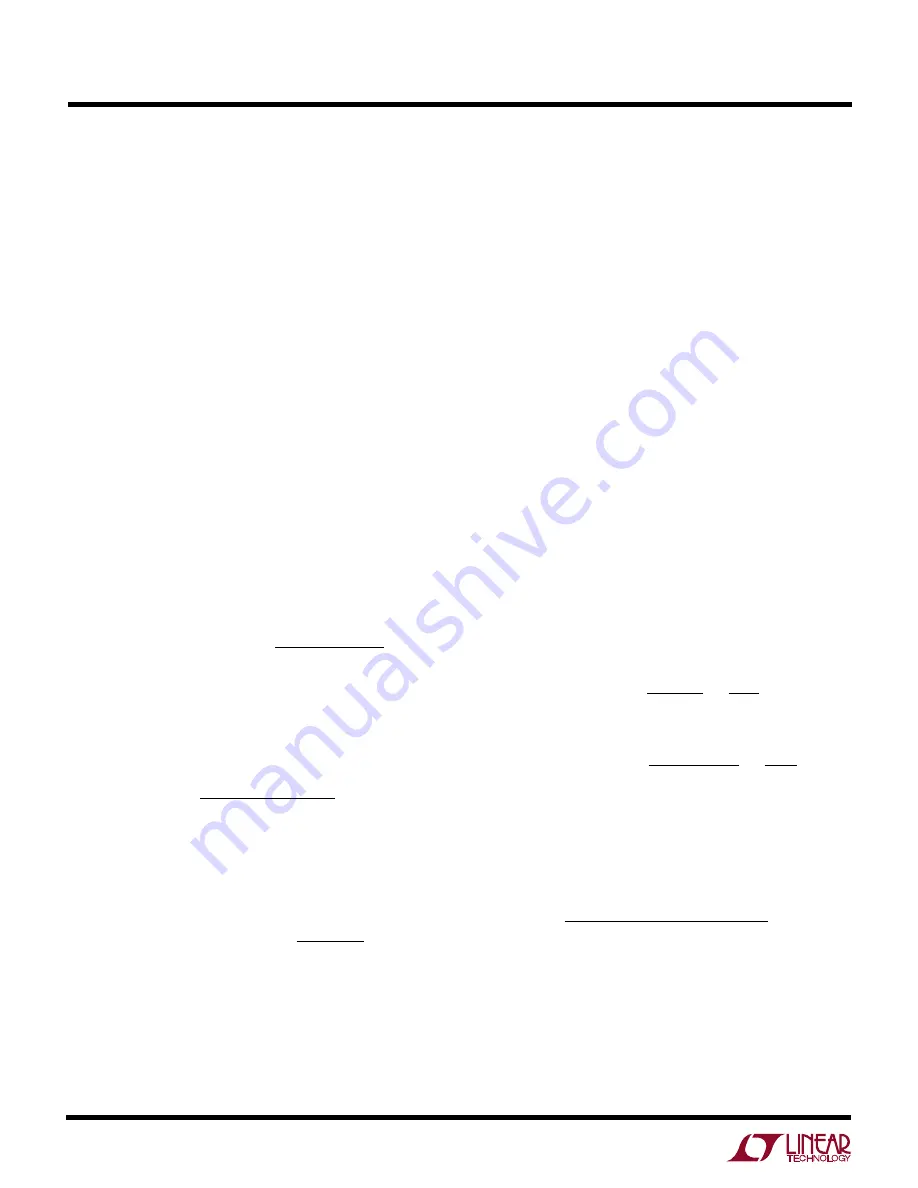
16
LTC1624
APPLICATIO
N
S I
N
FOR
M
ATIO
N
W
U
U
U
identical voltages are applied to L1 and L2 throughout the
switching cycle. By making L1 = L2 and wound on the
same core the input ripple is reduced along with cost and
size. All SEPIC applications information that follows
assumes L1 = L2 = L.
SEPIC Converter: Power MOSFET Selection
One external N-channel power MOSFET must be selected
for use with the LTC1624 for the switch. As in boost
applications the source of the power MOSFET is grounded
along with the SW pin. The peak-to-peak gate drive levels
are set by the INTV
CC
voltage. This voltage is equal to
approximately 5V for V
IN
> 5.6V and a logic level MOSFET
can be used. At V
IN
voltages below 5V the INTV
CC
voltage
is equal to V
IN
– 0.6V and a sublogic level MOSFET should
be used.
Selection criteria for the power MOSFET include the “ON”
resistance R
DS(ON)
, reverse transfer capacitance C
RSS
,
input voltage and maximum output current. When the
LTC1624 is operating in continuous mode the duty cycle
for the MOSFET is given by:
Main Switch Duty Cycle =
V
V
V
V
V
OUT
D
IN
OUT
D
+
+
+
The MOSFET power dissipation and maximum switch
current at maximum output current are given by:
P
I
V
V
V
V
V
R
k V
V
I
C
kHz
where
I
I
V
V
V
MAIN
SW MAX
OUT
D
IN MIN
OUT
D
DS ON
IN MIN
OUT
SW MAX
RSS
SW MAX
OUT MAX
OUT
D
IN MIN
=
+
+
+
+
( )
+
+
( )(
)
=
+
+
( )
( )
( )
( )
( )
( )
( )
( )
2
1 85
1
200
1
δ
.
δ
is the temperature dependency of R
DS(ON)
and k is a
constant inversely related to the gate drive current. The
peak switch current is I
SW(MAX)
+
∆
I
L
.
MOSFETs have I
2
R losses plus the P
MAIN
equation
includes an additional term for transition losses that are
highest at high total input plus output voltages. For
(V
IN
+ V
OUT
) < 20V the high current efficiency generally
improves with larger MOSFETs, while for (V
IN
+ V
OUT
) >
20V the transition losses rapidly increase to the point that
the use of a higher R
DS(ON)
device with lower C
RSS
actual
provides higher efficiency. For additional information refer
to the Step-Down Converter: Power MOSFET Selection in
the Applications Information section.
SEPIC Converter: Inductor Selection
For most applications the equal inductor values will fall in
the range of 10
µ
H to 100
µ
H. Higher values reduce the
input ripple voltage and reduce core loss. Lower inductor
values are chosen to reduce physical size and improve
transient response.
Like the boost converter the input current of the SEPIC
converter is calculated at full load current. Peak inductor
current can be significantly higher than output current,
especially with smaller inductors and lighter loads. The
following formula assumes continuous mode operation
and calculates maximum peak inductor current at mini-
mum V
IN
:
I
I
L1 PEAK
L2 PEAK
( )
( ) ( )
( )
( )
( )
( )
=
+
=
+
+
I
V
V
I
I
V
V
V
I
OUT MAX
OUT
IN MIN
L
OUT MAX
IN MIN
D
IN MIN
L
∆
∆
1
2
2
2
The ripple current in the inductor (
∆
I
L
) is typically 20% to
30% of the peak current occuring at V
IN(MIN)
and I
OUT(MAX)
,
and
∆
I
L1
=
∆
I
L2
. Maximum
∆
I
L
occurs at maximum V
IN
.
∆
I
V
V
V
kHz L V
V
V
L
IN
OUT
D
IN
OUT
D
P-P
( )
=
( )
+
(
)
(
)( )
+
+
(
)
200
By making L1 = L2 and wound on the same core
the value
of inductance in all the above equations are replaced by
2L due to their mutual inductance. Doing this maintains
the same ripple current and inductive energy storage in the
inductors. For example a Coiltronix CTX10-4 is a 10
µ
H
inductor with two windings. With the windings in parallel