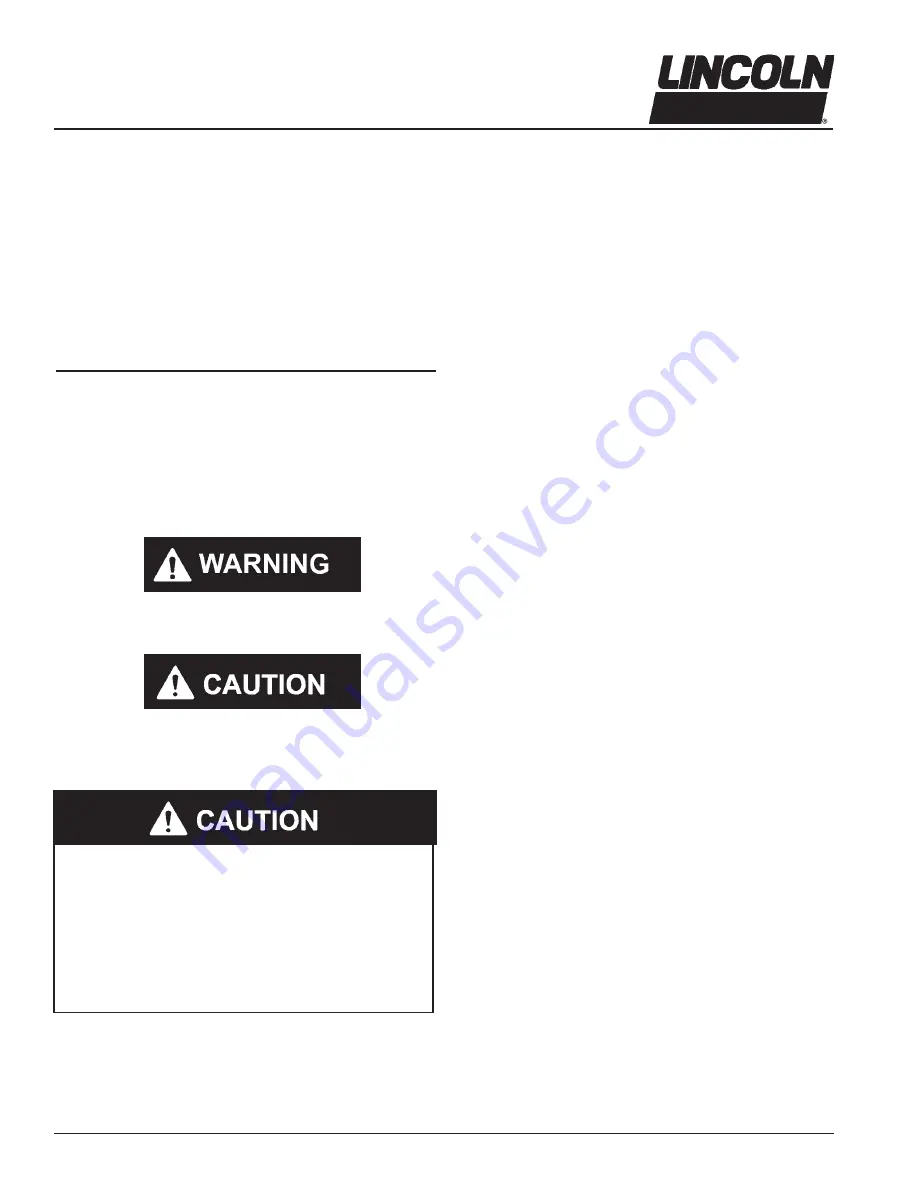
Page Number - 2
FlowMaster™ Rotary Driven Electric Pump
Form 402753
Description
A newer version of the FlowMaster pump was introduced in July of
2008. These units incorporate the following improvements:
* Bushing & plunger seals used along with elastomer cup seals for
longer life and better high temperature operation.
* A crankcase oil dipstick
* Hardened and ground section on the reciprocating tube for longer
life and better crankcase oil control.
+DUGHQHGDQGJURXQGSLYRWSLQEXVKLQJVZLWKDWLJKWHU¿WLQWRWKH
pivot pin anchor.
* Improved pivot pin fastener with deeper Allen hex socket.
All of the improved parts can be used with the older model pumps,
so the upgraded parts and subassemblies will now be supplied
to repair older model pumps. Please see the “Maintenance and
Repair” section for a list of the new repair kits and their proper ap-
plication.
85598 - 400 pound pump, 360RPM maximum, 5,000 psi
max. pressure rating
85599 - 120 poung pump, 360 RPM maximum, 5,000 psi
maxpressure rating
General Description
The Lincoln Industrial rotary A/C electric pump uses a 120-230
VAC dual voltage motor and a single stage planetary gear
drive. Grease output is proportional to the pump RPM.
The pump is primarily designed for centralized lubrication sys-
tems such as the Single Line parallel, Single Line Progressive
and Two Line systems.
The pump is driven by the rotary motion of the electric motor.
Rotary motion is converted to reciprocating motion through an
eccentric crank mechanism. The reciprocating action causes
the pump cylinder to move up and down. The unit is a positive
displacement double acting pump as grease output occurs dur-
ing both the up and down stroke.
During the down stroke, the pump cylinder is extended into the
grease. Through the combination of shovel action and vacuum
generated in the pump cylinder chamber, the grease is forced
into the pump cylinder. Simultaneously, grease is discharged
through the outlet of the pump. The volume of grease during
intake is twice the amount of grease output during one cycle.
During the upstroke, the inlet check closes, and one half of the
grease taken in during the previous stroke is transferred through
this pump. Contact the factory authorized warranty and service
center nearest you for repair or adjus®ents other than mainte-
QDQFHVSHFL¿HGLQWKLVPDQXDO
Annual inspection by the factory authorized warranty and ser-
vice center nearest you is recommended.
A list of factory authorized warranty and service centers is avail-
able upon request at www.lincolnindustrial.com
Damaged Pumps
Any pump that appears to be damaged in any way, is badly
worn or operates abnormally, shall be removed from use until
repairs are made. Contact the factory authorized warranty and
service center nearest to you for repairs.
Table of Contents
Page
Safety..…….……………................................................................2
Description....................................................................................2
Appropriate Use................................................................3
3XPS 3HUIRUPDQFH DQG 6SHFL¿FDWLRQV
Installing the Pump.....................................................................3
Operation.....................................................................................4
Crank Case Oil................................................................................4
Pump Dimensions.............................................................5
Trouble Shooting............................................................................6
Required Tools...............................................................................7
Maintenance and Repair...........................................................8
Repair Parts List............................................................................23
Safety
Read and carefully observe these operating instructions before
unpacking and operating the pump! The pump must be oper-
ated, maintained and repaired exclusively by persons familiar
with the operating instructions. Local safety regulations regard-
ing installation, operation and maintenance must be followed.
Operate this pump only after safety instructions and this service
manual are fully understood.
Indicates a potentially hazardous situation which, if not avoided,
could result in death or serious injury.
Indicates a potentially hazardous situation which, if not avoided,
may result in minor or moderate injury.
Safety Instructions
Inspection
If overpressurizing of the equipment is believed to have oc-
curred, contact the factory authorized warranty and service
center nearest you for inspection of the pump.
Specialized equipment and knowledge is required for repair of
This equipment generates very high grease pressure.
Extreme caution should be used when operating this equip-
ment as material leaks from loose or ruptured
FRPSRQHQWVFDQLQMHFWÀXLGWKURXJKWKHVNLQDQGLQWRWKH
body causing serious bodily injury. Adequate protection is
recommended to prevent splashing of material onto the skin
or into the eyes.
,IDQ\ÀXLGDSSHDUVWRSHQHWUDWHWKHVNLQJHWHPHUJHQF\
medical care immediately. Do not treat as a simple cut. Tell
DWWHQGLQJSK\VLFDOH[DFWO\ZKDWÀXLGZDVLQMHFWHG