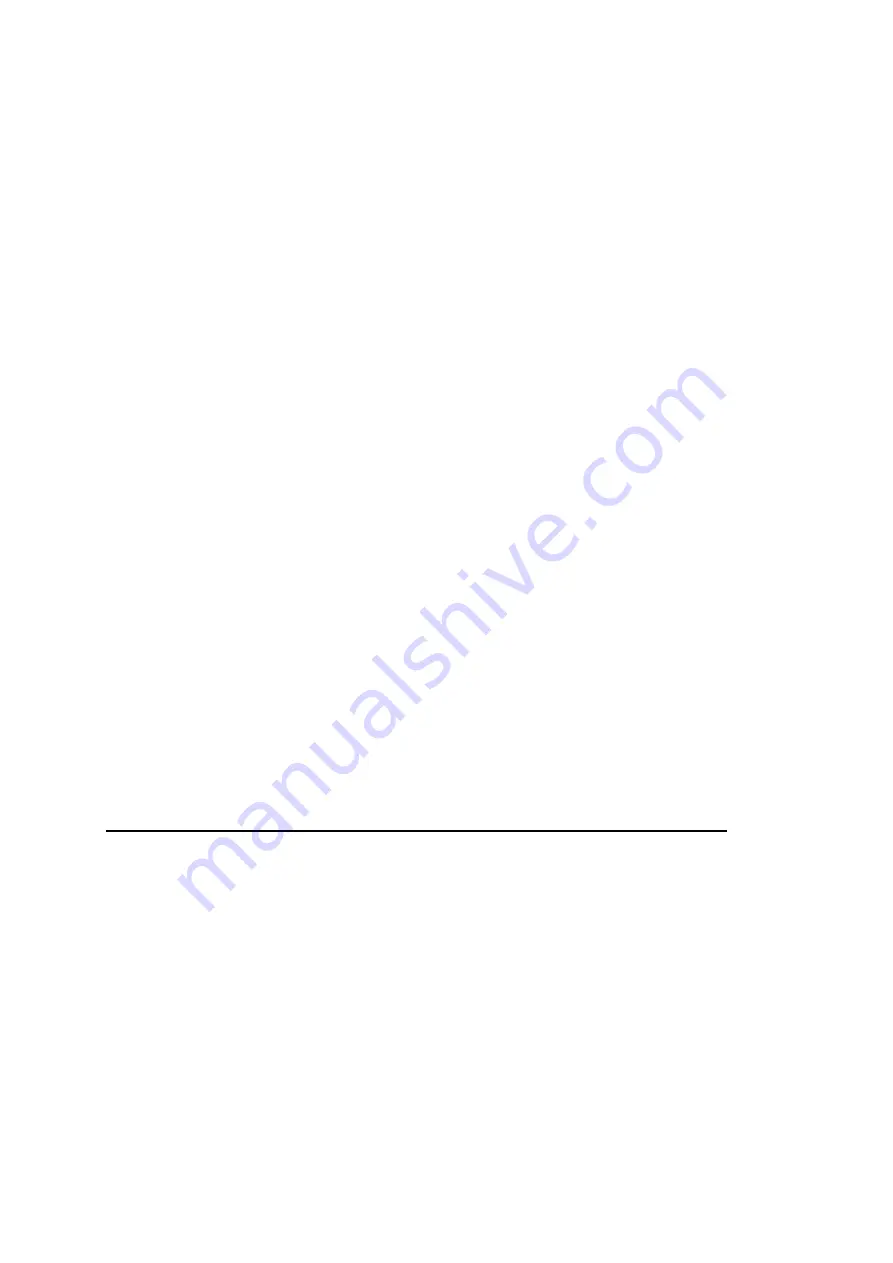
1.3.3 Any personnel working on the machine must read this operating manual
especially this chapter on safety precautions-prior to beginning. Learning on
the job is too late. This especially applies to personnel who occasionally work
on the machine (e.g. setup and maintenance crews).
1.3.4 Perform regular spot checks to ensure that personnel are doing their jobs in a
safe and conscientious manner and that they are adhering to the instructions in
the operating manual!
1.3.5 Use personal protective equipment whenever necessary or when required by
regulations!
1.3.6 Pay attention to all safety and danger warning labels located on the machine!
1.3.7 Keep all safety and danger warning labels in/on the machine completely
legible!
1.3.8 Stop the machine and notify the parties in charge when performing safety-
related changes on the machine or its operation!
1.3.9 Make no alterations and do not add componentry or rebuild the machine
without permission from the manufacturer!
1.3.10 Use only original spare parts!
1.3.11 Perform all scheduled inspections as needed, or use the scheduled intervals
outlined in the operating manual!
1.3.12 For carrying out maintenance work, adequate workshop equipment is
indispensable.
1.4 Qualifications for Selecting Operators; Fundamental Responsibilities
1.4.1 Only personnel of proven reliability is allowed to operate the machine. Observe
legal minimum age requirements!
1.4.2 Use only qualified and trained personnel. Clearly define staff responsibilities
concerning operation of machine, setup, maintenance, and repair works!
1.4.3 Ensure that the floor cutter is handled only by persons instructed to do so.
1.4.4 Define machine operator's responsibility - also in respect to road traffic
regulations - and his ability to object to instructions not in compliance with the
safety regulations!
1.4.5 Apprentices, new employees, or personnel being trained must be
4
Summary of Contents for FS 27-E
Page 9: ...9...
Page 13: ...13 13...
Page 14: ...14...
Page 17: ...Date Operating hours performed maintenance work Signature stamp 17...
Page 18: ...18...
Page 23: ...23...