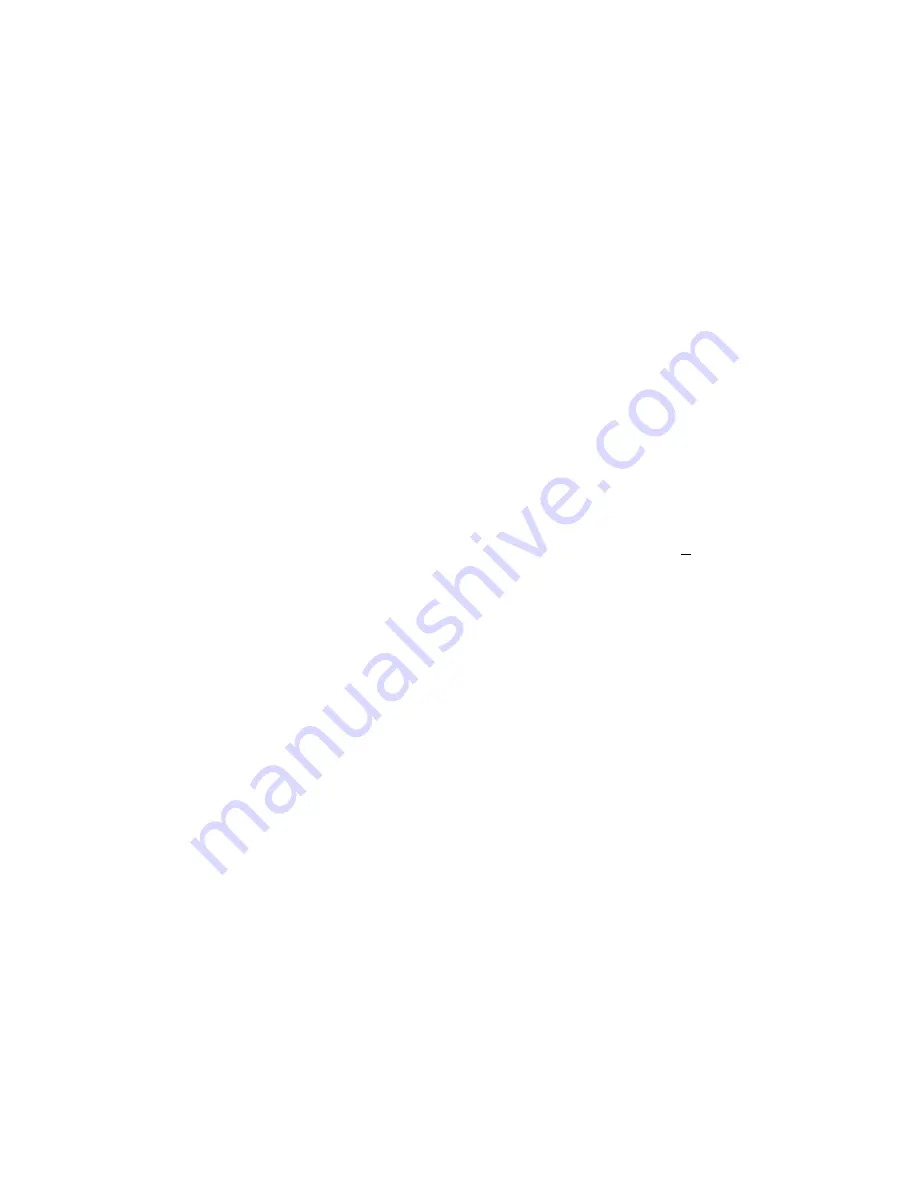
Page 15
The compressor is charged with sufficient polyol ester
oil for line set lengths up to 50 feet (15.2 m). If oil must
be added to the compressor in the field, Copeland has
approved Mobil EAL
t
Arctic 22CC and ICI EMKA-
RATE
t
RL32CF.
Units Delivered Void of Charge
If the system is void of refrigerant,
clean the system us-
ing the procedure described below.
1 − Use nitrogen to pressurize the system and check for
leaks. Repair leaks, if possible.
2 − Evacuate the system to remove as much of the mois-
ture as possible.
3 − Use nitrogen to break the vacuum and install the pro-
vided filter drier in the system.
4 − Evacuate the system again. Then, weigh the appropri-
ate amount of R410A refrigerant (listed on unit name-
plate) into the system.
5 − Monitor the system to determine the amount of mois-
ture remaining in the oil. Use test kit 10N46 to verify
that the moisture content is within the kit’s dry color
range. It may be necessary to replace the filter drier
several times to achieve the required dryness level.
If
system dryness is not verified, the compressor will
fail in the future.
Checking Charge
The outdoor unit should be charged during warm weather.
However, applications arise in which charging must occur
in the colder months.
The method of charging is deter-
mined by the unit’s
refrigerant metering device
and the
outdoor ambient temperature
.
Measure the liquid line temperature and the outdoor ambi-
ent temperature as outlined below:
1 − Connect the manifold gauge set to the service valves:
low pressure gauge to
vapor
valve service port
high pressure gauge to
liquid
valve service port
Close manifold gauge set valves. Connect the center
manifold hose to an upright cylinder of R410A .
2 − Set the room thermostat to call for heat. This will create
the necessary load for properly charging the system in
the cooling cycle.
3 − Use a digital thermometer to record the outdoor ambi-
ent temperature.
4 − When the heating demand has been satisfied, switch
the thermostat to cooling mode with a set point of 68
F
(20
C). When pressures have stabilized, use a digital
thermometer to record the liquid line temperature.
5 − The outdoor temperature will determine which charg-
ing method to use. Proceed with the appropriate charg-
ing procedure.
Weighing in the Charge Fixed Orifice
or
TXV Systems – Outdoor Temp. < 65
F (18
C)
If the system is void of refrigerant, or if the outdoor ambient
temperature is cool, the refrigerant charge should be
weighed into the unit. Do this after any leaks have been re-
paired.
1 − Recover the refrigerant from the unit.
2 − Conduct a leak check, then evacuate as previously
outlined.
3 − Weigh in the unit nameplate charge.
If weighing facilities are not available or if you are charging
the unit during warm weather, follow one of the other proce-
dures outlined below.
Charging Using the Subcooling
Method
Fixed Orifice Systems
Outdoor Temp. > 65
F (18
C))
If you charge a fixed orifice system when the outdoor ambi-
ent is 65
F (18
C) or above, use the subcooling method to
charge the unit.
1 − With the manifold gauge hose still on the liquid service
port and the unit operating stably, use a digital ther-
mometer to record the liquid line temperature.
2 − At the same time, record the liquid line pressure reading.
3 − Use a temperature/pressure chart for R410A to deter-
mine the saturation temperature for the liquid line pres-
sure reading. See table 5.
4 − Subtract the liquid line temperature from the saturation
temperature (according to the chart) to determine sub-
cooling.
(Saturation temperature − Liquid line tem-
perature = Subcooling)
5 − Compare the subcooling value with those in table 6. If
subcooling is greater than shown, recover some refrig-
erant. If subcooling is less than shown, add some re-
frigerant.