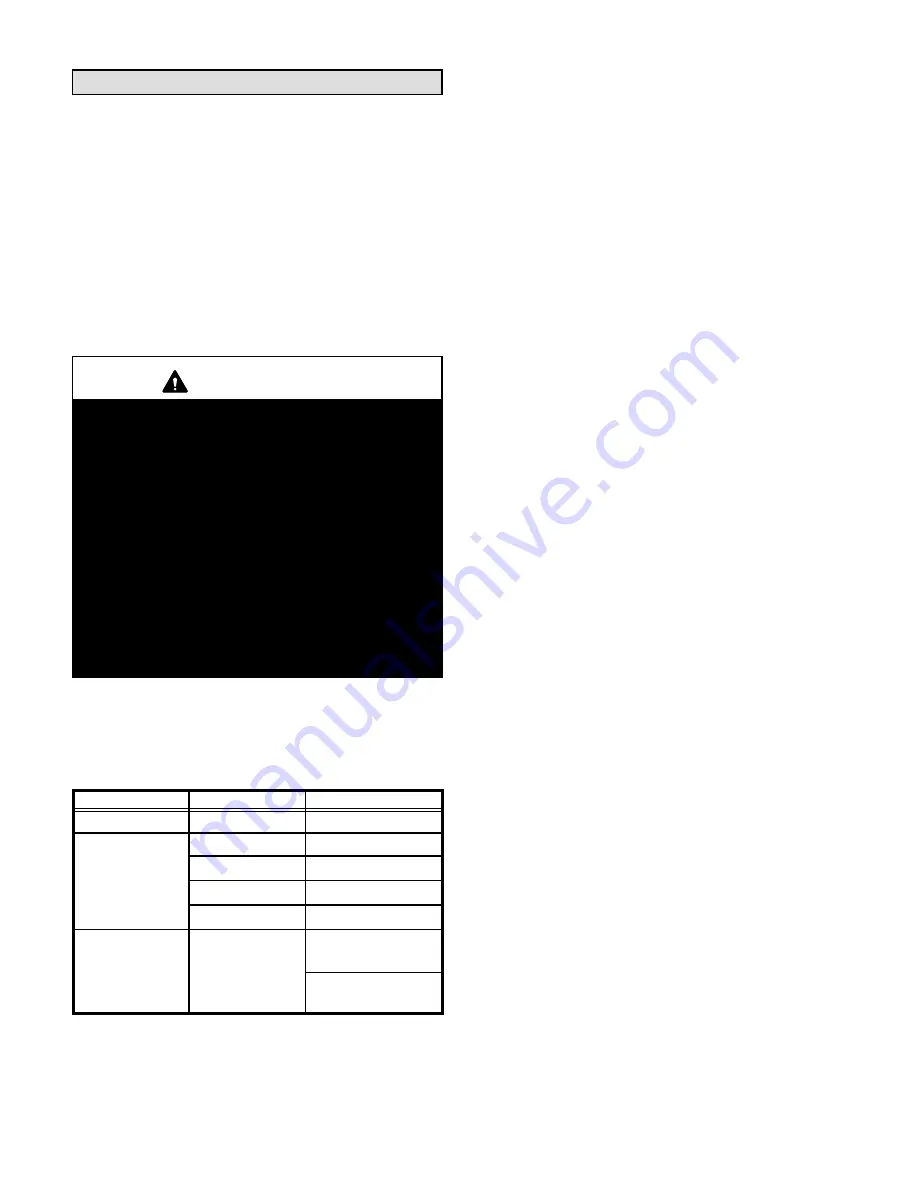
Page 4
Requirements
All G23(X) units are Canadian Standards Association
(CSA) certified.
In the USA, installation of Lennox gas central furnaces
must conform with local building codes. In the absence of
local codes, units must be installed according to the cur
rent National Fuel Gas Code (ANSIZ223.1) in the United
States. The National Fuel Gas Code is available from the
following address:
American National Standards Institute, Inc.
11 West 42nd Street
New York, NY 10036
Air supply for combustion and ventilation must conform to
the methods outlined in the current National Fuel Gas Code.
WARNING
Product contains fiberglass wool.
Disturbing the insulation in this product during
installation, maintenance, or repair will expose you
to fiberglass wool dust. Breathing this may cause
lung cancer. (Fiberglass wool is known to the State
of California to cause cancer.)
Fiberglass wool may also cause respiratory, skin,
and eye irritation.
To reduce exposure to this substance or for further
information, consult material safety data sheets
available from address shown below, or contact
your supervisor.
Lennox Industries Inc.
P.O. Box 799900
Dallas, TX 75379-9900
This furnace is CSA certified for installation clearances to
combustible material as listed on the unit rating plate and
in table 1. Accessibility and service clearances must take
precedence over fire protection clearances.
TABLE 1
Clearances
Location
Inches (mm)
Service access
Front
24 (610)
Side and rear
0 (0)
To combustible
Top
1 (25)
To combustible
materials
Flue
6 (152)*
Floor
0 (0)**
Around com
bustion cham
Front
B1Vent
3 (76)
bustion cham
ber air opening
Front
Single Wall Vent
4 (102)
NOTE-Service access clearance must be maintained.
* 1 inch (25mm) for type B1" Vent Pipe.
**For installation on combustible floors, appliance shall not be installed
directly on carpeting, tile, or other combustible material other than wood
flooring.
Vent installations must be in accordance with the pro
vided venting tables and applicable provisions of local
building codes.
For installation in a residential garage, the furnace must
be installed so that the burner(s) and the ignition source
are located no less than 18 inches (457 mm) above the
floor. The furnace must be located or protected to avoid
physical damage by vehicles. When a furnace is installed
in a public garage, hangar, or other building that has a
hazardous atmosphere, the furnace must be installed ac
cording to recommended good practice requirements
and current National Fuel Gas Code.
Unit must be adjusted to obtain a temperature rise within
the range specified on appliance rating plate.
G23(X) units must be installed so that electrical compo
nents are protected from water.
When the furnace is used with cooling units, it shall be
installed in parallel with, or on the upstream side of, cool
ing units to avoid condensation in the heating compart
ment. With a parallel flow arrangement, a damper (or
other means to control the flow of air) must adequately
prevent chilled air from entering the furnace. If the damp
er is manually operated, it must be equipped to prevent
operation of either the heating or the cooling unit, unless
it is in the full HEAT" or COOL" setting.
When installed, the furnace must be electrically
grounded according to local codes. In addition, in the
United States, installation must conform with the current
National Electric Code, ANSI/NFPA No. 70. The Nation
al Electric Code (ANSI/NFPA No. 70) is available from
the following address:
National Fire Protection Association
1 Battery March Park
Quincy, MA 02269
Field wiring connection with unit must meet or exceed
specifications of type T wire and withstand a 63
F (17
C)
temperature rise.
This furnace is designed for a minimum continuous return
air temperature of 60° dry bulb for cases in which a ther
mostat night setback is used. Return air temperature
must not exceed a maximum of 85
F db.
NOTE - G23(X) series units must not be used as a
construction heater during any phase of construction.
Very low return air temperatures, harmful vapors and
misplacement of the filters will damage the unit and low
er its efficiency.