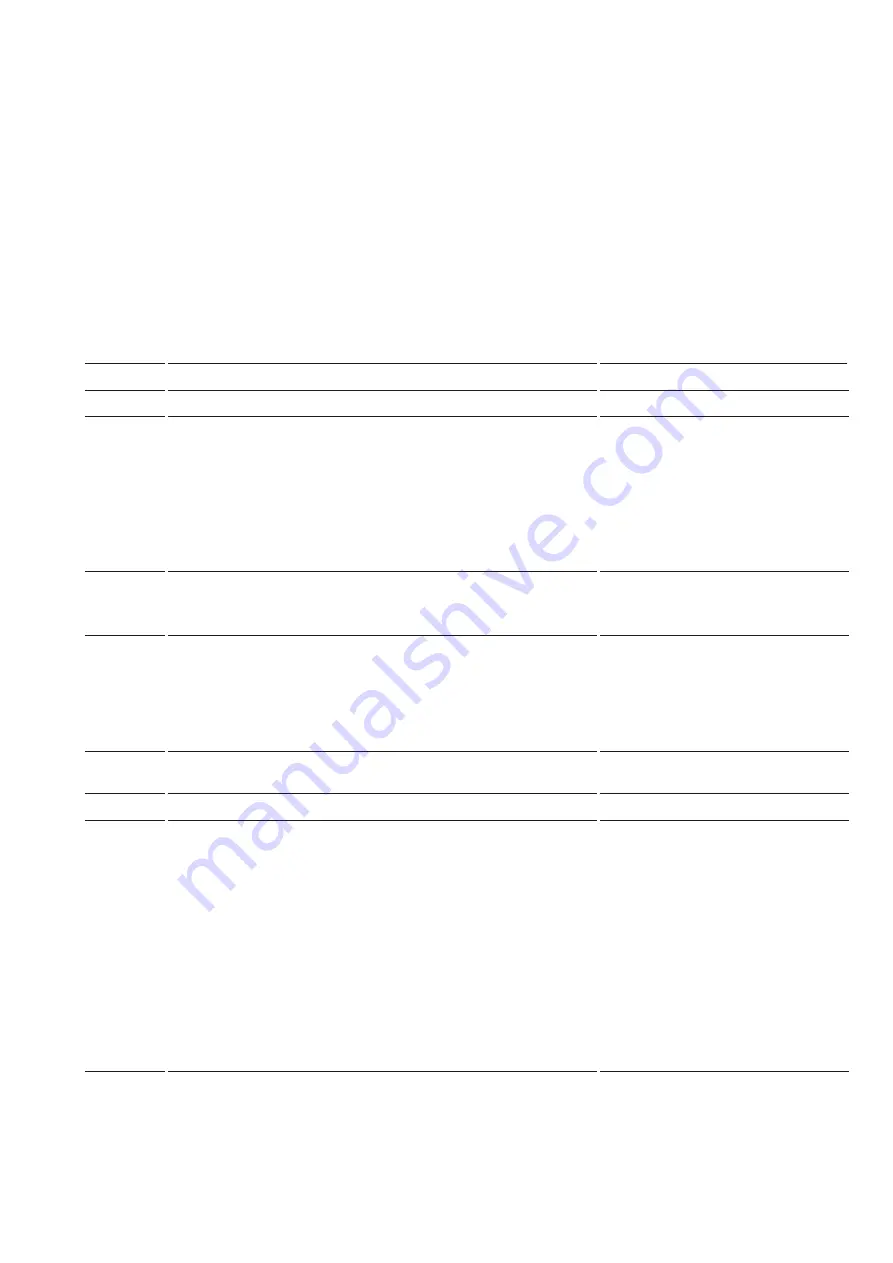
Troubleshooting
95
300314330_002_C7 - 05/2021 - © Leybold
Operator Programming Errors
An Operator Programming Error (OPE) occurs when an inapplicable parame-
ter is set or an individual parameter setting is inappropriate. When an OPE
error is displayed, press the ENTER button to display U1-18 (OPE fault con-
stant). This monitor will display the parameter that is causing the OPE error.
Error mes-
sage
Possible cause
Corrective Action
oPE01
Drive capacity and value set to o2-04 do not match.
Correct the value set to o2-04.
oPE02
Parameters were set outside the allowable setting range.
Set parameters to the proper values.
oPE03
A contradictory setting is assigned to multi-function contact inputs
H1-01 through to H1-06.
The same function is assigned to two inputs. (this excludes “External
fault” and “Not used”)
Input functions which require the setting of other input functions were
set alone.
Input functions that are not allowed to be used simultaneously have
been set.
Fix any incorrect settings.
oPE05
The run command source (b1-02) or frequency reference source (b1-01)
is set to 3 but no option board is installed.
The frequency reference source is set to pulse input but H6-01 is not 0.
Install the required option board.
Correct the values set to b1-01 and
b1-02.
oPE07
Settings to multi-function analog inputs H3-02 and H3-10 and PID func-
tions conflict.
H3-02 and H3-10 are set to the same value. (this excludes settings “0”
and “F”)
PID functions have been assigned to both analog inputs and the pulse
input at the same time.
Fix any incorrect settings.
oPE08
A function has been set that cannot be used in the control mode select-
ed.(might appear after control mode change)
Fix any incorrect settings.
oPE10
The V/f pattern setting is incorrect.
Check the V/f pattern settings.
oPE12
Occurs if b1-01 (Frequency Reference) = 3 or b1-02 (Sequence
Reference) =3 and Leybold Parameters Lower Level is set and option
card is connected.
Occurs if following condition is not given:
P2-02 < P2-04 < P2-06 < P2-08 < P2-10 < P2-12
< P2-14 < P2-16 < P2-18 < P2-20 < P2-22.
Occurs if following condition is not given:
P4-01 < P4-02 < P4-03
Occurs if MFDI setting in H1-02 is not an external fault setting and
P1-05 is unequal to 0.
((H1-02 < 20h) OR (H1-02 > 2Fh)) AND (P1-05 NOT 0)
Occurs if MFDI setting in H1-03 is not an external fault setting and
P1-06 is unequal to 0.
((H1-03 < 20h) OR (H1-03 > 2Fh)) AND (P1-06 NOT 0)