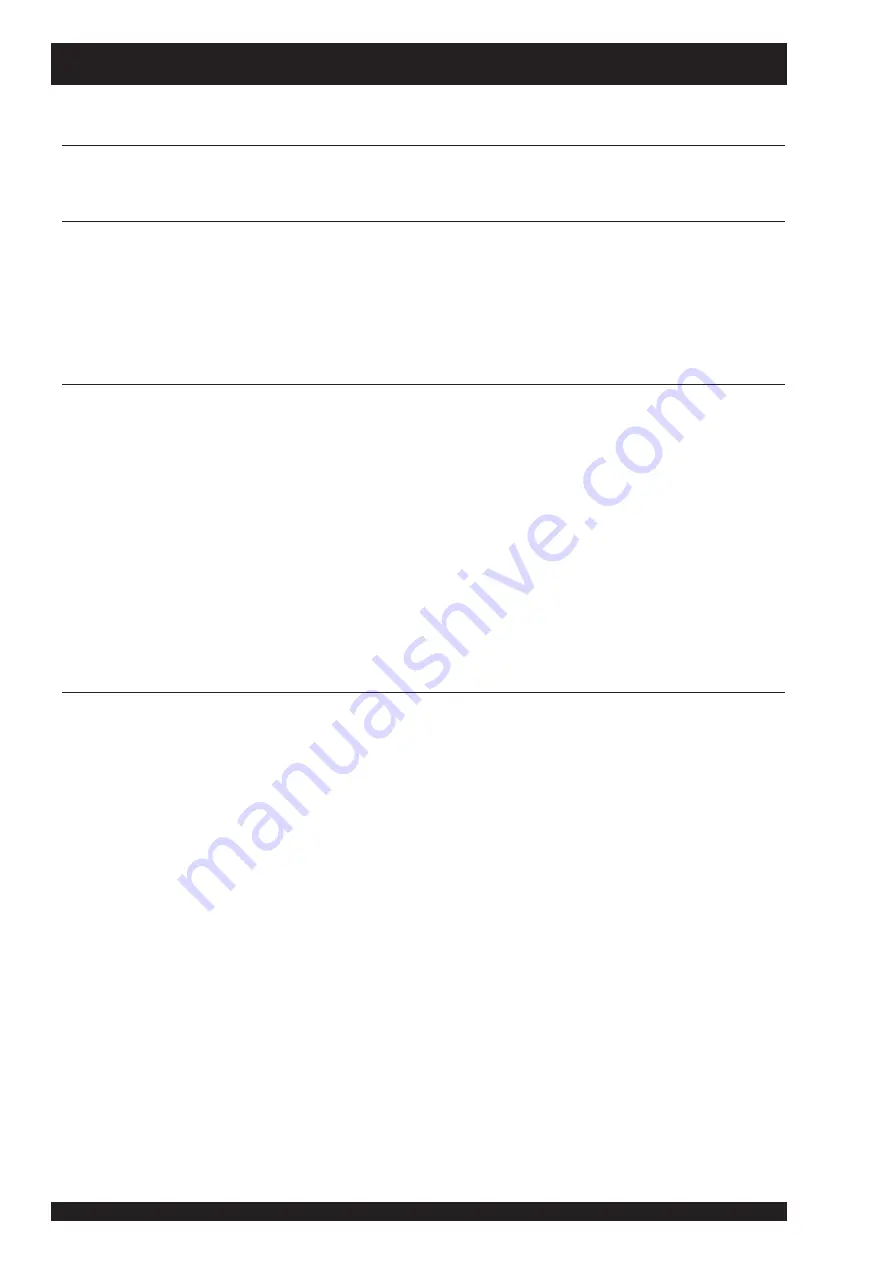
Page 10
500AS
IMA 551C
TROUBLE
CAUSE
WHAT TO DO
Machine fails to start
Check for:
Flat battery and/or faulty terminal connections.
Charge battery and/or clean terminals.
Key switch (4) faulty connection and/or loose wires.
Repair or replace
Starter Motor faulty (21).
Repair or replace
Machine starts but has
the following faults:
Voltage at AC outlet but
Check DC voltage across bridge rectifier (8). If there is
Replace
no voltage or reduced
no voltage or half voltage, bridge rectifier may have
voltage at welder output
open circuit in one or two diodes only.
studs.
If the above is O.K., then check:
Rheostat (9) for open circuit
Replace
Shunt coil (9A) for open circuit
Repair or replace
Bad connections
Repair
Field reversing switch (20) faulty
Repair or replace
There is not output from
Check fuses F1 and F4
Replace
either the AC outlet or
If F4 is blown also check bridge rectifier (8).
Replace
the welder output studs.
If the above are O.K., then check flashing circuit for
faults. Check there is battery voltage across rotor
brushes (12A) with key switch (4) turned midway
Between “On” and “Start” positions
If not check for:
Bridge rectifier (10,11) open circuit
Replace
Key switch (4) faulty
Replace
Poor connections
Repair
If the above are O.K., then check for:
Alternator brushes (12A) sticking or excessively
Free or Replace
worn
Dirty slip rings (12A)
Clean
Bridge rectifier (8) open or short circuited
Replace
Rotor (12) open or short circuit (rotor resistance
Repair or replace
approximately 11ohm)
Stator field windings (17) open or short circuit.
Repair or replace
Capacitors (13) faulty
Replace
Poor connections
Repair
Machine has low welding
Rectifier bridge (8) and (10,11) may be open circuited on
Replace bridge
output or fails to hold
one or two diodes only.
welding current constantly.
Rotor (12) or brushes (12A) may have a ground
Locate and remove ground
Engine speed low
No load 1780 rpm, Full load 1700 rpm
Main brush holder rocker (7) moved position
Realign drilled marker points
Commutator may be dirty (7A)
Refer maintenance section (page 5)
Two segments on commutator (7A) burnt (open in that
Repair or replace
coil)
Short circuit in armature (7A) 2 segments burnt in four
Locate fault using growler and repair or replace
locations 90° apart)
Main brushes excessively worn (7)
Replace brushes
Faulty capacitors (13)
Replace capacitors
Brush springs may be broken (7)
Replace brush springs
Field circuit may have variable resistance connections or
Check field current with ammeter to discover varying
intermittent open circuit, due to loose connections or
current. This applies to both the main
broken wires (17), (8), (9) or (9A)
generator and alternator
Electrode lead or work lead connections may be poor
Tighten all connections
Wrong grade of brushes may have been installed on
Fit correct Lincoln brushes
generator (7)
Field rheostat may be making poor contact and over-
Inspect rheostat. Clean out and if necessary increase
heating (9)
finger tension on contact arm by bending arm
Current-adjusting mechanism may not be operating
Check for loose or missing set screw in control handles
properly (5A
Current control brush holder contact springs may be worn
Inspect. Replace needed parts. Clean internal contact
out or missing. Contact surface may be dirty, rough or
surface of control device. Do not lubricate. Smooth up
pitted (5a)
roughened surface.
Current control brush holder support stud and mating
If brush holder internal contact surface is pitted and
contact surfaces may be dirty or pitted and burned (5A)
burned, replace the brush holder and support stud. If
the contact surface is dirty, clean off the brush holder
stud and internal contact surface. Apply mixture of
three parts of silicone grease and one part zinc powder
(by weight) to stud
TROUBLESHOOTING
READ IN CONJECTION WITH WIRING DIAGRAM AM3064MC on Page 18
Summary of Contents for SHIELD-ARC 500AS
Page 19: ......