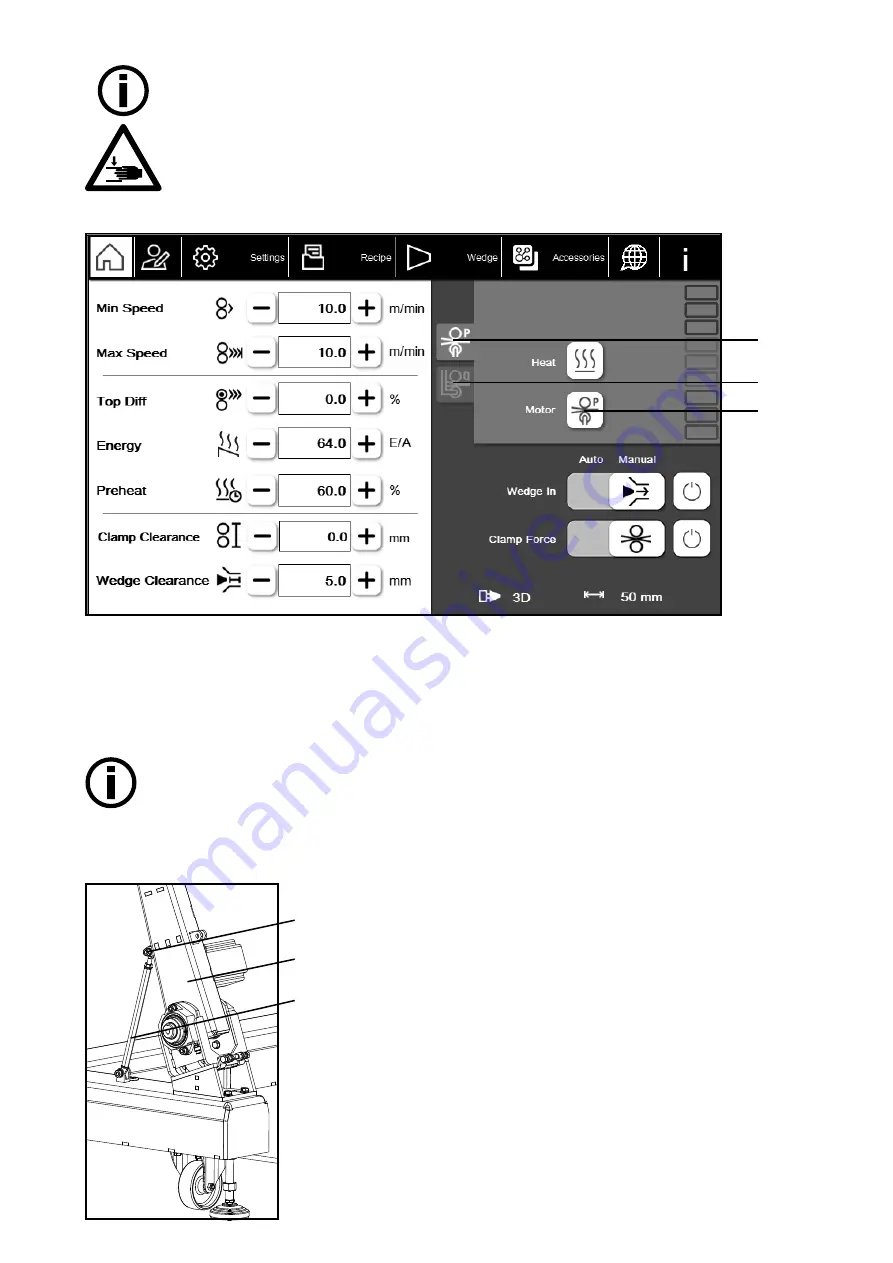
17
7.9 Changing Welding Arm and Welding Arm Options
Caution:
To activate the desired welding arm, the
motor icon (M)
must be switched off.
Make sure that the correct welding arm is selected to prevent damage to the drive and hazardous situa-
tions.
Caution:
Always hold the
pedestal (6)
when you detach the
retaining screw (6A)
. Then carefully lay the pedestal
down. If the pedestal falls downward unchecked, it may sustain irreparable damage.
When folding down the pedestal, be mindful of a possible crushing risk and keep body parts away from the area be-
tween the contact surface and pedestal.
Risk of crushing:
There is a risk of crushing due to the movement of mechanical parts. When changing
the welding arms, make sure that no body parts become trapped. Set the "Wedge In" and "Clamp Force"
sliders to "Manual" to prevent the machine from starting inadvertently.
To change between the individual welding arms, please set all settings to "Manual" and "Off" in advance. The
trans-
port rollers (4)
are now open and the
welding wedge (22)
is in the starting position.
Switch off the motor and select the welding arm you want to activate.
Pedestal (P)
see
Chapter 7.9.2
/
Quickarm (Q)
see
Chapter 7.9.3
Loosen the
screw (6A)
that holds the
threaded rod (6B)
and the
pedestal
(6)
together. Then pull the screw out while firmly holding the pedestal. Care-
fully lay the pedestal down.
Refit the screw and the corresponding washers so they do not get lost.
Now switch to the quickarm.
To bring the pedestal into the welding position, lift the
pedestal (6)
upward
and insert the screw.
7.9.1 Changing Welding Arm
7.9.2 Pedestal
Activating / Deactivating the Pedestal
6A
6
6B
P
Q
M