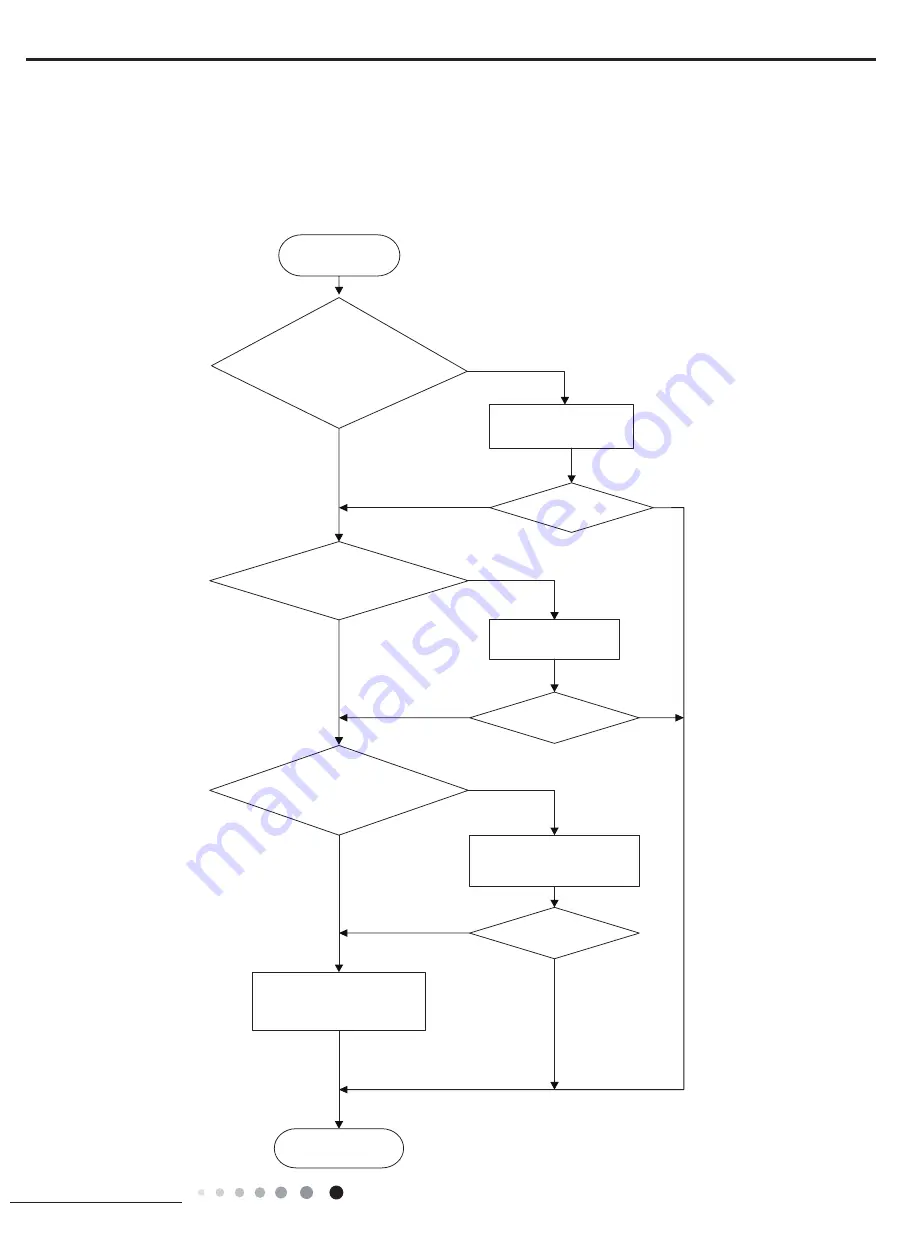
35
Installation and Maintenance
Service Manual
9.2 Procedure of Troubleshooting
1. Malfunction of Temperature Sensor F1, F2
Main detection points:
● Is the wiring terminal between the temperature sensor and the controller loosened or poorly contacted?
● Is there short circuit due to trip-over of the parts?
● Is the temperature sensor broken?
● Is mainboard broken?
Malfunction diagnosis process:
Is the wiring terminal between the
temperature sensor and the controller
loosened or poorly contacted?
Start
Insert the temperature
sensor tightly
Yes
Yes
Yes
Yes
Yes
Yes
No
No
No
No
No
No
Is malfunction
eliminated
Is malfunction
eliminated
Is malfunction
eliminated
Replace it with a
temperature sensor with
the same model
Make the parts upright
Is there short circuit due to trip-
over of the parts
Is the temperature sensor normal
according to the resistance table?
Replace the mainboard with
the same model.
End
Summary of Contents for Y6760
Page 20: ...17 Technical Information Service Manual AUTO COOL DRY FAN HEAT OFF...
Page 21: ...18 Technical Information Service Manual battery Cover of battery box remove reinstall...
Page 22: ...19 Technical Information Service Manual...
Page 51: ...48 Installation and Maintenance Service Manual LM024CI 100T432 1...
Page 70: ...67 Installation and Maintenance Service Manual...