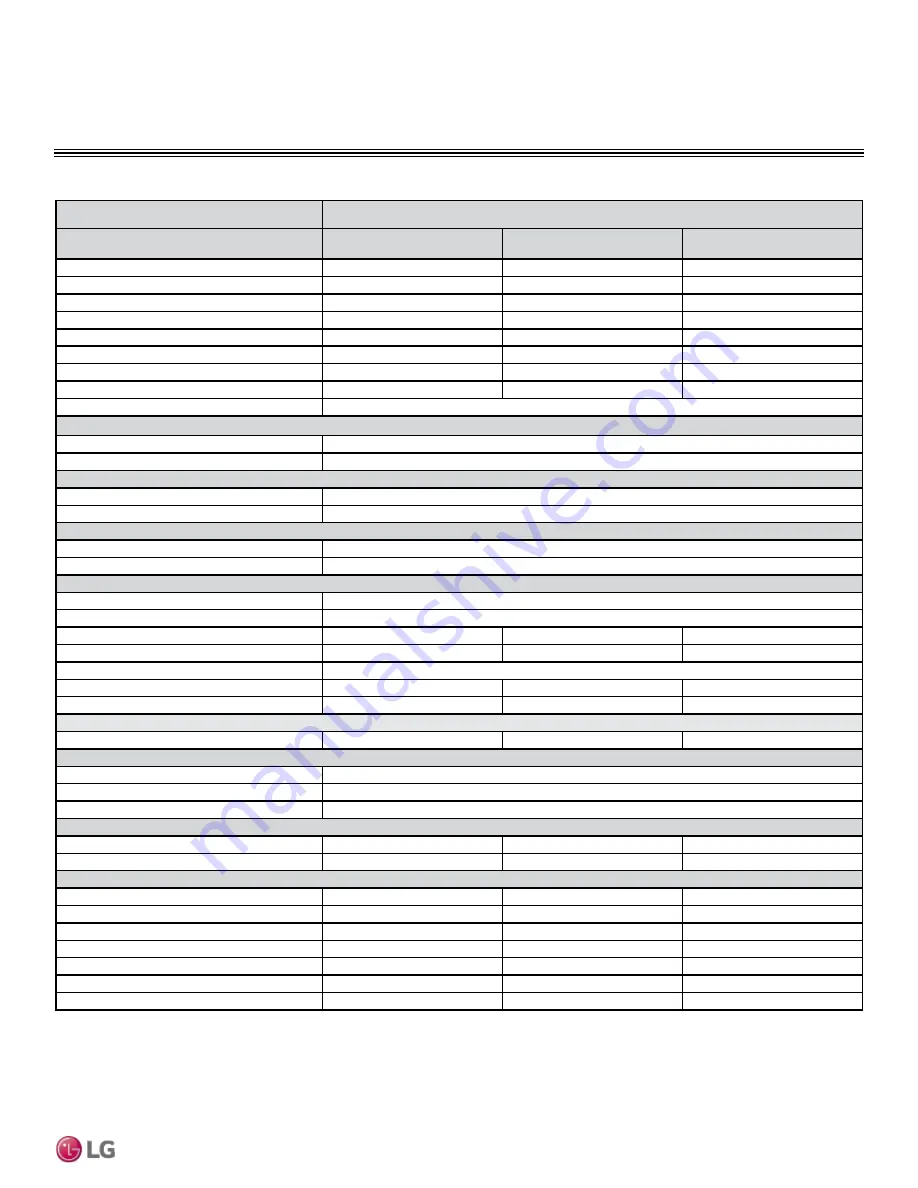
Due to our policy of continuous product innovation, some specifications may change without notification.
©LG Electronics U.S.A., Inc., Englewood Cliffs, NJ. All rights reserved. “LG” is a registered trademark of LG Corp.
9
Product Data
GENERAL DATA
Single Zone Art Cool Mirror Specifications
Table 1:
Single-Zone Art Cool Mirror System Specifications.
Type
Single-Zone Art Cool Mirror Units
System Model Number (IDU/ODU)
LA090HSV4
(LAN090HSV4/LSU090HSV4)
LA120HSV4
(LAN120HSV4/LSU120HSV4)
LA180HSV4
(LAN180HSV4/LSU180HSV4)
Nominal Cooling Capacity
9,000
11,200
18,200
Cooling Power Input
1
(kW)
0.68
0.90
1.45
Nominal Heating Capacity (Btu/h)
10,800
13,300
22,000
Heating Power Input
1
(kW)
0.70
1.0
1.76
COP
4.51
3.90
3.66
EER
13.29
12.5
12.58
SEER
21.5
21.5
20.5
HSPF
10.8
11.0
9.7
Power Supply (V/Hz/Ø)
208-230/60/1
Outdoor Unit Operating Range
2
Cooling (°F DB)
14 to 118
Heating (°F WB)
-4 to 65
Indoor Unit Operating Range
Cooling (°F WB)
53 to 75
Heating (°F DB)
60 to 86
Indoor Temperature Setting Range
Cooling (°F)
64 to 86
Heating (°F)
60 to 86
Unit Data
Refrigerant Type
3
R410A
Refrigerant Control
EEV
IDU Sound Pressure
4
dB(A) (H/M/L/Sleep)
38/33/23/19
39/33/23/19
45/40/35/29
ODU Sound Pressure
4
dB(A)
45
45
53
Power/Communication Cable
5
(No. x AWG)
4 x 18
IDU Net/Shipping Weight (lbs.)
24/29
24/29
32/39
ODU Net/Shipping Weight (lbs.)
75/79
75/79
121/131
Compressor
Compressor Type (Qty)
Single Rotary (1)
Single Rotary (1)
Twin Rotary (1)
Fan
IDU Type (Qty)
Cross Flow (1)
ODU Type (Qty)
Propeller (1)
Motor/Drive
Brushless Digitally Controlled/Direct
Airflow Rate
IDU Max/H/M/L (CFM)
423/353/272/191
423/353/272/191
735/622/509/339
ODU Max (CFM)
1,165
1,165
2,119
Piping
Liquid Line (in, OD)
1/4
1/4
3/8
Vapor Line (in, OD)
3/8
3/8
5/8
Condensation Line (OD, ID)
27/32, 5/8
27/32, 5/8
27/32, 5/8
Additional Refrigerant Charge (oz/ft)
0.22
0.22
0.38
Pipe Length
6
(Minimum/Maximum)(ft)
6.6/65.6
6.6/65.6
9.84/98.4
Piping Length
6
(no add’l refrigerant, ft)
41.0
41.0
24.6
Max Elevation Difference (ft)
32.8
32.8
49.2
EEV: Electronic Expansion Valve IDU: Indoor Unit ODU: Outdoor Unit
1
Power Input is rated at high speed.
2
Optional Low Ambient Wind Baffle Kit allows operation down to 0°F in cooling mode.
3
Take appropriate actions at the end of HVAC equipment life to recover, recycle, reclaim or destroy R410A
refrigerant according to applicable regulations (40 CFR Part 82, Subpart F) under section 608 of CAA.
4
Sound Pressure levels are tested in an anechoic chamber under ISO Standard 3745.
5
All power wiring/communication cables are field supplied and are to be minimum 18 AWG, 4-conductor,
stranded, shielded and must comply with applicable local and national codes.
6
Piping lengths are equivalent.
This unit comes with a dry helium charge.
This data is rated 0 ft above sea level with 24.6 of refrigerant line per indoor unit and a 0 ft level
difference outdoor and indoor units.
Cooling capacity rating obtained with air entering the indoor unit at 80ºF dry bulb (DB) and 67ºF wet
bulb (WB) and outdoor ambient conditions of 95ºF dry bulb (DB) and 75ºF wet bulb (WB).
Heating capacity rating obtained with air entering the indoor unit at 70ºF dry bulb (DB) and 59ºF wet
bulb (WB) and outdoor ambient conditions of 47ºF dry bulb (DB) and 43ºF wet bulb (WB).