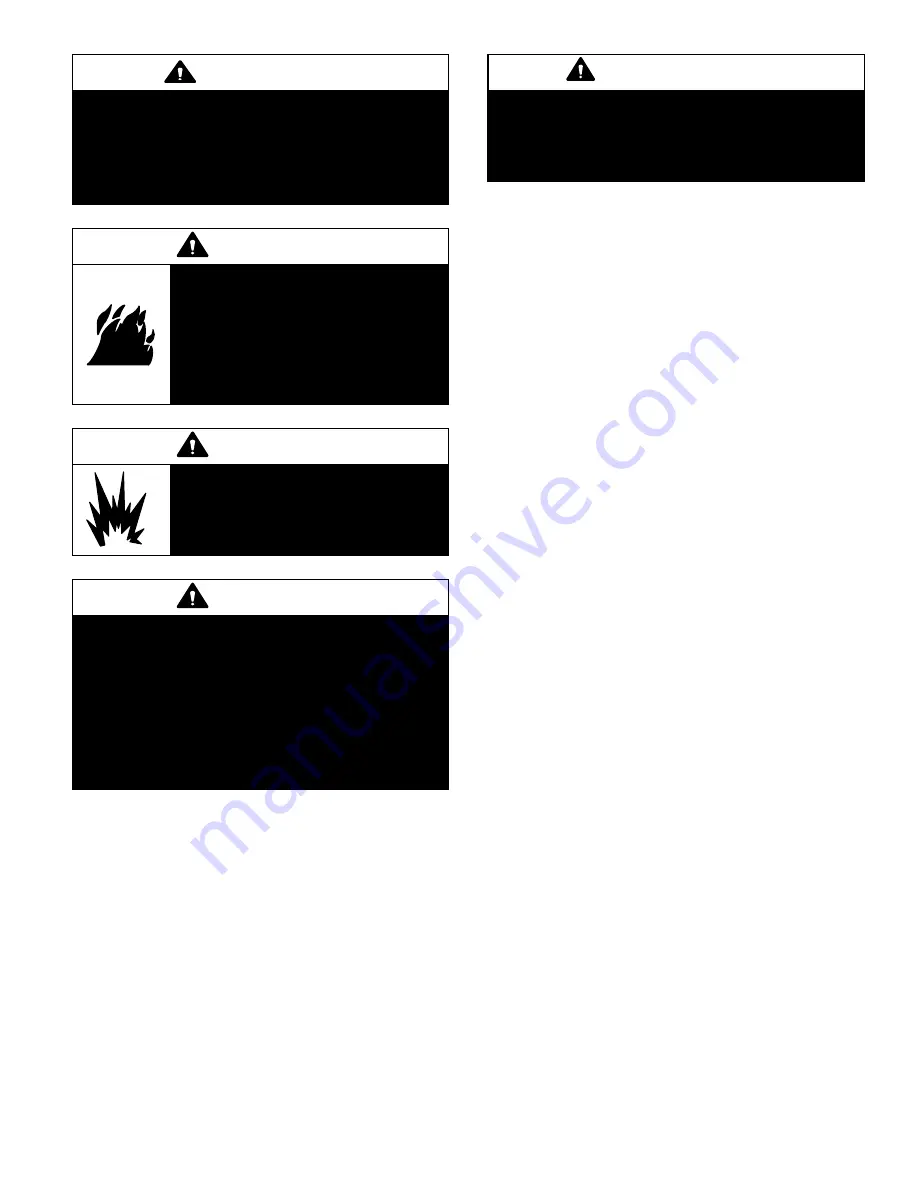
Page 11
MERIT
®
CBX25UHV SERIES
WARNING
Polyol ester (POE) oils used with HFC-410A
refrigerant absorb moisture very quickly. It is very
important that the refrigerant system be kept closed as
much as possible. DO NOT remove line set caps or
service valve stub caps until you are ready to make
connections.
WARNING
Danger of fire. Bleeding the refrigerant
charge from only the high side may result
in the low side shell and suction tubing
being pressurized. Application of a
brazing torch while pressurized may
result in ignition of the refrigerant and oil
mixture - check the high and low
pressures before unbrazing.
WARNING
When using a high pressure gas such as
dry nitrogen to pressurize a refrigeration
or air conditioning system, use a
regulator that can control the pressure
down to 1 or 2 psig (6.9 to 13.8 kPa).
CAUTION
Brazing alloys and flux contain materials which are
hazardous to your health.
Avoid breathing vapors or fumes from brazing
operations. Perform operations only in well ventilated
areas.
Wear gloves and protective goggles or face shield to
protect against burns.
Wash hands with soap and water after handling brazing
alloys and flux.
IMPORTANT
To prevent the build-up of high levels of nitrogen when
purging, be sure it is done in a well ventilated area. Purge
low pressure nitrogen (1 to 2 psig) through the refrigerant
piping during brazing. This will help to prevent oxidation
and the introduction of moisture into a system.
NOTE
- When installing refrigerant lines longer than 50
feet, see the Lennox Refrigerant Piping Design and
Fabrication Guidelines, CORP. 9351-L9, or contact
Lennox Technical Support Product Applications for
assistance. To obtain the correct information from Lennox,
be sure to communicate the following information: Model
and capacity.
1 -
Route the suction and liquid lines from the fittings on the
indoor coil to the fittings on the outdoor unit. Run the lines in
a direct path, avoiding unnecessary turns and bends.
2 -
Make sure that the suction line is insulated over the entire
exposed length and that neither suction nor liquid lines are
in direct contact with floors, walls, duct system, floor joists, or
other piping.
3 -
To avoid damaging the rubber grommets in the cabinet while
brazing, slide the rubber grommets over the refrigerant lines
until they are away from the heat source.
NOTE
-
Place wet rags against piping plate and around
suction line connections.
4 -
Connect the suction and liquid lines to the evaporator coil.
Take care to protect the cabinet and internal components as
detailed in figure 18.
5 -
Braze using an alloy of silver or copper and phosphorus with
a melting point above 1,100°F (593°C).
NOTE
- Do not use soft solder.
6 -
Allow refrigerant pipes to cool to room temperature.
7 -
Reinstall the rubber grommets into the refrigerant piping
panel.
NOTE
- Make sure expansion valve capillary tube is not
touching metal edges or copper tubing.
8 -
Make sure outdoor unit has been placed according to the
Installation Instructions and is connected to the refrigerant
lines.