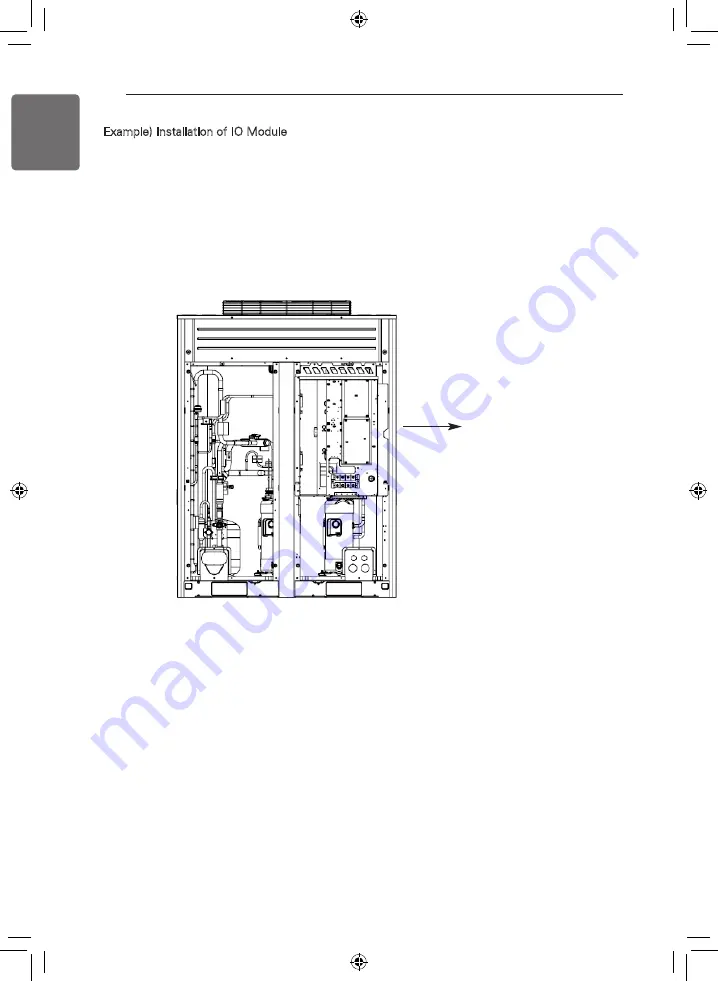
62
ELECTRICAL WIRING
ENGLISH
Example) Installation of IO Module
Installation Method
1. Separate front panel from outdoor unit.
2. Separate front cover of control box.
3. Assemble the IO Module with screws(12 mm*2EA) on designated location.
4. Connect the connection wires according to the instructions.
(Please refer to Setting and Using Method which is included in IO Module Installation Manual)
Location of IO Module