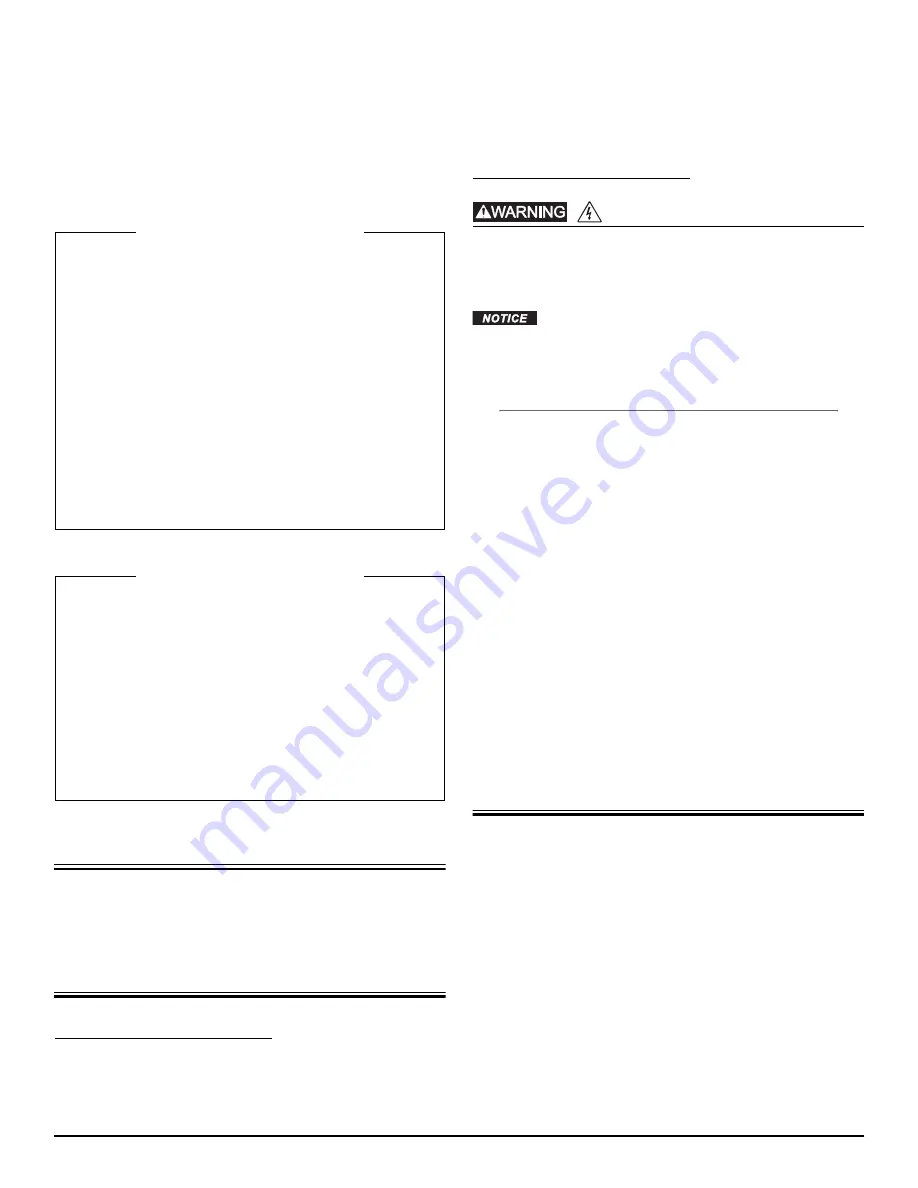
4 | EN
Copyright © Liberty Pumps, Inc. 2021 All rights reserved.
5647000M
Submersible Pump—do not run dry
Keep pump upright.
At no time should the pump be stored within an incomplete
wet pit. The pump should not be placed into the pit until it
can be fully operational.
Do not allow the pump to freeze.
Before installation, read these instructions carefully. Each
pump is individually factory tested to ensure proper
performance. Closely following these instructions will
eliminate potential operating problems, assuring years of
trouble-free service.
The LSG/LSGX-Series pumps are to be used for handling
septic tank effluent, sewage, and drain (storm) water.
Provide pump serial number in all correspondence.
Pumps are CSA certified to CSA and UL® standards.
Pumps must be serviced at a qualified repair facility
approved by Liberty Pumps. No repair work should be
carried out during the warranty period without prior factory
approval. Any unauthorized field repairs void warranty.
Contact Liberty Pumps at 1-800-543-2550 to locate the
closest authorized service center.
It is extremely important to verify that the pump has been
sized correctly for the intended installation. The operating
point of the pump must lie within the acceptable range as
outlined by the applicable Liberty Pumps performance chart.
Operating the pump outside of the recommended range
can invalidate the CSA Certification of the pump and can
also cause damage and premature failure. Operating
outside of the recommended range can cause the pump to
exceed its rated nameplate amp draw, which will void the
pump certification. It can also cause motor overheating,
cavitation, excessive vibration, clogging, and poor energy
efficiency.
Model Specifications
For complete listing of models and their specifications, refer to
http://www.LibertyPumps.com/About/Engineering-Specs. Pump
nameplate provides a record of specific pump information.
Inspection and Storage
Initial Inspection
The pump should be immediately inspected for damage that may
have occurred in shipment.
1.
Visually check the pump and any spare parts for damage.
2.
Check for damaged electrical wires, especially where they exit
the motor housing.
Contact Liberty Pumps customer service to report any damage or
shortage of parts.
Storage Before Use
Protect the power and control cords from the environment.
Unprotected power and control (switch) cords can allow water
to wick through ends into pump or switch housings, causing
surroundings to become energized.
At no time shall the pump be stored within an incomplete wet
pit. The pump shall not be placed into the pit until it can be
fully operational.
Do not allow the pump to freeze.
LSG/LSGX-Series Omnivore grinder pumps are shipped from the
factory ready for installation and use. The pump should be held in
storage if the pump station is not complete.
If storage is necessary, the pump should remain in its shipping
container. It should be stored in a warehouse or storage shed that
has a clean, dry temperature-stable environment where the pump
and its container are covered to protect it from water, dirt,
vibration, etc. The cord ends must be protected against moisture.
Uninstalled
pumps that are idle for greater than three months
should have cutters and impellers manually rotated once a month
to lubricate the seals.
Installed
pumps that are idle for greater than one month should
have impellers and cutters manually operated through the breaker
panel once a month to lubricate the seals.
For automatic models
,
turn off the breaker, unplug the piggyback switch, and plug the
pump directly into receptacle. Turn the breaker on for 30 seconds,
then turn the breaker off. Plug the piggyback switch back in. Refer
to
.
Pumps that are idle in a wet basin must be removed.
Pump Design
LSG/LSGX-Series grinder pumps are designed for continuous
underwater operation. The motor and pump form a close coupled,
watertight unit. The induction motor is insulated against heat and
moisture in accordance with Class B 265°F (130°C) regulations.
A thermal overload protector is embedded in the stator windings.
This is connected in series and wired to shut down the pump if
overheating occurs. The overload switch resets automatically
when the motor cools.
The motor is protected against damage from water entry by two
seals. The lower seal is a Viton lip seal and the upper seal is a
graphite impregnated silicon carbide hard face seal.
The impeller and volute are designed for efficient flow
characteristics and clog-free operation. The hardened cutters
grind solids and fibrous matter into small particles that can be
safely pumped through small diameter piping.
General Information
Operating Constraints
RISK OF ELECTRIC SHOCK