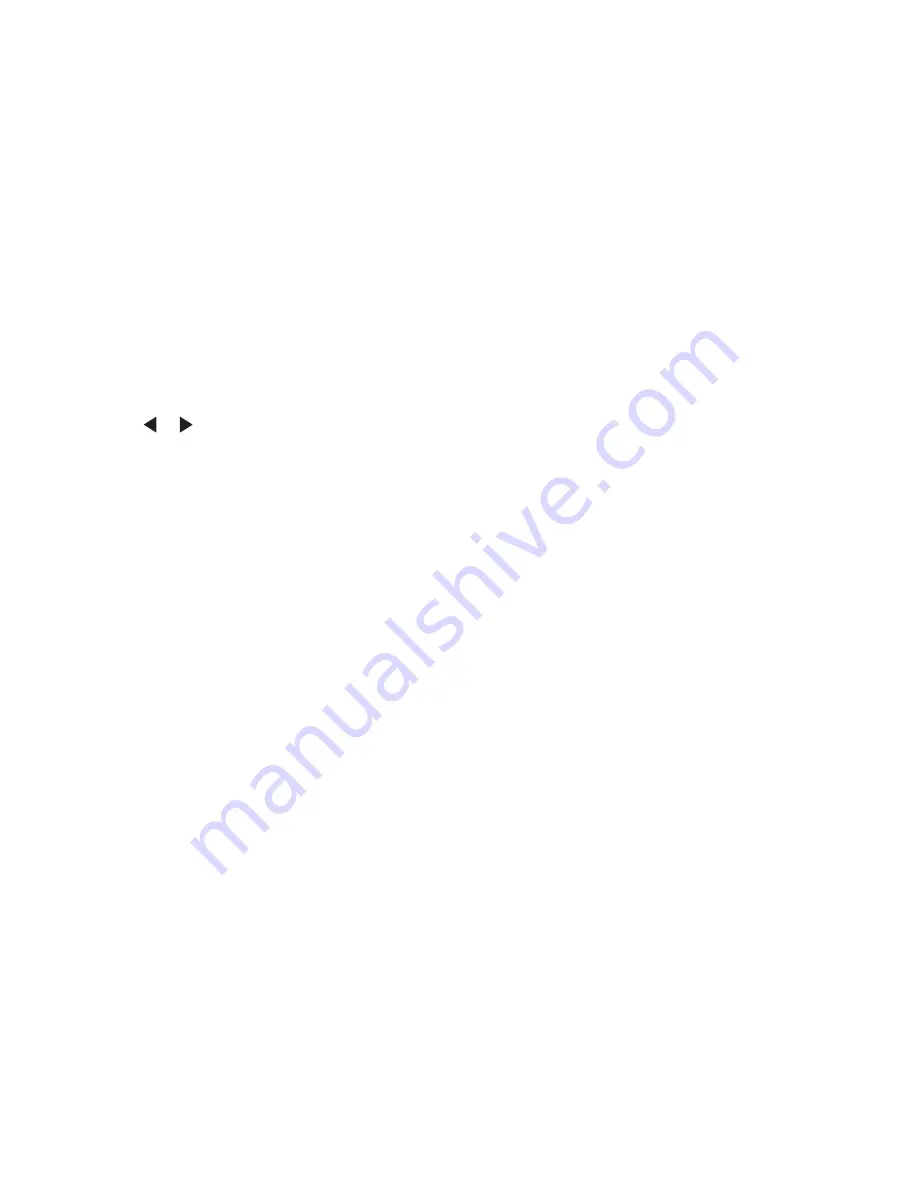
Installed Licenses
This setting prints a report that lists the currently installed licenses and the feature data of each license.
To print the menu settings page:
From the Diagnostics menu, navigate to
EP Setup
>
Installed Licenses
.
EVENT LOG
Display Log
This version of the Event log displays the panel text that appeared when the event occurred.
To view the Event log:
1
From the Diagnostics menu, navigate to:
Event Log
>
Display Log
2
Press or to view the entries.
Print Log
Additional diagnostic information is available when the event log is printed. The first page of the report shows the
general device information.
The specific events that appear in the report vary depending on the operational history of the printer. Logs may be
printed from the following events:
•
Job accounting log failures
•
NV reset failures
•
NV mirror entries
•
9xx and 1xx (print engine) service error entries
•
Programming error entries
•
Maintenance count reset entries
•
Clear log entries
•
Paper jam entries
•
Firmware update entries
•
JFFS2 partition format entries
•
USB setup pkt info entries
•
Supply event entries
To print the Event log:
From the Diagnostics menu, navigate to
Event Log
>
Print Log
.
Clear Log
Use this to remove all the current information in the Event log. This affects both the viewed log and the printed log
information.
4063
Service menus
241
Summary of Contents for MS71x
Page 24: ...4063 24 ...
Page 26: ...4063 26 ...
Page 222: ...4063 222 ...
Page 307: ...10 Remove the MPF pick roller 11 Remove the second flange 4063 Repair information 307 ...
Page 332: ...3 Open the fuser access door 4 Remove the two screws A 4063 Repair information 332 ...
Page 358: ...6 Remove the five screws A 7 Remove the PCBA housing 4063 Repair information 358 ...
Page 437: ...4 Remove the other four screws C from the front side of the frame 4063 Repair information 437 ...
Page 441: ...5 Release the latches A holding the sensor to the media feeder 4063 Repair information 441 ...
Page 451: ...2 Remove the two screws B then remove the right cover 4063 Repair information 451 ...
Page 453: ...2 Remove the two screws B then remove the left cover 4063 Repair information 453 ...
Page 459: ...4063 Repair information 459 ...
Page 464: ...2 Remove the two screws B then remove the right outer cover 4063 Repair information 464 ...
Page 466: ...2 Remove the two screws B then remove the left cover 4063 Repair information 466 ...
Page 468: ...3 Remove the three screws A then remove the controller PCBA 4063 Repair information 468 ...
Page 475: ...2 Remove the two screws C then remove the right cover 4063 Repair information 475 ...
Page 481: ...2 Remove the two screws C then remove the left cover 4063 Repair information 481 ...
Page 488: ...6 Ease the media stack flap off the stapler assembly 4063 Repair information 488 ...
Page 524: ...4063 524 ...
Page 539: ...4063 539 ...
Page 542: ...4063 Parts catalog 542 ...
Page 543: ...Assembly 1 Covers 4063 Parts catalog 543 ...
Page 545: ...Assembly 2 Paper path 4063 Parts catalog 545 ...
Page 547: ...Assembly 3 Fusers 4063 Parts catalog 547 ...
Page 549: ...Assembly 4 Electronics 19 20 20 21 22 4063 Parts catalog 549 ...
Page 552: ...4063 Parts catalog 552 ...
Page 553: ...Assembly 5 Drive motors 11 12 4063 Parts catalog 553 ...
Page 555: ...Assembly 6 Duplex 4063 Parts catalog 555 ...
Page 557: ...Assembly 7 Frame 16 16 17 4063 Parts catalog 557 ...
Page 559: ...Assembly 8 Control panel 9 10 17 6 7 7 8 5 11 12 13 14 14 15 15 16 4063 Parts catalog 559 ...
Page 562: ...4063 Parts catalog 562 ...
Page 565: ...Assembly 10 Input options 1 2 3 4063 Parts catalog 565 ...
Page 567: ...Assembly 11 250 sheet tray option 4063 Parts catalog 567 ...
Page 569: ...Assembly 12 550 sheet tray option 4063 Parts catalog 569 ...
Page 571: ...Assembly 13 High capacity input tray option 1 1 2 4063 Parts catalog 571 ...
Page 575: ...Assembly 15 Output options 2 1 3 4 4063 Parts catalog 575 ...
Page 577: ...Assembly 16 Output expander option 1 2 3 4 5 6 8 7 9 4063 Parts catalog 577 ...
Page 579: ...Assembly 17 High capacity output expander option 1 2 3 5 6 4 7 8 4063 Parts catalog 579 ...
Page 581: ...Assembly 18 Staple finisher option 1 5 1 2 3 4 6 4063 Parts catalog 581 ...
Page 583: ...Assembly 19 Staple finisher option 2 1 4 5 6 7 8 3 10 11 2 12 13 14 9 4063 Parts catalog 583 ...
Page 585: ...Assembly 20 Mailbox option 1 1 2 3 4 5 6 7 10 8 9 4063 Parts catalog 585 ...
Page 587: ...Assembly 21 Mailbox option 2 1 3 4 2 4063 Parts catalog 587 ...
Page 592: ...4063 Parts catalog 592 ...
Page 594: ...4063 594 ...
Page 598: ...4063 598 ...
Page 602: ...Models MS81x and MS71x paper path rollers and sensors 4063 Appendix C Theory of operation 602 ...
Page 638: ...4063 Index 638 ...