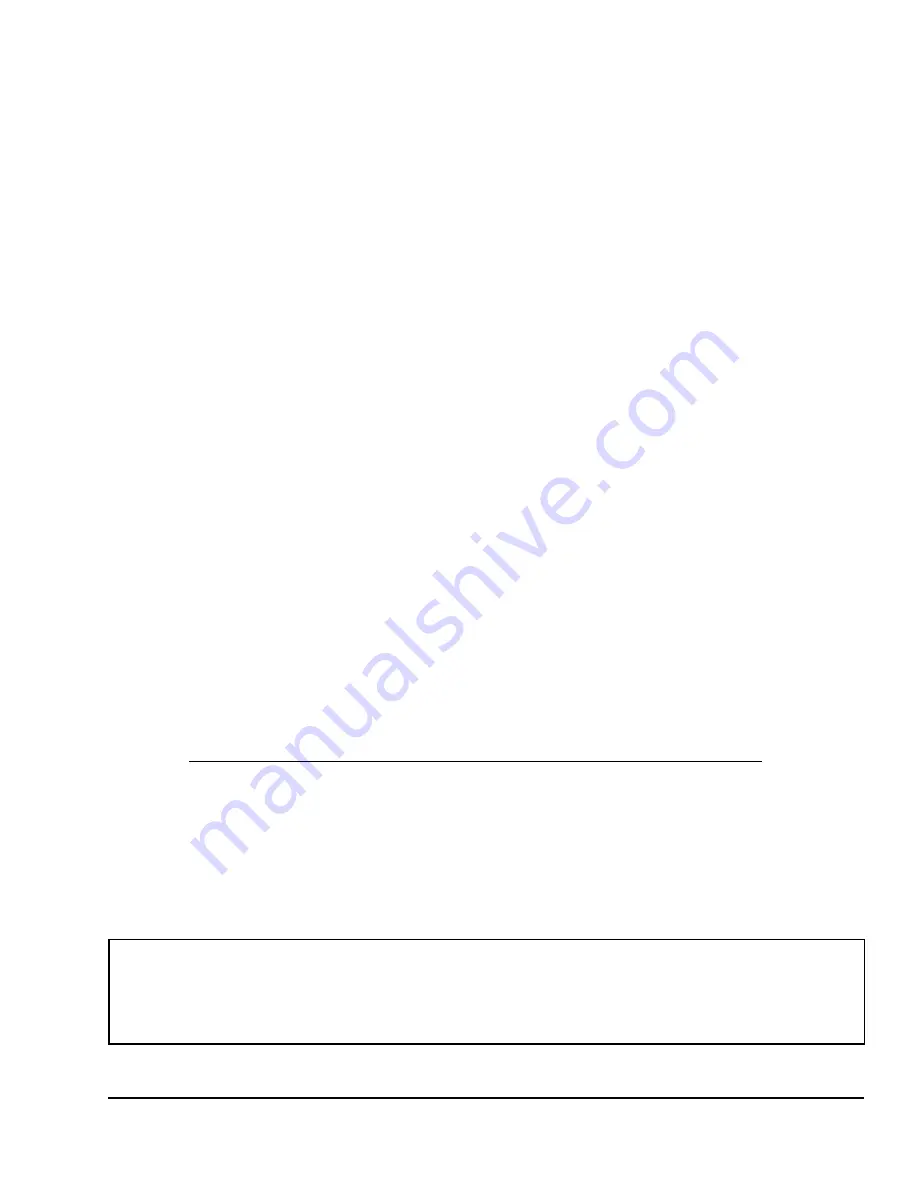
April 27, 2004 Manual Version 1.01
8.1
Note!
Incorrect gib adjustments, and/or severe bearing wear in the slide drive system can cause the
slide to cock and generate significant forces against linear guides or gibs. These non-
symmetrical forces can void the assumption of central loading and introduce some error in the
calibration procedure.
Section 8
Calibration
Calibration of an OmniLink II Tonnage Monitor Module consists of achieving a known load on the
machine and adjusting the installed monitor so that the known load is displayed correctly. The known
load used during calibration should be at least 50% of rated machine load and preferably 100% of rated
machine load. On straight side machine frame configurations of tie rod construction, it is always
advisable to use loads of 100% of machine rating in calibration when strain links are mounted on uprights
compressed by the tie rods. False load readings can be generated if a tie rod loses enough tension that the
upright is released from compression before full load is reached. This condition can be detected during
calibration if 100% of machine rating load is used.
Either static or dynamic calibration techniques can be used to calibrate Tonnage Monitor Module. Load
cell(s) are used to provide the known load in dynamic calibration. The load cell(s) are placed in the
machine point of operation (normally with tooling absent) and a combination of shimming and machine
shut height adjustment is used to generate the desired load to be used for calibration. The machine must
be cycled, so that the slide strikes the load cells at the bottom of the stroke to generate the load.
Hydraulic jacks are used in static calibration of the Tonnage Monitor Module. The machine slide is
placed in the bottom of stroke position, and if necessary, the hydraulic jack(s) are placed upon plates or
shims in the point of operation so that they can exert force between slide and bolster. A large pressure
gauge is used to indicate the pressure of the hydraulic fluid as the jack is pumped up. The force exerted
by the jack is equal to the fluid pressure times the area of the jack cylinder. Thus, the pressure required to
exert a given force (tonnage) can be determined and adjusted to that value.
Single or multiple load cells or jacks can be used to load the machine to the value used for calibration.
When a single load cell or jack is used for calibration, it should be centrally located under the machine
slide. Where multiple load cells or jacks are employed for calibration, they should be located in a
geometrically symmetrical pattern with respect to the center of the machine slide. The preferred
procedure is to place a single load cell or jack directly under each connection to the slide from the
crankshaft. Do not exceed the point loading of the ram specified by the press manufacturer.
When multiple load cells are used, each load cell should be of the same physical dimensions and load
rating. The load cells must be shimmed as necessary to provide equal loads on each cell. The
combination of geometrically symmetrical location and equal loading for load cells will produce a total
machine load equal to the sum of the loads on each individual load cell and will simulate a single central
load.
Summary of Contents for OmniLink II
Page 5: ...April 27 2004 Manual Version 1 01 iv ...
Page 7: ...April 27 2004 Manual Version 1 01 1 2 ...
Page 21: ...April 27 2004 Manual Version 1 01 3 8 ...
Page 44: ...April 27 2004 Manual Version 1 01 4 23 Section 4 5 4 N A ...
Page 45: ...April 27 2004 Manual Version 1 01 4 24 ...
Page 69: ...April 27 2004 Manual Version 1 01 7 14 ...
Page 77: ...April 27 2004 Manual Version 1 01 8 8 ...