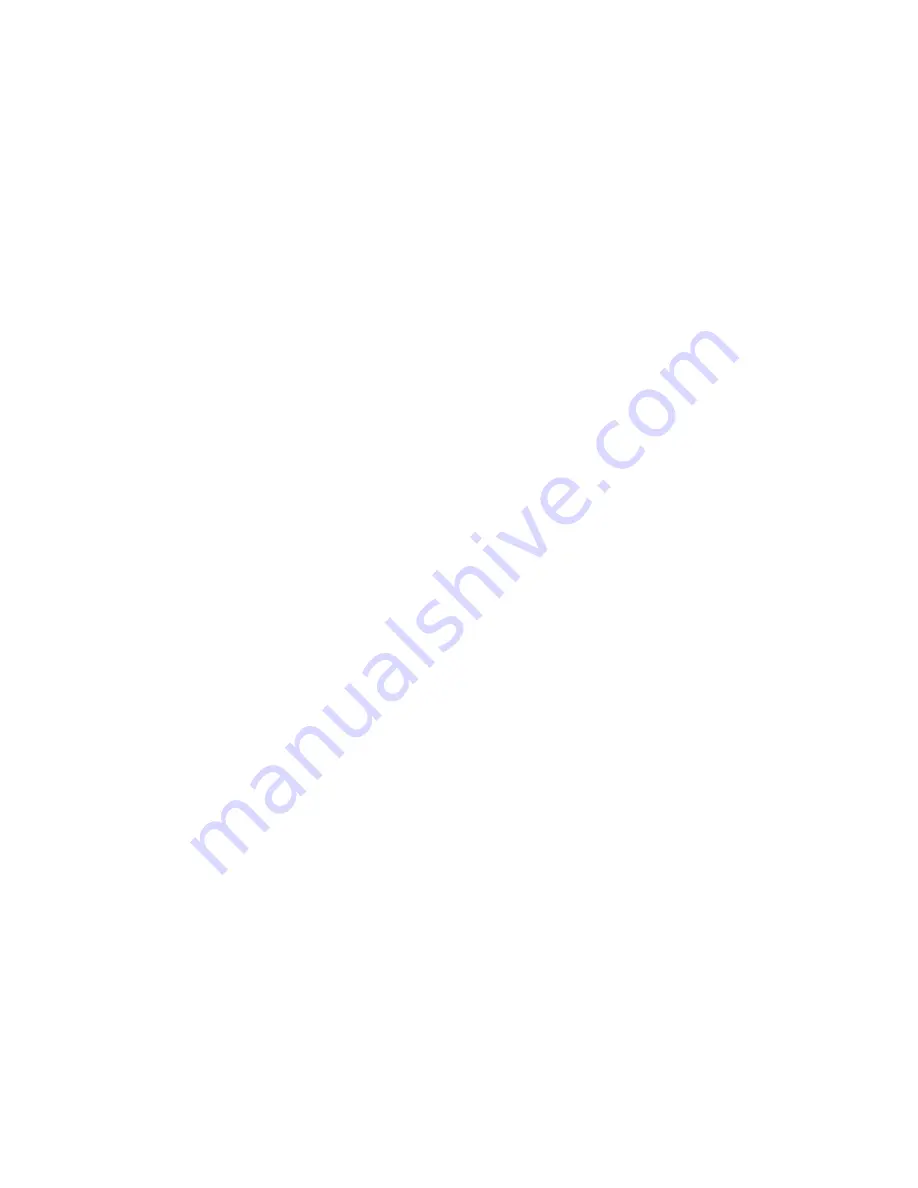
Page 11
Defrost Temperature Termination Shunt (Jumper)
Pins
The defrost board selections are: 50, 70, 90, and
100°F (10, 21, 32 and 38°C). The shunt termination pin is
factory set at 50°F (10°C). If the temperature shunt is not
installed, the default termination temperature is 90°F
(32°C).
Delay Mode
The defrost board has a field−selectable function to reduce
occasional sounds that may occur while the unit is cycling
in and out of the defrost mode. When a jumper is installed
on the DELAY pins, the compressor will be cycled off for 30
seconds going in and out of the defrost mode. Units are
shipped with jumper installed on DELAY pins.
NOTE − The 30 second off cycle is NOT functional when
jumpering the TEST pins.
Operational Description
The defrost control board has three basic operational
modes: normal, defrost, and calibration.
Normal Mode
The demand defrost board monitors
the O line, to determine the system operating mode
(heat/cool), outdoor ambient temperature, coil temper-
ature (outdoor coil) and compressor run time to deter-
mine when a defrost cycle is required.
Calibration Mode
The board is considered uncali-
brated when power is applied to the board, after cool
mode operation, or if the coil temperature exceeds the
termination temperature when it is in heat mode.
Calibration of the board occurs after a defrost cycle to
ensure that there is no ice on the coil. During calibra-
tion, the temperature of both the coil and the ambient
sensor are measured to establish the temperature dif-
ferential which is required to allow a defrost cycle.
Defrost Mode
The following paragraphs provide a
detailed description of the defrost system operation.
Detailed Defrost System Operation
The demand defrost control board initiates a defrost cycle
based on either frost detection or time.
Frost Detection
If the compressor runs longer than 34
minutes and the actual difference between the clear coil
and frosted coil temperatures exceeds the maximum differ-
ence allowed by the control, a defrost cycle will be initiated.
IMPORTANT − The demand defrost control board will allow
a greater accumulation of frost and will initiate fewer de-
frost cycles than a time/temperature defrost system.
Time
If 6 hours of heating mode compressor run time has
elapsed since the last defrost cycle while the coil tempera-
ture remains below 35°F (2°C), the demand defrost control
will initiate a defrost cycle.
Actuation
When the reversing valve is de−energized, the
Y1 circuit is energized, and the coil temperature is below
35°F (2°C), the board logs the compressor run time. If the
board is not calibrated, a defrost cycle will be initiated after
34 minutes of heating mode compressor run time. The con-
trol will attempt to self−calibrate after this (and all other) de-
frost cycle(s).
Calibration success depends on stable system tempera-
tures during the 20−minute calibration period. If the board
fails to calibrate, another defrost cycle will be initiated after
90 minutes of heating mode compressor run time. Once
the defrost board is calibrated, it initiates a demand defrost
cycle when the difference between the clear coil and
frosted coil temperatures exceeds the maximum difference
allowed by the control OR after 6 hours of heating mode
compressor run time has been logged since the last defrost
cycle.
Termination
The defrost cycle ends when the coil tem-
perature exceeds the termination temperature or after 14
minutes of defrost operation. If the defrost is terminated by
the 14−minute timer, another defrost cycle will be initiated
after 34 minutes of run time.
Test Mode
When Y1 is energized and 24V power is be-
ing applied to the board, a test cycle can be initiated by
placing the termination temperature jumper across the
Test" pins for 2 to 5 seconds. If the jumper remains across
the Test" pins longer than 5 seconds, the control will ignore
the test pins and revert to normal operation. The jumper will
initiate one cycle per test.
Enter the TEST" mode by placing a shunt (jumper) across
the TEST" pins on the board
after
power−up. (The TEST"
pins are ignored and the test function is locked out if the
shunt is applied on the TEST" pins before power−up).
Board timings are reduced, the low−pressure switch and
loss of charge detection fault is ignored and the board will
clear any active lockout condition.
Each test pin shorting will result in one test event.
For
each TEST" the shunt (jumper) must be removed for at
least 1 second and reapplied. Refer to flow chart (figure 16)
for TEST" operation.
Note: The Y1 input must be active (ON) and the O" room
thermostat terminal into board must be inactive.
Defrost Board Diagnostics
See table 5 to determine defrost board operational condi-
tions and to diagnose cause and solution to problems.