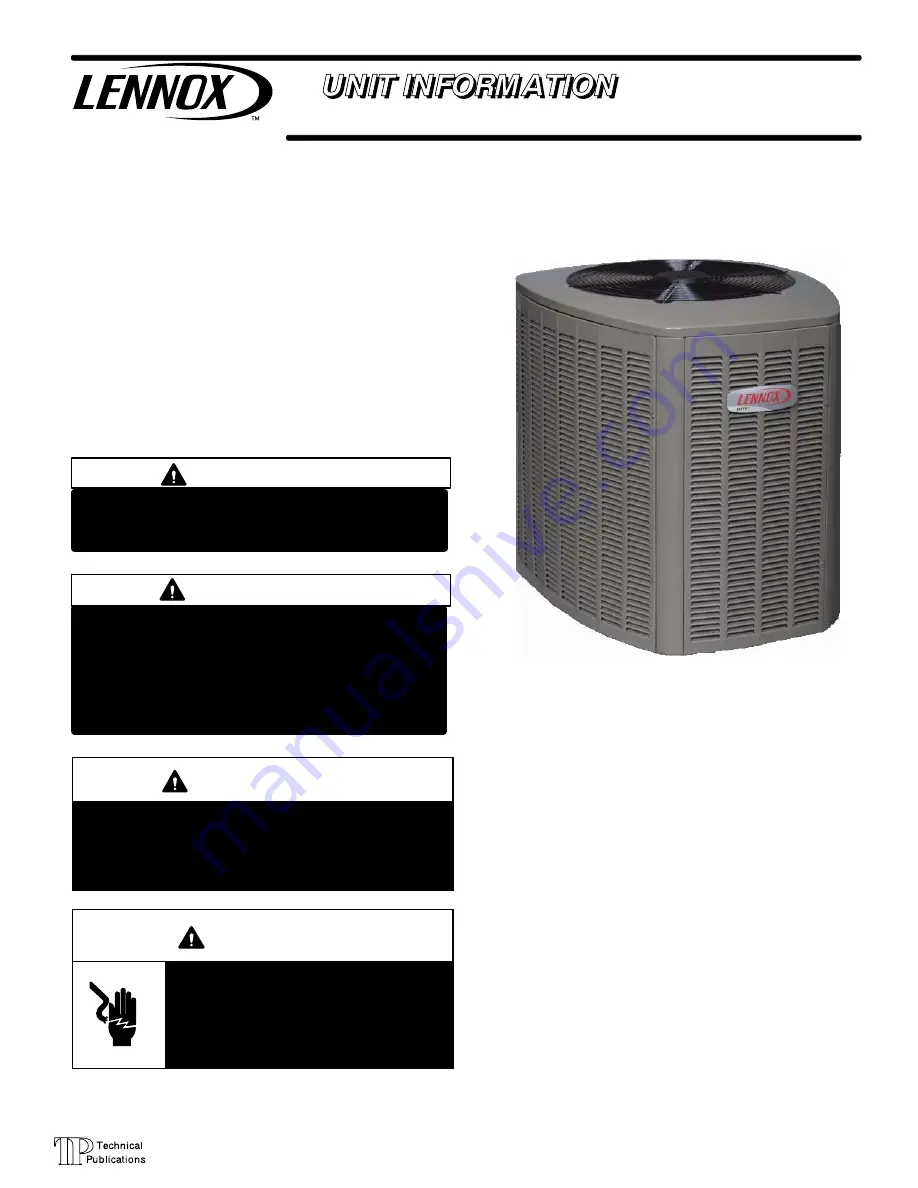
Page 1
©
2007 Lennox Industries Inc.
Corp. 0721−L7
XP14
Service Literature
Revised 06−2008
XP14 SERIES UNITS
The XP14 is a high efficiency residential split−system heat
pump unit, which features a scroll compressor and
HFC−410A refrigerant. XP14 units are available in sizes
ranging from 1 1/2 through 5 tons. The series is designed
for use with an indoor unit with an expansion valve ap-
proved for HFC−410A. This manual is divided into sections
which discuss the major components, refrigerant system,
charging procedure, maintenance and operation se-
quence.
Information contained in this manual is intended for use by
qualified service technicians only. All specifications are
subject to change.
IMPORTANT
Operating pressures of this HFC−410A unit are
higher than pressures in HCFC−22 units. Always
use service equipment rated for HFC−410A.
WARNING
Warranty will be voided if covered equipment is re-
moved from original installation site. Warranty will
not cover damage or defect resulting from:
Flood, wind, lightning, or installation and opera-
tion in a corrosive atmosphere (chlorine, fluorine,
salt, recycled waste water, urine, fertilizers, or oth-
er damaging chemicals).
WARNING
Improper installation, adjustment, alteration, service
or maintenance can cause property damage, person-
al injury or loss of life. Installation and service must
be performed by a qualified installer or service
agency.
WARNING
Electric shock hazard. Can cause injury
or death. Before attempting to perform
any service or maintenance, turn the
electrical power to unit OFF at discon-
nect switch(es). Unit may have multiple
power supplies.
TABLE OF CONTENTS
Specifications / Electrical
Page 2
. . . . . . . . . . . . .
I Unit Information
Page 3
. . . . . . . . . . . . . . . . . . . .
II Unit Components
Page 3
. . . . . . . . . . . . . . . . . .
III Refrigerant System
Page 13
. . . . . . . . . . . . . . . .
IV Charging
Page 15
. . . . . . . . . . . . . . . . . . . . . . . . .
V Service and Recovery
Page 20
. . . . . . . . . . . . . .
VI Maintenance
Page 21
. . . . . . . . . . . . . . . . . . . . . .
VII Wiring Diagram
Page 22
. . . . . . . . . . . . . . . . . . .