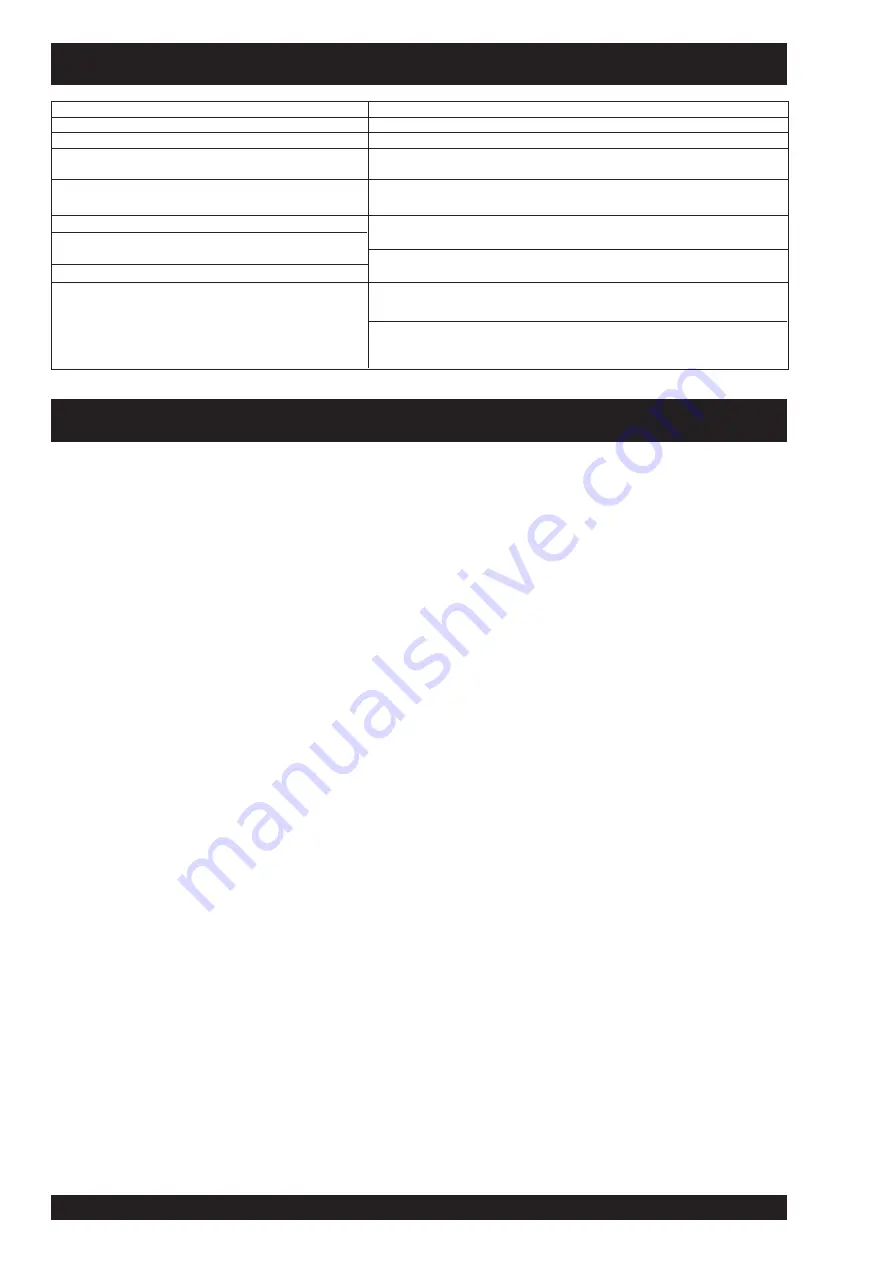
Page 6
500AS
IMA 551C
Engine
Welder
Model
Perkins 4/236 Diesel
Model
Shield-Arc
®
500AS KA1353
Capacity
3.86 litres (236 cu. ins.)
Rated Output
475 amps @ 40 arc volts and 60% duty cycle
Lubrication
High pressure forced feed from rotary
Rating to AS1966. 475 amps @ 39 arc volts and 60% duty cycle
type oil pump
380 amps @ 36 arc volts and 100% duty cycle
Cooling
Water cooling with circulation by
Welding Current
60-600 amps D.C.
centrifugal pump
Range
Governor
Mechanical, on injection pump
Speeds: No Load
1800 r.p.m.
Fuel Tank
64 litres. Sufficient for well over one day’s
Full Load
1750 r.p.m.
Capacity
operation under severe conditions
Weight (approx)
Without Trailer 930kg
Starting
12 volt battery and alternator
With Unsprung Trailer 1025kg
Auxiliary Power*
4,000 watts, 240 volt, 60 Hz., 100% duty cycle
A.C.
2,000 watts, 115 volt, 60 Hz., 100% duty cycle
* Available while welding at currents up to rated output.
N.B.: If 240 volt and 115 volt supply are being used simultaneously the total current draw should
not exceed 16.5 amps.
All diesel engines require some additional care for about the
first 50 hours operation. While maximum load can be applied to
a new engine as soon as it is put into service and the coolant
temperature has reached at least 60°C, care should be taken that
the engine is not run at very light loads (say less than 2.4 kVA, or
a 10 amp radiator) for extended periods, as this can lead to
glazing of the cylinder bores. Do not operate at high speeds
without a load, and do not overload the engine. Cylinder glazing
can lead to excessive oil consumption and smoky exhaust, while
overloading during the first few hours can lead to excessive wear
and shorten the life of the engine.
See the engine manufacturer’s operating manual supplied
with the welder for detailed engine operating and
maintenance instructions, parts lists and safety precautions.
Engine Operation
On receipt of 500AS, remove “Gold Seal” or “Care-card” label
from engine, add Ownership details, and mail to nearest Perkins
Distributor. The Distributor will return a plastic Care-card - which
must be retained and presented should warranty service be
required. Note that Care-card is accepted World-wide.
Before attempting to start the welder the following should be
carried out:
1.
Remove the protective seals from the motor and fit the air
cleaner and exhaust silencer. Air cleaner and exhaust
fittings are packed inside the machine canopy, on fuel tank
rails behind the control panel.
2.
Ensure the crankcase oil level is at the “Full” mark on the
dipstick. Use the grade of oil recommended by the engine
manufacturer.
N.B. Many oil companies market a product which
meets the recommended MIL-L-46152 (SE CC) and the
heavy duty and turbocharged engine specification MIL-
L-2104C (SE CD). These oils are not recommended for
use in this welder, particularly in the initial 50 hours of
operation.
3.
Fill the radiator. (Use a 50-50 mixture of water and glycol,
premixed, if operating in temperatures near or below zero.)
4.
Fill the fuel tank (always use clean fuel).
5.
The battery supplied with the welder is dry charged. Fill with
the electrolyte and boost charge as per the instructions on
page 7.
6.
In the case of a new engine or an engine which has been
standing idle for any length of time, it is important to bleed
the fuel system. Refer to the engine instruction manual for
the correct procedure.
To start the welder - Turn the start switch to the “H” position for 15-
20 seconds, then turn further in the clockwise direction to the
“start” position. If the engine does not start after 20 seconds,
return the switch to the “H” position for 10 seconds and then
return to the “start” position. As soon as the engine starts, the start
switch must be released and allowed to return to the “on” position.
Do not turn the start switch to the “start” position while the engine
is running. To do so may cause circuit or component damage. If
the engine is warm and has only been stopped for a short period,
restart by turning the start switch directly on to the “start” position,
and releasing when the engine starts. Note: The “H” position is
midway between the “on” position and the “start” position. A
definite spring loaded location can be felt at the “H” position.
If the oil pressure gauge does not show normal oil pressure
(207/414kPa) 10 seconds after starting, stop the engine and
consult the engine instruction manual.
Before any welding current can be drawn from the unit, the
polarity switch must be placed in Ele or Electrode -
position.
To stop the engine - Turn the key switch to off position.
The engine speed has been pre-set in the factory for optimum
welder performance and the fuel pump and governor then sealed.
This setting should not be altered and to do so will void warranty.
OPERATING INSTRUCTIONS
SPECIFICATIONS
Summary of Contents for SHIELD-ARC 500AS
Page 19: ......