Syncro Fault Finding Flow Charts ...
Page 91: ...page 91 Section 07 Flywheel Charge Windings Syncro Syncro Fault Finding Flow Charts ...
Page 93: ...page 93 Nicsa Fault Finding Flow Charts Section 07 Flywheel Charge Windings Nicsa ...
Page 94: ...page 94 Section 07 Flywheel Charge Windings Nicsa Nicsa Fault Finding Flow Charts ...
Page 95: ...page 95 Section 07 Flywheel Charge Windings Nicsa Nicsa Fault Finding Flow Chart ...
Page 96: ...page 96 ...
Page 98: ...page 98 Section 08 Electrical Wiring Diagrams ...
Page 99: ...page 99 Section 08 Electrical Wiring Diagrams ...
Page 100: ...page 100 Section 08 Electrical Wiring Diagrams ...
Page 101: ...page 101 Section 08 Electrical Wiring Diagrams ...
Page 102: ...page 102 Section 08 Electrical Wiring Diagrams ...
Page 103: ...page 103 Section 08 Electrical Wiring Diagrams ...
Page 104: ...page 104 ...
Page 115: ...page 115 Section 11 Index Section 11 Index a ...