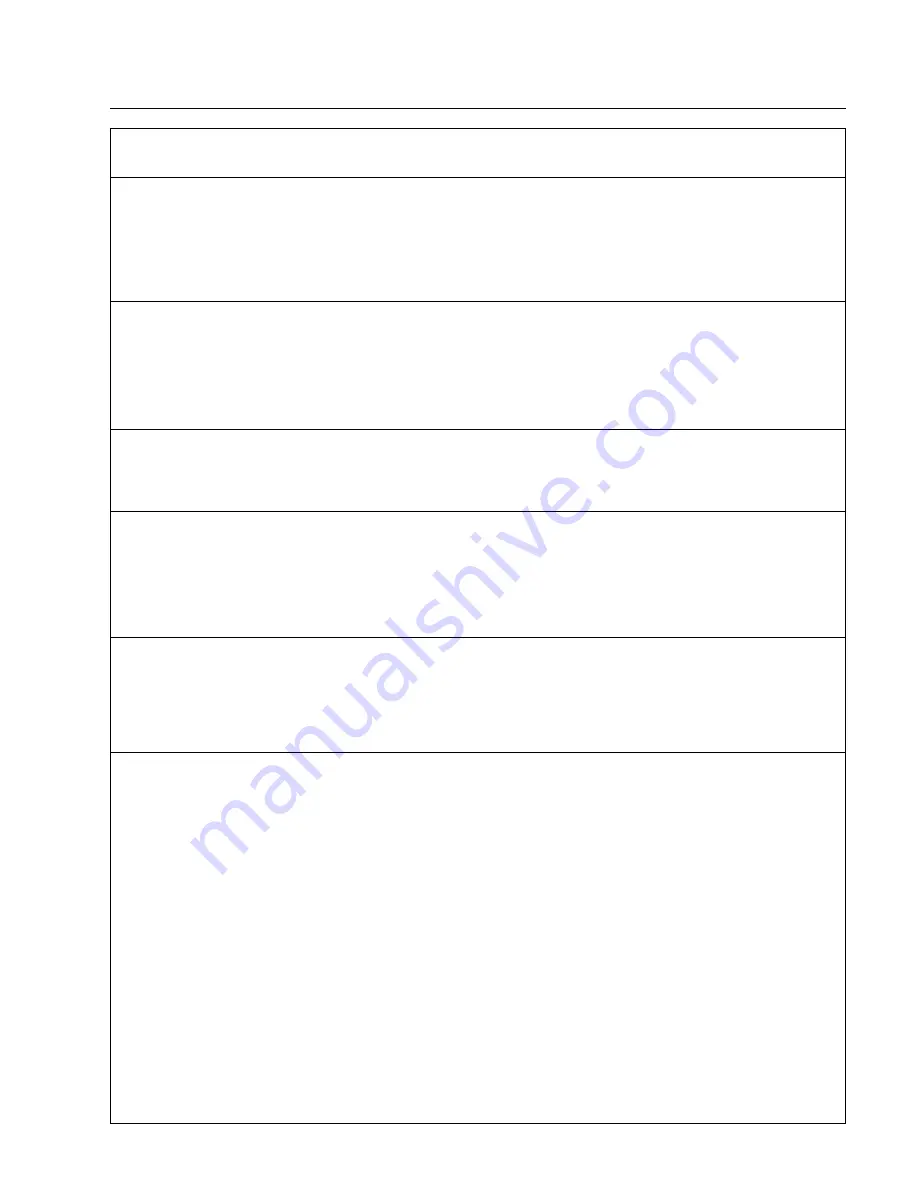
Troubleshooting
55
GA 05.139/1.02 - 06/99
Failure Message on
Display
Bearing Temp. SC
The magnetic bearing tem-
perature sensor reads a tem-
perature lower than 1
°
C.
Motor Temp. SC
The motor temperature sen-
sor reads a temperature
lower than 1
°
C.
Connection pump
Frequency XX*
Abnormal motor current or
frequency
*XX is a code no. between
43 and 55. It helps the Ley-
bold service to find the
cause of the failure.
No Motor Current
TMS 1
The converter measures a
heating current of less than
300 mA when heater is on.
Measures
Repeat step 1 of „failure Bearing Temp.“.
Contact Leybold service if the resistance of
the sensor is less than 100
Ω
.
Repeat step 2 of „failure Bearing Temp.“.
Contact Leybold service if the resistance of
the sensor is less than 100
Ω
.
Contact Leybold service.
Repeat step 1 of „failure Motor Temp.“.
Contact Leybold service if the resistance of
the sensor is less than 1.62 k
Ω
.
Repeat step 2 of „failure Motor Temp.“.
Contact Leybold service if the resistance of
the sensor is less than 1.62 k
Ω
.
Contact Leybold service.
Check if the BEARING cable is connected to
the pump and the converter. Acknowledge
failure message.
Contact Leybold service.
Acknowledge failure message. If failure per-
sists contact Leybold service.
Contact Leybold service.
Check cables and connectors, straighten
pins if required.
Deactivate „Emergency off“ via control plug
X14 and acknowledge failure message.
Reconnect or replace DRIVE cable.
Step 1: Check fuse
Replace fuse TMS (F4A, 5x20 mm) if blown.
Step 2: Check pump (heating element)
Check if the connector of the heating ele-
ment is connected.
Check pump connector X30. In particular
measure resistance between pins X30/A and
X30/B. The resistance is typically between
70
Ω
and 75
Ω
. In case abnormal values are
measured contact Leybold service.
Step 3: Check TMS/DRIVE cable
If step 2 was successful do the following:
Check TMS/DRIVE cable for bent pins
Measure resistance between pins X21/b and
X21/d with the cable connected to the pump.
The resistance is typically between 70
Ω
and 75
Ω
.
Replace the cable if it is damaged or in case
the measurement of the resistance shows
abnormal values now.
Contact Leybold service.
Possible Cause
Temperature sensor Pt 100 short-circuited.
BEARING cable short-circuited.
Converter failure.
Temperature sensor KTY short-circuited.
BEARING cable short-circuited.
Converter failure.
BEARING cable not connected.
Converter failure.
The rotor frequency exceeds 515 Hz.
Converter failure.
On START command: DRIVE cable not
connected or connectors damaged.
Resultant message after activating „Emer-
gency off“.
DRIVE cable interrupted during operation of
the MAG.
Fuse TMS blown.
Heating element or internal pump connec-
tion damaged.
TMS/DRIVE cable or connectors damaged.
Converter failure.
Summary of Contents for MAG W 2010 CHT
Page 63: ...Notes 63 GA 05 139 1 02 06 99...