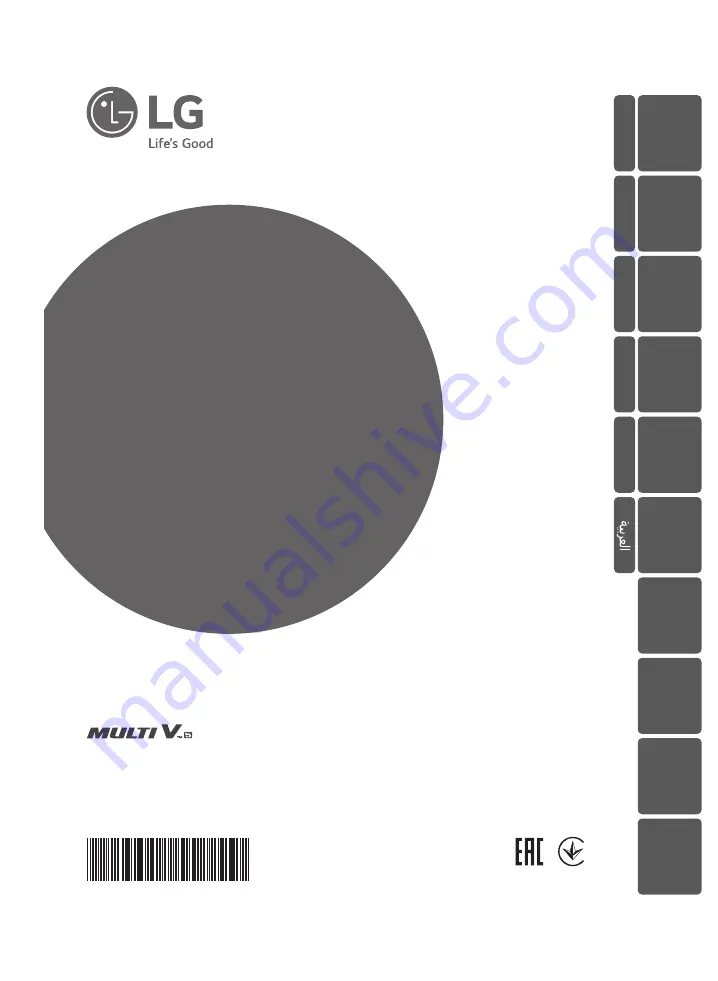
INSTALLATION MANUAL
AIR
CONDITIONER
www.lg.com
MFL32987320
Rev.01_011719
Please read this installation manual completely before installing the product.
Installation work must be performed in accordance with the national wiring
standards by authorized personnel only.
Please retain this installation manual for future reference after reading it thoroughly.
[Representative] LG Electronics Inc. EU Representative : LG Electronics European Shared Service Center B.V.
Krijgsman 1, 1186 DM Amstelveen, The Netherlands
[Manufacturer] LG Electronics Inc. Changwon 2nd factory 84, Wanam-ro, Seongsan-gu, Changwon-si,
Gyeongsangnam-do, KOREA
PRHR083/PRHR063/PRHR043/PRHR033/PRHR023 (Heat Recovery Unit)
Original instruction
Copyright © 2017 - 2019 LG Electronics Inc. All Rights Reserved.
ENGLISH
ITALIANO
ESPAÑOL
FRANÇAIS
DEUTSCH
ΕΛΛΗΝΙΚΆ
ČEŠTINA
NEDERLANDS
POLSKI
LIMBA ROMÂNĂ
РУССКИЙ ЯЗЫК
УКРАÏНСЬКА
ҚАЗАҚ ТІЛІ
БЕЛАРУСКАЯ МОВА
O
‘
ZBEK TILI
Summary of Contents for Multi V PRHR023
Page 28: ...28 ENGLISH ...