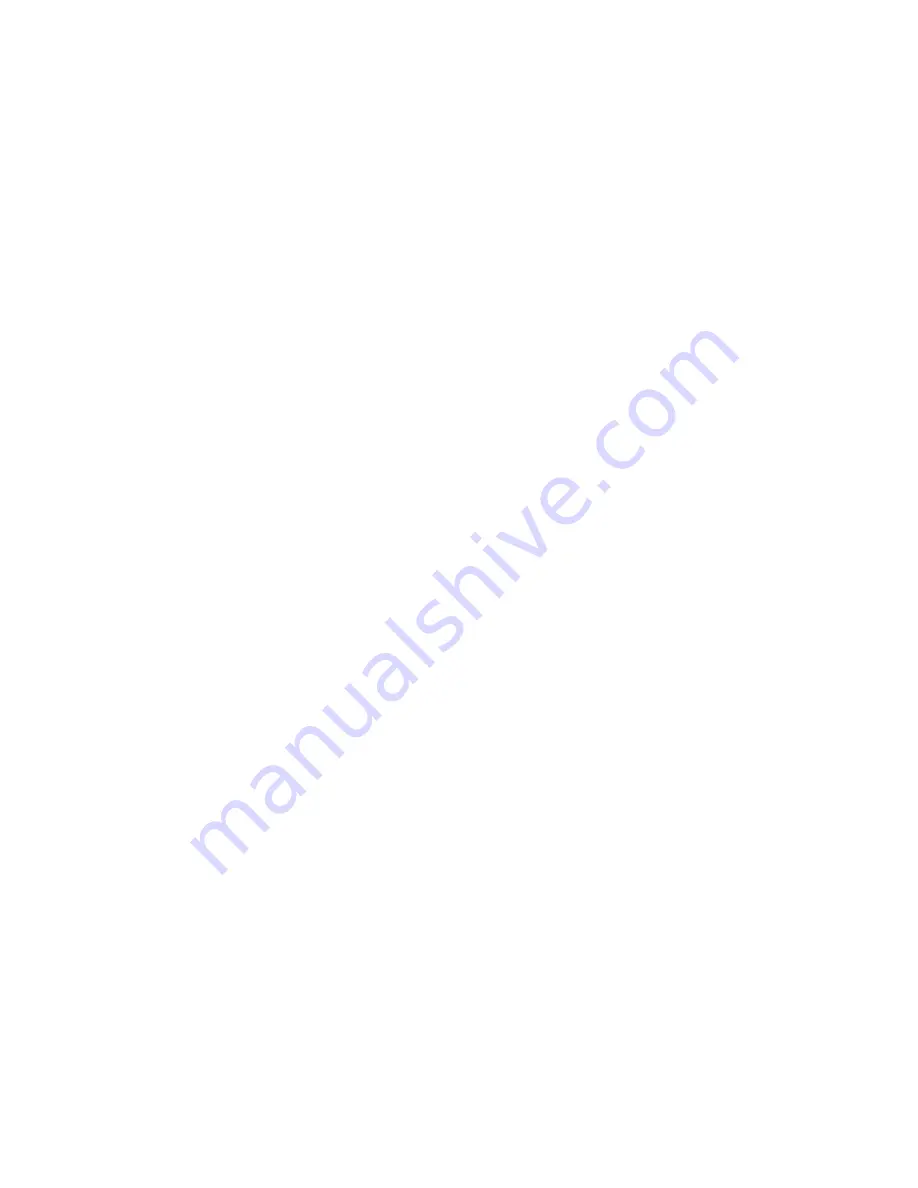
Page 75 of 80
Warranty
There is an 18 months’ warranty on TECHLINE products against manufacturing faults calculated from the
production date of the individual products (see label). LINAK’s warranty is only valid in so far as the equipment
has been used and maintained correctly and has not been tampered with. Furthermore, the actuator must not
be exposed to violent treatment. In the event of this, the warranty will be ineffective/invalid. For further details,
please see standard terms of sale and delivery for LINAK A/S.
Note:
Only an authorised LINAK
®
service centre should repair LINAK actuator systems. Systems to be repaired under
warranty must be sent to an authorised LINAK service centre.
In order to avoid the risk of malfunction, all actuator repairs must only be carried out by an authorised LINAK
Service shop or repairer, as special tools and parts must be used.
If a system is opened by unauthorised personel there is a risk that it may malfunction at a later date.
The actuator is not to be opened by unauthorised personnel. In case the actuator is opened, the warranty will be invalid.