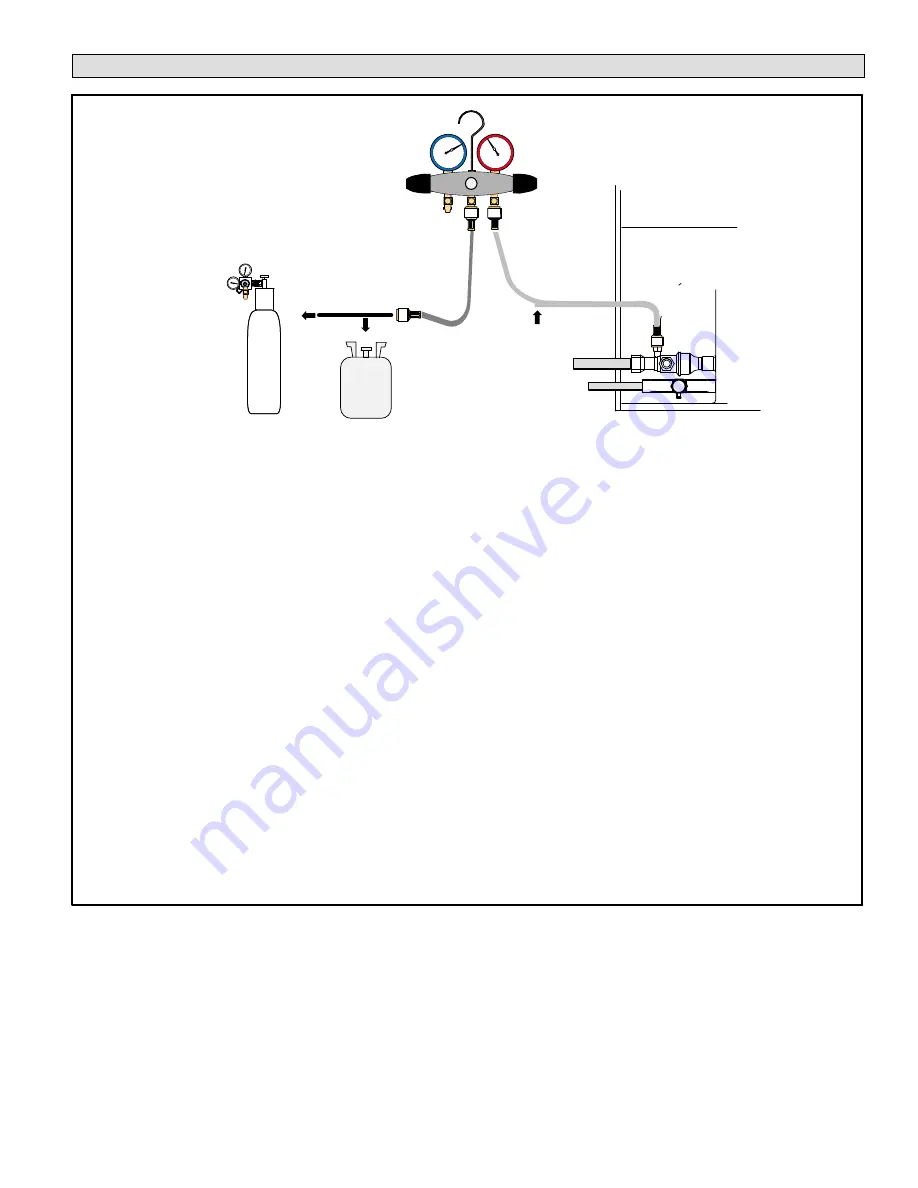
Page 9
XP13 SERIES
STEP 4 −− LEAK TEST AND EVACUATION
TO VAPOR
SERVICE VALVE
HFC−410A
MANIFOLD GAUGE SET
OUTDOOR UNIT
HIGH
LOW
CONNECT GAUGE SET
A
Connect the high pressure hose of an HFC−410A manifold gauge set to the vapor valve service port.
NOTE
Normally, the high pressure hose is connected to the liquid line port. However, connecting it
to the vapor port better protects the manifold gauge set from high pressure damage.
B
With both manifold valves closed, connect the cylinder of HFC−410A refrigerant to the center port of
the manifold gauge set.
NOTE
Later in the procedure, the HFC−410A container will be replaced by the nitrogen container.
TEST FOR LEAKS
After the line set has been connected to the indoor and outdoor units, check the line set connections
and indoor unit for leaks. Use the following procedure to test for leaks:
A
With both manifold valves closed, connect the cylinder of HFC−410A refrigerant to the center port of
the manifold gauge set. Open the valve on the HFC−410A cylinder (vapor only).
B
Open the high pressure side of the manifold to allow HFC−410A into the line set and indoor unit.
Weigh in a trace amount of HFC−410A.
[A trace amount is a maximum of two ounces (57 g) refriger-
ant or three pounds (31 kPa) pressure.]
Close the valve on the HFC−410A cylinder and the valve on
the high pressure side of the manifold gauge set. Disconnect the HFC−410A cylinder.
C
Connect a cylinder of nitrogen with a pressure regulating valve to the center port of the manifold
gauge set.
D
Adjust nitrogen pressure to 150 psig (1034 kPa). Open the valve on the high side of the manifold gauge
set in order to pressurize the line set and the indoor unit.
E
After a few minutes, open one of the service valve ports and verify that the refrigerant added to the
system earlier is measurable with a leak detector.
F
After leak testing, disconnect gauges from service ports.
1
2
A
B
NITROGEN
NOTE − Position
canister to deliver
liquid refrigerant.
FIGURE 9