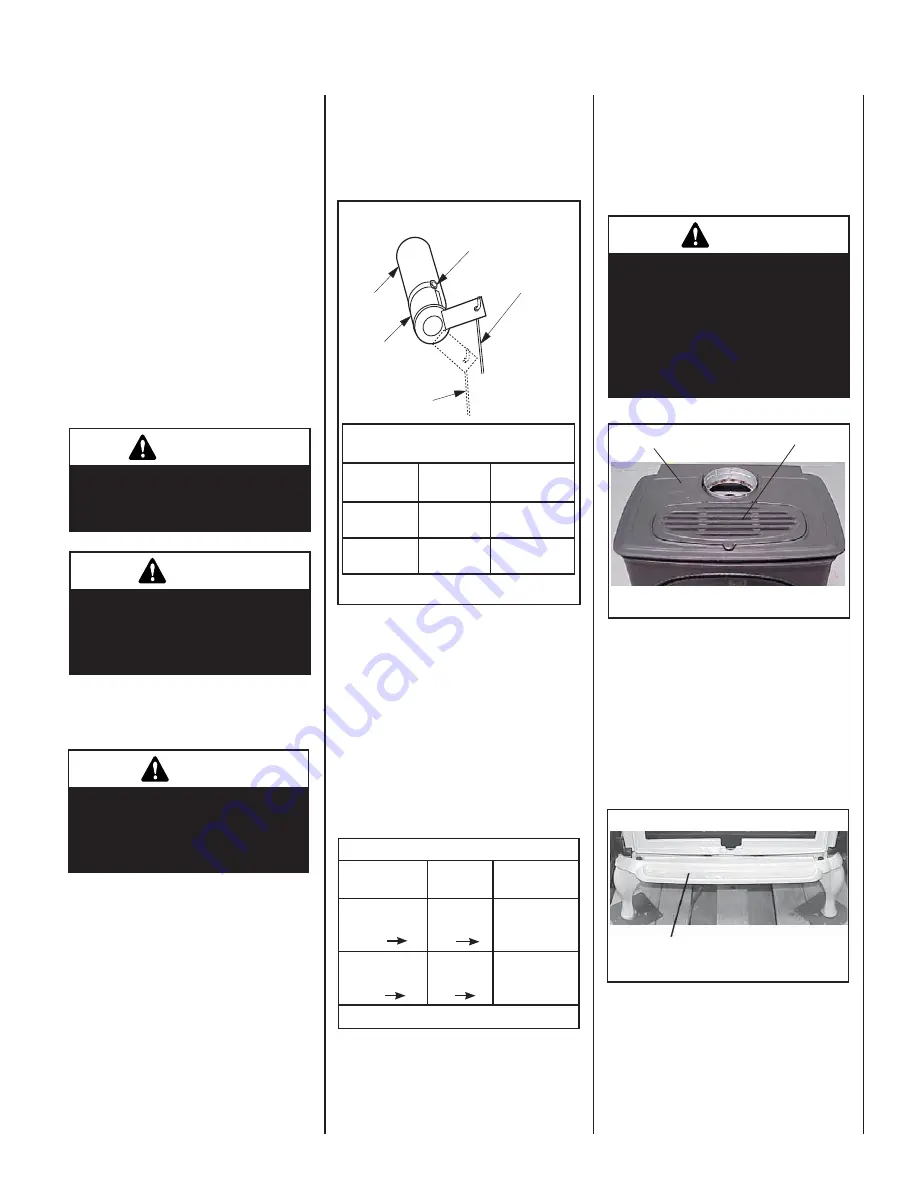
17
NOTE: DIAGRAMS & ILLUSTRATIONS ARE NOT TO SCALE.
Ref. Air shutter Patent:
U.S. Pat. 5,553,603
Figure 34
Adjustment Rod Up
(1/8" Open Position)
Air Shutter
Burner Tube
Adjusting Set Screw
Adjustment Rod Down
(full open position)
Burner Air Shutter Adjustment
Stove Cast Iron Top
Trivet
Ash Lip
CAUTION
The cast iron stove top is very
heavy and may require a mini-
mum of two people to lift; one
person on each side (the CI1500
series cast top weighs ~20
pounds and the CI2500 series
cast top weighs ~40 pounds).
IMPORTANT
Ensure that the front glass panel
is in place and sealed during
adjustment.
WARNING
Air shutter adjustment should
only be performed by a qualifi ed
professional service techni-
cian.
CAUTION
The adjustment rod and nearby
appliance surfaces are hot. Exer-
cise caution to avoid injury while
adjusting fl ame appearance.
Burner Adjustment
Air Shutter Adjustment Guidelines:
If the burner flame appearance differs
greatly from what is shown on this Page
(see
Figure 33
)
, some adjustment from
standard for the air shutter gap may be
necessary (to compensate for variables in
the installation and fuel such as, BTU value
/ composition, gas pressure, specifi c gravity
of gas, altitude, etc.).
The following chart is provided to aid you in
achieving the correct air shutter adjustment
for your installation.
Air Shutter Adjustment Guidelines:
Amount of
Primary Air
Flame
Color
Air Shutter
Adjustment
If air shutter is
closed too far
Flame will
be yellow
Air shutter
gap should be
increased
If air shutter is
open too far
Flame will
be blue
Air shutter
gap should be
decreased
Table 10
When satisfi ed that the appliance operates
properly, proceed to fi nish the installation.
Leave the control knob in the ON position and
the on/off switch in the OFF position.
Main Burner Factory Air Shutter
Opening Setting - Inches (millimeter)
Model
Natural
Gas
Propane
Gas
CI1500DVF
5/16"
(7.93 mm)
5/8"
(15.9 mm)
CI2500DVF
1/2"
(12.7 mm)
5/8"
(15.9 mm)
Initially, always position the air shutter to the
factory setting as shown in
Figure 34
(adjust-
ment rod is located in the lower control area).
This can be done by moving the adjustment
rod up or down accordingly. Allow the burner
to operate for at least 15 minutes. Observe
the fl ame continuously. If it appears weak
or sooty as previously described, adjust the
air shutter to a more open position until the
desired fl ame appearance is achieved.
The adjustment rod and associated adjustable
air shutter is patented technology. Flame adjust-
ments can be made quickly and accurately to
taste without the need of disassembling the
appliance and waiting for 30 minutes after
each adjustment.
Sooting is indicated by black puffs developing
at the tips of very long orange fl ames. Sooting
results in black deposits forming on the logs,
appliance inside surfaces and on exterior
surfaces adjacent to the vent termination.
Sooting is caused by incomplete combus-
tion in the fl ames and lack of combustion air
entering the air shutter opening. To achieve
a warm yellow to orange fl ame that does not
soot, the shutter opening must be adjusted
between these two extremes.
No smoke or soot should be present. Repo-
sition the logs if fl ames impinge on any of
them. If the logs are properly positioned
and sooting conditions exist, the air shutter
opening on the main burner tube should be
adjusted. Normally, the more offsets in the
vent system, the greater the need for the air
shutter to be opened further.
Step 16. INSTALL STOVE TOP, TRIVET
AND ASH LIP
A. Place the cast iron top into position on the
stove top (See
Figure 35
).
Place the trivet
into the recess on the cast iron top (See
Figure 35
).
Figure 35
Figure 36
B. Locate the
ash lip
from packaging (Step 2).
Remove the 2 bolts from the tapped holes in
the ash lip. Align the ash lip below the fi rebox
as shown in
Figure 36
(the tapped holes
in ash lip should align with corresponding
slots below fi rebox). Reinstall the 2 bolts
that were removed from the ash lip (fi nger
tight only. If a tool is used, be careful not to
overtighten).