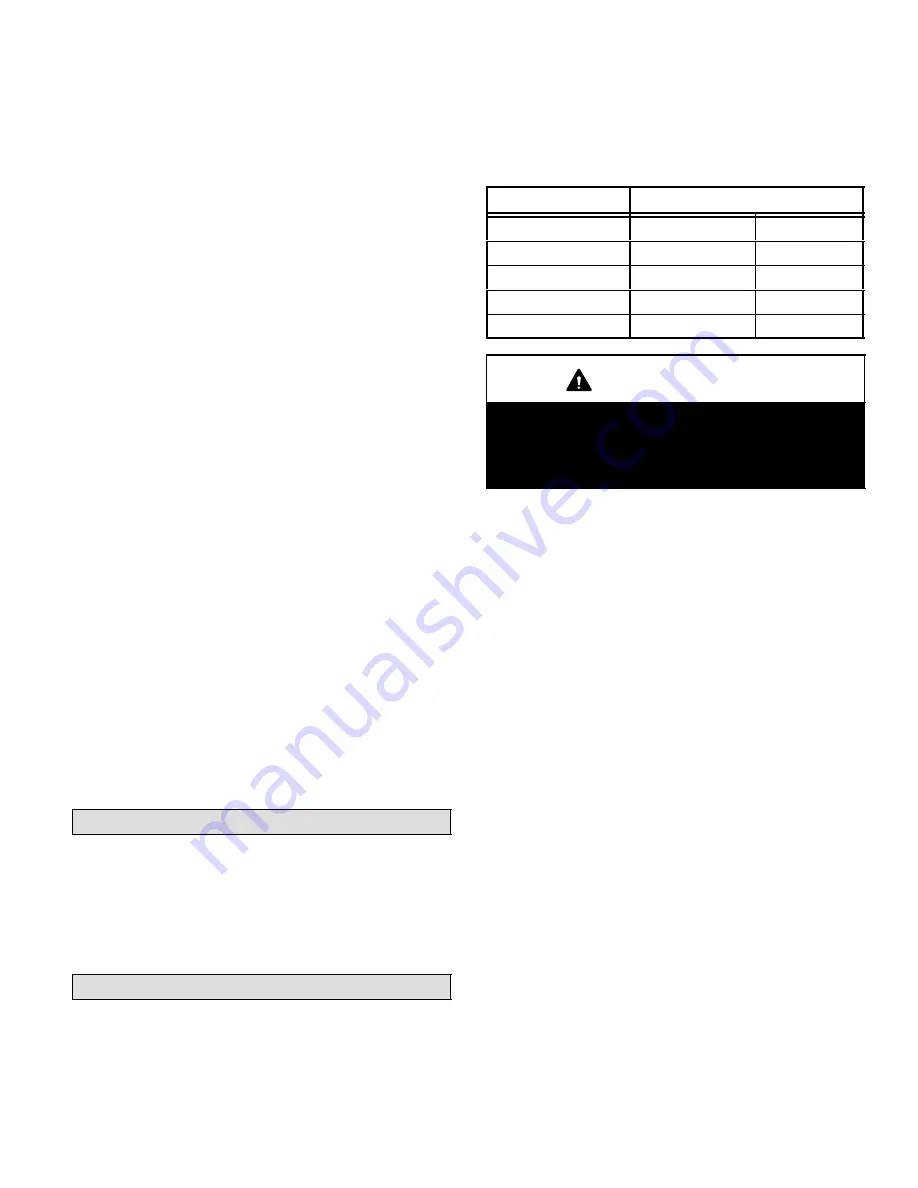
Page 12
4 − Remove the pressure tap valve cores from the
HPXA15 unit’s service valves. Connect an R22 cylin-
der with clean refrigerant to the vapor service valve.
Connect the R22 gauge set to the liquid line valve and
connect a recovery machine with an empty recovery
tank to the gauge set.
5 − Set the recovery machine for liquid recovery and start
the recovery machine. Open the gauge set valves to
allow the recovery machine to pull a vacuum on the ex-
isting system line set and indoor coil.
6 − Invert the cylinder of clean R22 and open its valve to
allow liquid refrigerant to flow into the system through
the vapor line valve. Allow the refrigerant to pass from
the cylinder and through the line set and the indoor coil
before it enters the recovery machine.
7 − After all of the liquid refrigerant has been recovered,
switch the recovery machine to vapor recovery so that
all of the R22 vapor is recovered.
NOTE − A single system flush should remove all of the
mineral oil from the existing refrigerant lines and in-
door coil. A second flushing may be done (using clean
refrigerant) if insufficient amounts of mineral oil were
removed during the first flush.
Each time the system
is flushed, you must allow the recovery machine
to pull a vacuum on the system at the end of the
procedure.
8 − Close the valve on the inverted R22 drum and the
gauge set valves. Pump the remaining refrigerant out
of the recovery machine and turn the machine off.
9 − Use nitrogen to break the vacuum on the refrigerant
lines and indoor coil before removing the recovery ma-
chine, gauges and R22 refrigerant drum. Reinstall
pressure tap valve cores into HPXA15 service valves.
10 −Install the provided check/expansion valve (approved
for use with R410A refrigerant) in the liquid line at the
indoor coil.
Manifold Gauge Set
Manifold gauge sets used with systems charged with
R410A refrigerant must be capable of handling the higher
system operating pressures. The gauges should be rated
for use with pressures of 0 − 800 on the high side and a low
side of 30" vacuum to 250 psi with dampened speed to 500
psi. Gauge hoses must be rated for use at up to 800 psi of
pressure with a 4000 psi burst rating.
Service Valves
Access the liquid line and vapor line service valves (figures
13 and 14) and gauge ports are used for leak testing, eva-
cuating, charging and checking charge. See table 1 for
torque requirements.
Each valve is equipped with a service port which has a fac-
tory−installed Schrader valve. A service port cap protects
the Schrader valve from contamination and serves as the
primary leak seal.
Table 1
Torque Requirements
Part
Recommended Torque
Service valve cap
8 ft.− lb.
11 NM
Sheet metal screws
16 in.− lb.
2 NM
Machine screws #10
28 in.− lb.
3 NM
Compressor bolts
90 in.− lb.
10 NM
Gauge port seal cap
8 ft.− lb.
11 NM
IMPORTANT
Service valves are closed to the outdoor unit and
open to line set connections. Do not open the valves
until refrigerant lines have been leak tested and
evacuated. All precautions should be exercised to
keep the system free from dirt, moisture and air.
To Access Schrader Port:
1 − Remove service port cap with an adjustable wrench.
2 − Connect gauge to the service port.
3 − When testing is complete, replace service port cap.
Tighten finger tight, then an additional 1/6 turn.
To Open Service Valve:
1 − Remove stem cap with an adjustable wrench.
2 − Using service wrench and hex head extension, back
the stem out counterclockwise as far as it will go.
NOTE − Use a 3/16" hex head extension for liquid line
sizes or a 5/16" extension for vapor line sizes.
3 − Replace stem cap and tighten it firmly. Tighten finger
tight, then tighten an additional 1/6 turn.
To Close Service Valve:
1 − Remove stem cap with an adjustable wrench.
2 − Using service wrench and hex head extension, turn
stem clockwise to seat valve. Tighten it firmly.
NOTE − Use a 3/16" hex head extension for liquid line
sizes or a 5/16" extension for vapor line sizes.
3 − Replace stem cap. Tighten finger tight, then tighten an
additional 1/6 turn.
Vapor Line (Ball Type) Valve
Vapor line service valves function the same way as the oth-
er valves, the difference is in the construction. These
valves are not rebuildable. If a valve has failed, you must
replace it. A ball valve valve is illustrated in figure 14.
The ball valve is equipped with a service port with a factory−
installed Schrader valve. A service port cap protects the
Schrader valve from contamination and assures a leak−
free seal.