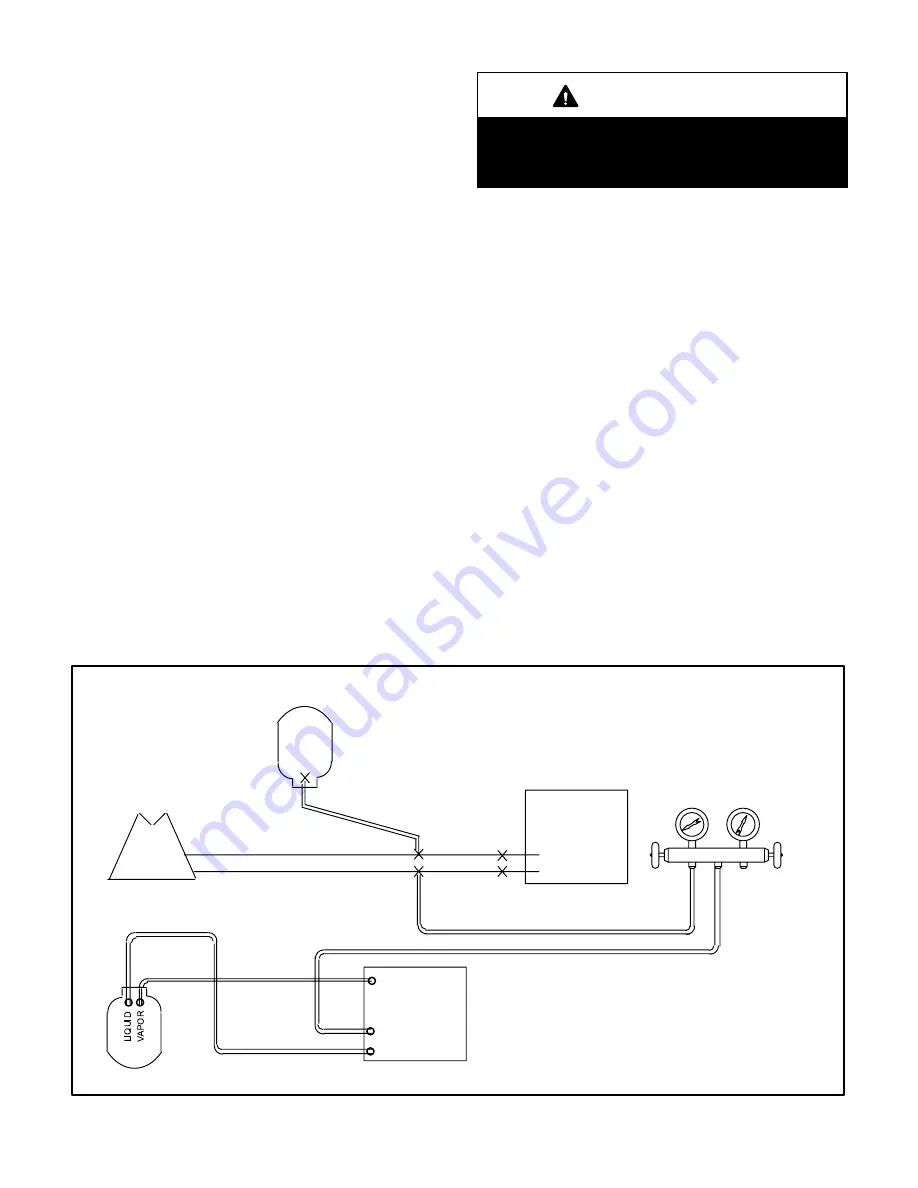
Page 6
the low pressure switches to ensure complete refrig-
erant evacuation.) When low side system pressures
reach 0 psig, close the suction line valve. Disconnect
all power to the existing outdoor unit. Refer to gauges
after shutdown to confirm that the valves are not al-
lowing refrigerant to flow back into the low side of the
system. Disconnect the liquid and vapor lines from
the existing outdoor unit.
2 − Remove the existing outdoor unit. Set the new
R407C unit and follow the brazing connection proce-
dure to make line set connections.
DO NOT install
provided R407C check/expansion valve at this
time.
Make low voltage and line voltage connections to the
new outdoor unit.
DO NOT turn on power to the
unit or open the outdoor unit service valves at
this time.
3 − Remove the existing refrigerant flow control orifice or
thermal expansion/check valve before continuing
with flushing procedures. The existing devices are
not approved for use with R407C refrigerant and may
prevent proper flushing. Use a field−provided fitting to
reconnect the lines.
4 − Remove the pressure tap valve cores from the HP32
unit’s service valves. Connect an R22 cylinder with
clean refrigerant to the suction service valve. Con-
nect the R22 gauge set to the liquid line valve and
connect a recovery machine with an empty recovery
tank to the gauge set.
IMPORTANT
The line set and indoor coil must be flushed with
at least the same amount of clean refrigerant that
previously charged the system. Check the charge
in the flushing cylinder before proceeding.
5 − Set the recovery machine for liquid recovery and
start the recovery machine. Open the gauge set
valves to allow the recovery machine to pull a vacu-
um on the existing system line set and indoor coil.
6 − Invert the cylinder of clean R22 and open its valve to
allow liquid refrigerant to flow into the system through
the suction line valve. Allow the refrigerant to pass
from the cylinder, through the line set and the indoor
coil before entering the recovery machine.
7 − After all of the liquid refrigerant has been recovered,
switch the recovery machine to vapor recovery so
that all of the R22 vapor is recovered. All the recovery
machine to pull a vacuum on the system.
NOTE − A single system flush should remove all of
the mineral oil from the existing refrigerant lines and
indoor coil. A second flushing may be done (using
clean refrigerant) if insufficient amounts of mineral oil
were removed during the first flush.
Each time the
system is flushed, you must allow the recovery
machine to pull a vacuum on the system at the
end of the procedure.
FLUSHING CONNECTIONS
LOW
PRESSURE
HIGH
PRESSURE
SUCTION LINE
SERVICE VALVE
INDOOR COIL
HP40 UNIT
GAUGE MANIFOLD
RECOVERY MACHINE
INVERTED R22
CYLINDER
LIQUID LINE
SERVICE VALVE
INLET
DISCHARGE
TANK RETURN
CLOSED
OPENED
EXISTING
EXISTING SUCTION LINE
EXISTING LIQUID LINE
RECOVERY
CYLINDER
FIGURE 5
Summary of Contents for HP40
Page 15: ...Page 15...