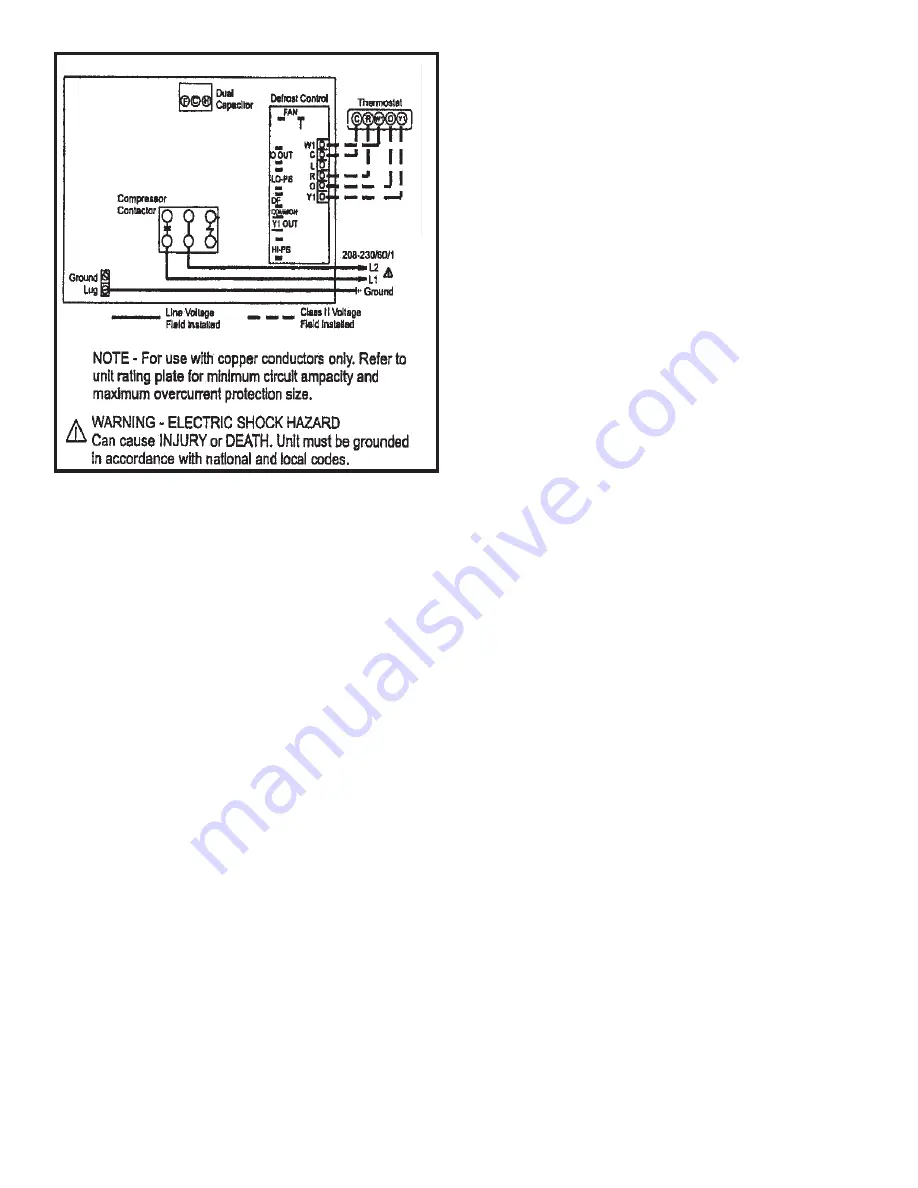
506470-01
Issue 1007
1. Install line voltage power supply to unit from a properly
sized disconnect switch. Any excess high voltage field
wiring should be trimmed or secured away from the low
voltage field wiring.
2. Ground unit at unit disconnect switch or to an earth
ground. To facilitate conduit, a hole is in the bottom of
the control box. Connect conduit to the control box
using a proper conduit fitting. Units are approved for
use only with copper conductors. 24V Class II circuit
connections are made in the low voltage junction box.
Refer to Figure 4 for high voltage field wiring diagram.
A complete unit wiring diagram is located inside the unit
control box cover.
3. Install room thermostat on an inside wall that is not
subject to drafts, direct sunshine, or other heat sources.
4. Install low voltage wiring from outdoor to indoor unit
and from thermostat to indoor unit. (See Wire Diagram
on page 27.)
5. Do not bundle any excess 24V control wire inside
control box. Run control wire through installed wire tie
and tighten wire tie to provide low voltage strain relief
and to maintain seperation of field-installed low and high
voltage circuits.
Refrigerant Piping
If the 4HP18LT unit is being installed with a new indoor coil
and line set, the refrigerant connections should be made as
outlined in this section. If an existing line set and/or indoor
coil will be used to complete the system, refer to this section
as well as the section that follows entitled -
Flushing
Existing Line Set and Indoor Coil
.
If this unit is being matched with an approved line set or
indoor coil which was previously charged with R-22
refrigerant, the line set and coil must be flushed prior to
installation. If the unit is being used with and existing indoor
coil which was equipped with a liquid line which served as a
metering device (RFCI), the liquid line must be replaced prior
to the installation of the 4HP18LT unit.
Field refrigerant piping consists of liquid and suction lines
from the outdoor unit (sweat connections) to the indoor coil
(flare or sweat connections).
Select line set diameters from Table 2 to ensure that oil
returns to the compressor. Size vertical suction riser to
maintain minimum velocity at minimum capacity.
Recommended line length is 50’ or less. If more than 50’
line set is required, contact Technical Services. Table 2
shows the diameters for line sets up to 100’ although vertical
lift applications and trapping requirements need to be
reviewed with Technical Services for line sets over 50’.
Installing Refrigerant Line
During the installation of an air conditioning system, it is
important to properly isolate the refrigerant line to prevent
unnecessary vibration. Line set contact with the structure
(wall, ceiling, or floor) may cause objectionable noise when
vibration is translated into sound. As a result, more energy
or vibration can be expected. Close attention to line set
isolation must be observed.
Following are some points to consider when placing and
installing a high-efficiency outdoor unit:
Page 4
Figure 4