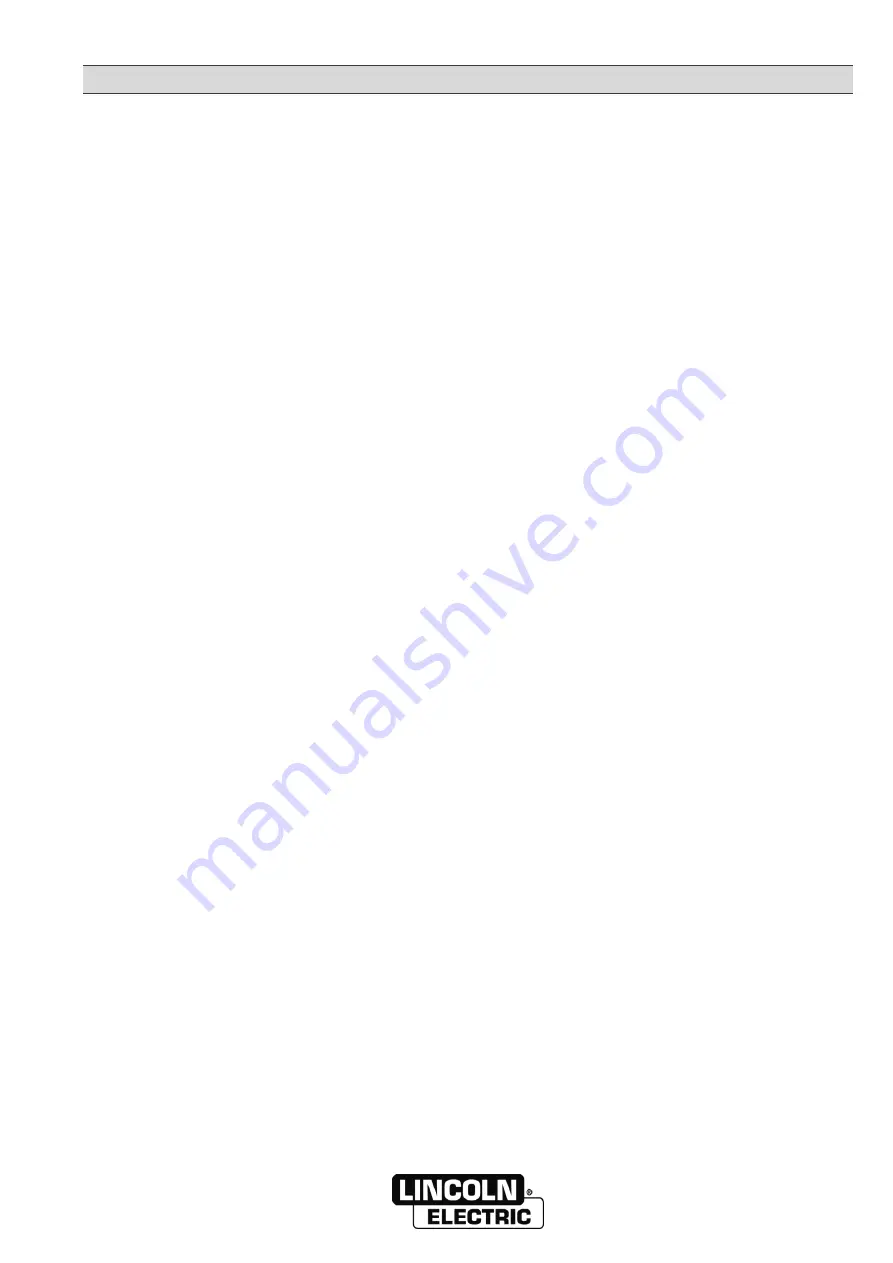
8695 4387 / H
F - UTILISATION DE L
’INSTALLATION PLASMA
EASYTOME
F-25
7 - USEFUL INFORMATION FOR ADJUSTING THE PARAMETERS
If the speed is slow:
When THC is activated, the torch will tend to dip.
The arc voltage value should be increased by 1 V per speed bracket of 5 mm/s.
Speed may be reduced when one wants to reduce the cutting angle (bevel angle).
There will be more dross under the piece after the cut is made. Such dross is generally easy to remove
from steel.
If the speed is high:
When THC is activated, the torch will tend to rise.
The arc voltage value should be decreased by 1 V per speed bracket of 5 mm/s.
Speed may be increased when one wants to reduce the quantity of dross under the cut or increase
productivity.
Caution! After a certain point, the effect is the opposite and the molten material is hard to remove. The arc
is said to go down under the plate.
When the speed is increased, the bevel angle increases (cutting angle)
Ideal speed:
It is reached when the plasma jet under the plate is straight and rigid and slightly tilted forwards in relation
to the cutting direction.
If you want to reduce the bevel angle
Three simple solutions:
Reduce the speed (as explained above)
Increase by one intensity range for the same thickness
Reduce the arc voltage
If you want to increase productivity:
Increase the speed (mind you do not reach the speed where the arc starts to go down)
Increase by one or more intensity ranges for the same thickness
Piercing phases:
The piercing height (distance between the bottom of the cap and the plate) must not be set too high. If that
is so, arc transfer would be difficult.
The machine feedback control parameter (return Ric) must be active. This information tells the machine
that the arc has been transferred to the plate. Without that, the machine movement cannot start. The
piercing time for coming out under the plate is then correctly followed.
The torch must not be too low during the piercing phase, so as to limit the return of splatter on the nozzle.
The piercing time must be adjusted so that the machine starts the cutting movement only when the plate
has been pierced:
o
If it is too early, the material may return on the nozzle and damage it
o
If it is too long, the diameter of the piercing hole will be too large or the arc may break on fine
thickness.