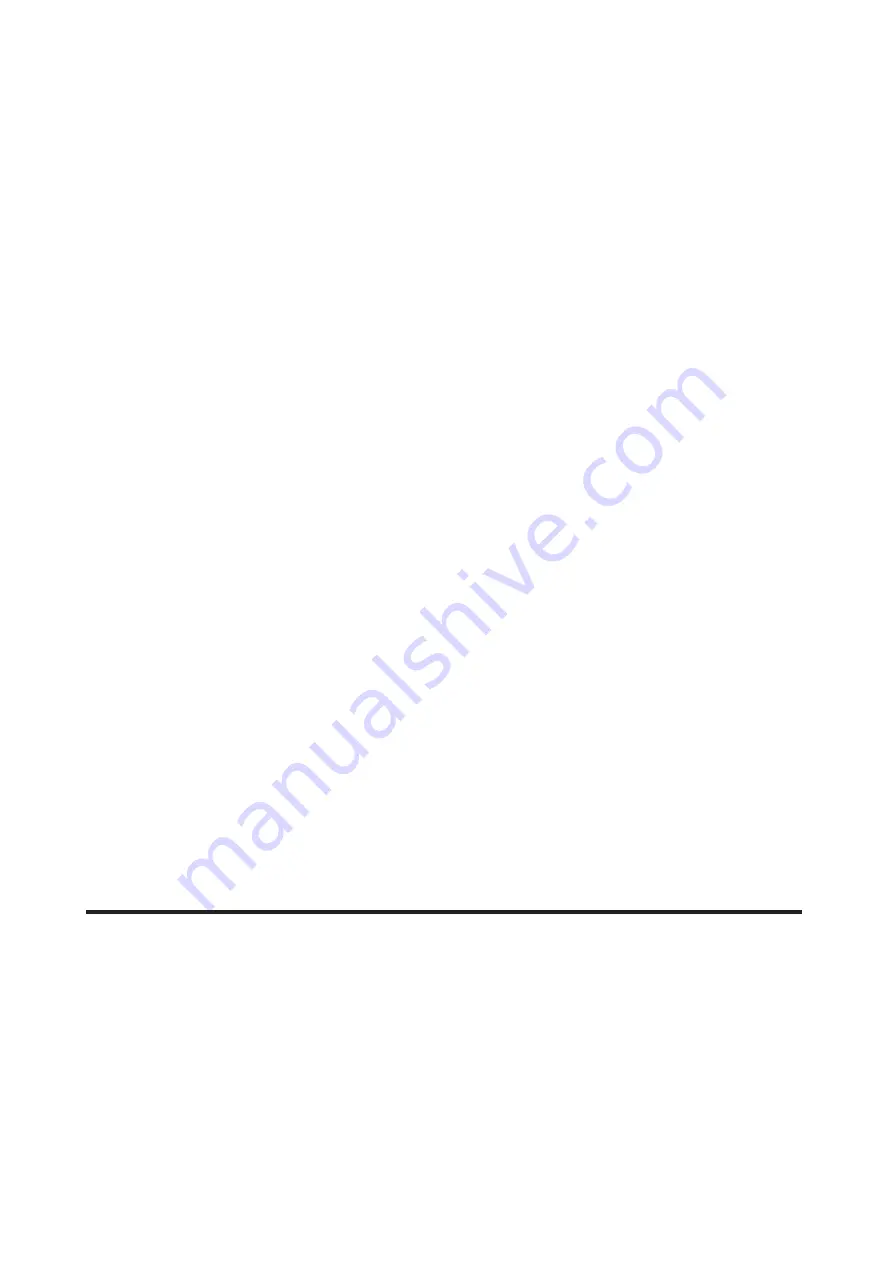
Mobile Elevating Work Platform
Maintenance Manual
880*1230 mm sixteen format 8 printed sheet
Fourth edition and printed for the first time in December 2021
LINGONG GROUP JINAN HEAVY MACHINERY CO.,LTD
Add: F12,Building 3 LushangGuoao Plaza, 9777 Jingshi Road,Lixia District, Jinan,
Shandong, 250000,China
Tel: 86-0531-67605017
Technical service: 86-0531-67605017
Fax: 86-0531-67605017
Accessory sales: 86-0531-67605016
Summary of Contents for AS0607E
Page 6: ...Maintenance Manual of Elevating Work Platform 1 Chapter 1 Maintenance...
Page 7: ...Maintenance Manual of Elevating Work Platform 2...
Page 33: ...Maintenance Manual of Elevating Work Platform 28...
Page 34: ...Maintenance Manual of Elevating Work Platform 29 Chapter 2 Appendix...
Page 35: ...Maintenance Manual of Elevating Work Platform 30...
Page 36: ...Maintenance Manual of Elevating Work Platform 31 2 1Battery Maintenance Schedule...
Page 41: ...Maintenance Manual of Elevating Work Platform 36 SS0407E SS0507E HYDRAULIC SCHEMATIC...
Page 42: ...Maintenance Manual of Elevating Work Platform 37 AS0607E HYDRAULIC SCHEMATIC...
Page 43: ...Maintenance Manual of Elevating Work Platform 38 AS0812E HYDRAULIC SCHEMATIC...
Page 44: ...Maintenance Manual of Elevating Work Platform 39 AS1012E AS1212E HYDRAULIC SCHEMATIC...
Page 45: ...Maintenance Manual of Elevating Work Platform 40 AS1413E HYDRAULIC SCHEMATIC...
Page 46: ...Maintenance Manual of Elevating Work Platform 41 SS07E ELECTRIC SCHEMATIC...
Page 47: ...Maintenance Manual of Elevating Work Platform 42 AS07E AS08E AS12E ELECTRIC SCHEMATIC...
Page 48: ...Maintenance Manual of Elevating Work Platform 43 AS1413E ELECTRIC SCHEMATIC...