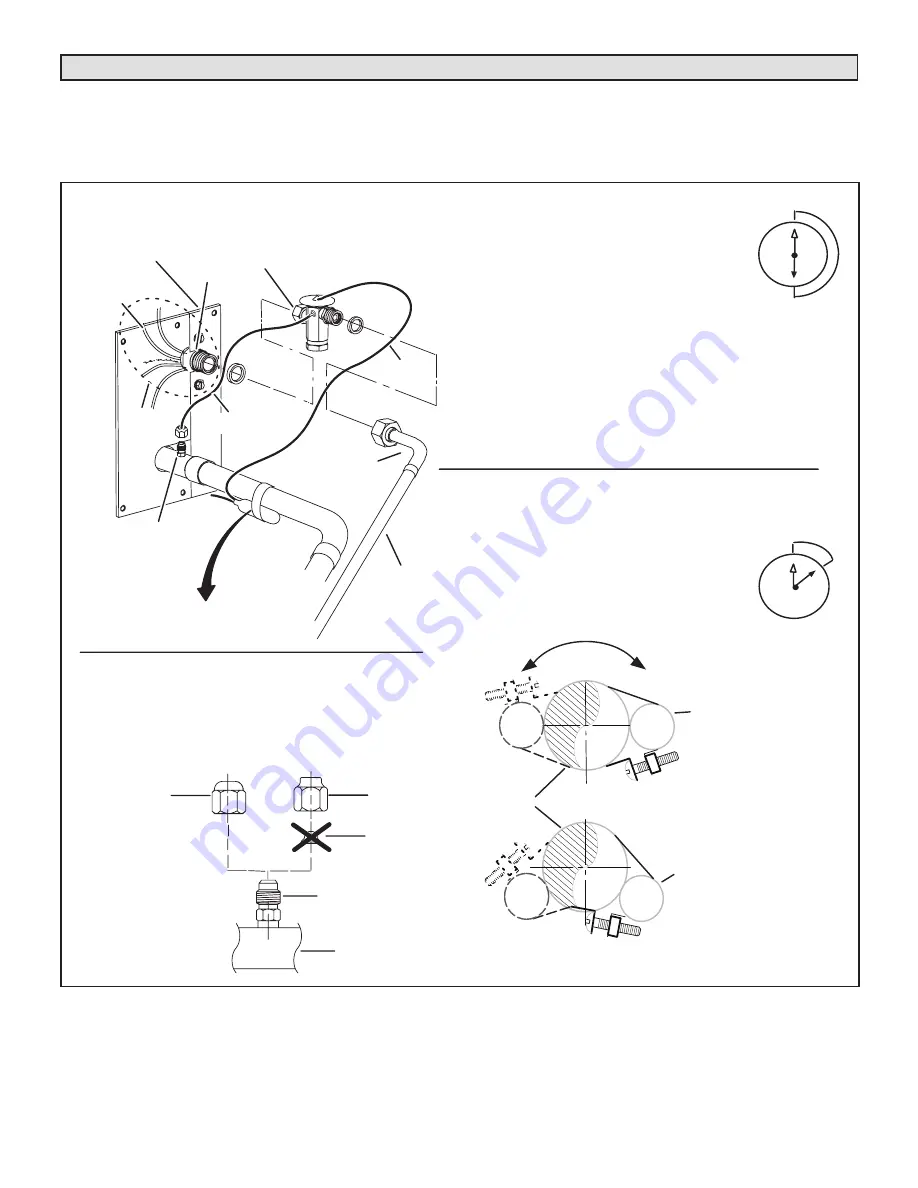
Page 17
A
Attach the vapor line sensing bulb in the proper
orientation as illustrated to the right using the clamp and
screws provided.
NOTE
— Confirm proper thermal contact between vapor line
and expansion bulb before insulating the sensing bulb once
installed.
B
Connect the equalizer line from the expansion valve to
the equalizer vapor port on the vapor line. Finger tighten
the flare nut plus 1/8 turn (7 ft-lbs) as illustrated below.
TWO PIECE
PATCH PLATE
(UNCASED
COIL ONLY)
VAPOR
LINE
LIQUID LINE
ORIFICE
HOUSING
DISTRIBUTOR
TUBES
LIQUID LINE
MALE EQUALIZER LINE
FITTING (SEE
EQUALIZER LINE
INSTALLATION FOR
FURTHER DETAILS)
SENSING
LINE
EQUALIZER
LINE
EXPANSION
VALVE
TEFLON
®
RING
(Uncased Coil Shown)
Sensing bulb insulation is required if
mounted external to the coil casing. See
sensing bulb installation for bulb positioning.
STUB
END
TEFLON
®
RING
LIQUID LINE
ASSEMBLY WITH
BRASS NUT
DISTRIBUTOR
ASSEMBLY
A
Remove the field-provided fitting that temporary
reconnected the liquid line to the indoor unit's distributor
assembly.
B
Install one of the provided Teflon
®
rings around the
stubbed end of the expansion valve and lightly lubricate
the connector threads and expose surface of the Teflon
®
ring with refrigerant oil.
C
Attach the stubbed end of the expansion valve to the
liquid line orifice housing. Finger tighten and use an
appropriately sized wrench to turn an additional 1/2 turn
clockwise as illustrated in the figure above, or 20 ft-lb.
D
Place the remaining Teflon
®
washer around the other
end of the expansion valve. Lightly lubricate connector
threads and expose surface of the Teflon
®
ring with
refrigerant oil.
E
Attach the liquid line assembly to the expansion valve.
Finger tighten and use an appropriately sized wrench to
turn an additional 1/2 turn clockwise as illustrated in the
figure above or 20 ft-lb.
ON 7/8” AND LARGER LINES,
MOUNT SENSING BULB AT
EITHER THE 4 OR 8 O'CLOCK
POSITION. NEVER MOUNT ON
BOTTOM OF LINE.
12
ON LINES SMALLER THAN
7/8”, MOUNT SENSING
BULB BETWEEN THE 3 AND
9 O'CLOCK POSITIONS.
12
BULB
VAPOR LINE
NOTE — NEVER MOUNT ON BOTTOM OF LINE.
BULB
BULB
BULB
VAPOR LINE
FLARE NUT
COPPER FLARE
SEAL BONNET
MALE BRASS EQUALIZER
LINE FITTING
FLARE SEAL CAP
OR
1
2
3
4
5
6
7
8
9
10
11 12
1/2 Turn
SENSING BULB INSTALLATION
EQUALIZER LINE INSTALLATION
1
2
3
4
5
6
7
8
9
10
11 12
1/8 Turn
A
Remove and discard either the flare seal cap or flare nut
with copper flare seal bonnet from the equalizer line port
on the vapor line as illustrated in the figure to the right.
B
Remove and discard either the flare seal cap or flare nut
with copper flare seal bonnet from the equalizer line port on
the vapor line as illustrated in the figure to the right.
INDOOR EXPANSION VALVE INSTALLATION
9 O'CLOCK TO
3 O'CLOCK
FIGURE 11
Installing Indoor Metering Device
This outdoor unit is designed for use in systems that use
an expansion valve (TXV) metering device at the indoor
coil. The expansion valve can be installed internal or ex-
ternal to the indoor coil. In applications where an uncased
coil is being installed in a field-provided plenum, install the
expansion valve in a manner that will provide access for
field servicing of the expansion valve. Refer to below illus
-
tration for reference during installation of expansion valve
unit.