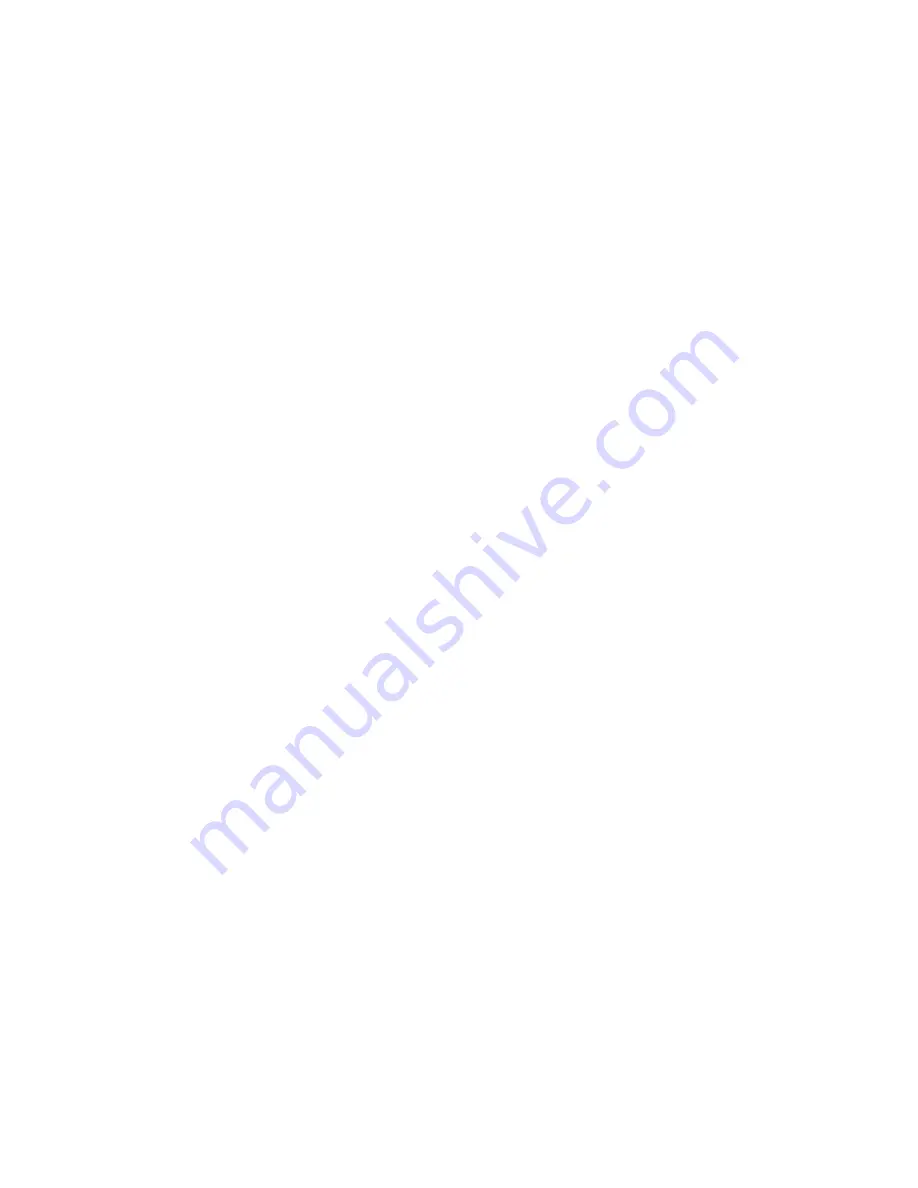
X-2
EOF
Exit Roller
Front Cover
Gear Plate
Gutter Pad
Large Feed Roller
Maintenance Station
Mid Frame
Operator Panel
Paper Feed Motor
Printhead Cable & Cradle
Rear Cover
Sheet Feeder
Small Feed Roller Holder
Small Feed Rollers
Star Wheel Roller Assembly
System Board
Temperature Sensor
Wipers & Caps
Repair Information
S
Safety Information
Service Checks
Carrier Transport
Envelope Feed
Maintenance Station
Paper Feed
Paper Path
Power
Print Quality
Start
Symptom Table (POST)
Symptom Tables
T
Tests
Encoder
End of Forms (EOF)
NVRAM Dump
Test Page
Part Numbers
11B6073
11B6074
11B6075
11B6076
11B6077
14R0145
14R0147
14R0149
14R0151
14R0153
14R0154
14R0156
14R0157
14R0159
14R0160
14R0161
14R0163
14R0164
14R0165
14R0166
14R0167
14R0168
14R0169
14R0170
14R0171
14R0175
14R0176
14R0179
14R0180
14R0181
14R0182
14R0183
14R0184
14R0185
14R0187
14R0189
14R0190
14R0191
14R0192
14R0193
14R0194
17A0124
17A0125
7350234
Summary of Contents for Z51 Color Jetprinter
Page 10: ...x Service Manual ...
Page 28: ...2 16 Service Manual 4098 001 ...
Page 48: ...6 2 Service Manual 4098 001 ...
Page 50: ......
Page 52: ...7 4 Service Manual 4098 001 Assembly 2 Frames ...
Page 54: ...7 6 Service Manual 4098 001 Assembly 3 Paper Feed ...
Page 56: ...7 8 Service Manual 4098 001 Assembly 3 cont Paper Feed ...
Page 58: ...7 10 Service Manual 4098 001 Assembly 4 Electronics ...
Page 60: ...7 12 Service Manual 4098 001 Assembly 5 Carrier ...
Page 62: ...7 14 Service Manual 4098 001 Assembly 6 Carrier Transport ...
Page 64: ...7 16 Service Manual 4098 001 Assembly 7 Maintenance Station ...
Page 66: ...7 18 Service Manual 4098 001 ...