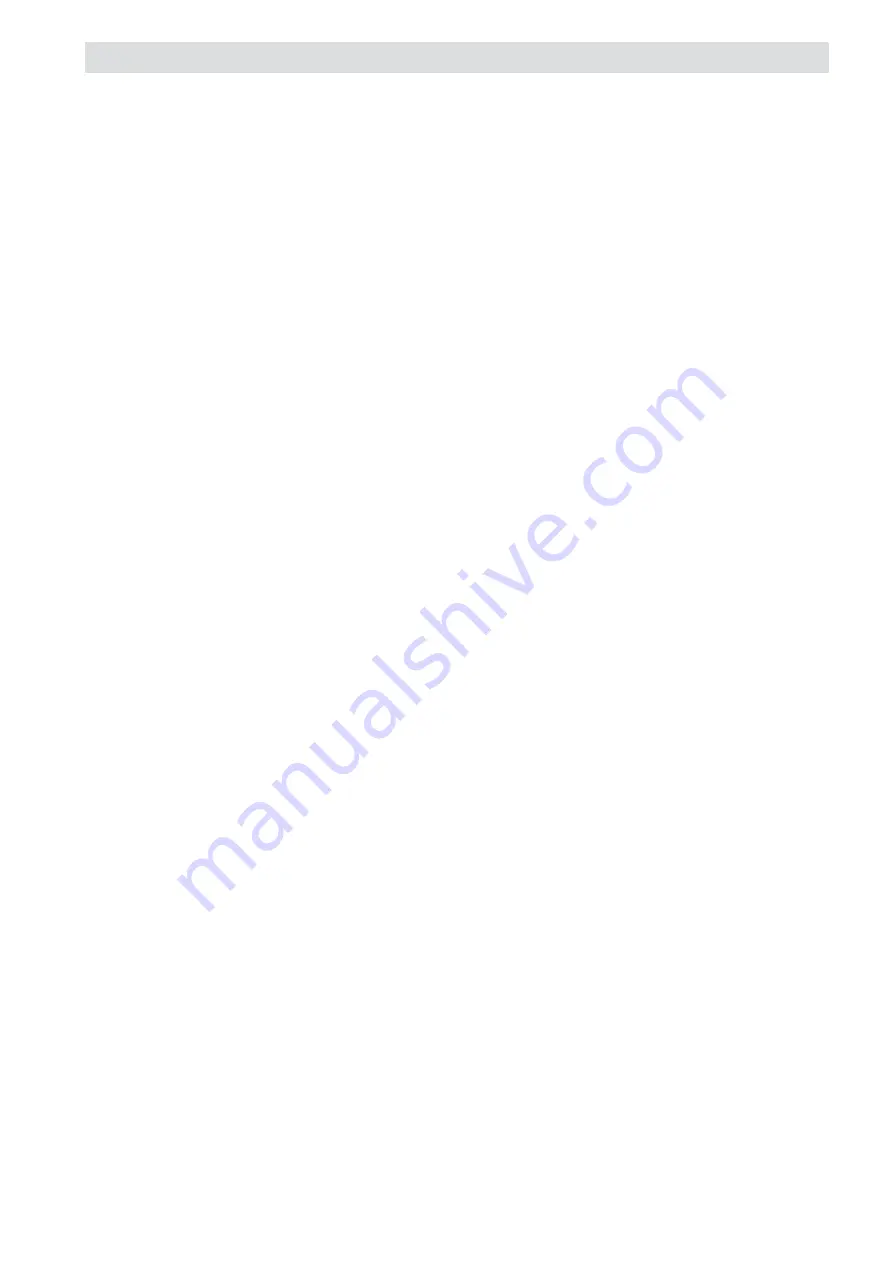
33
9.1 Welding Sequence
9.2 Tips for a Better Weld Result
9. Welding Sequence and Tips
Preparing a Weld/Test Mode
To prepare a weld, the welding parameters must be defined. It is advisable to gradually adjust the parameters while using
small test strips and the same material pairing until a good weld seam can be achieved. Alternatively, the test mode can be
used (see Chapter XY).
Performing a Weld
Press the left pedal (Raise Wheel) of the
pedal unit (7),
to raise the upper rollers. Now place the material as required and
release the pedal. The material is now compressed with the defined clamping pressure. Ensure that there is a sufficiently large
gap in front of the
transport rollers (9),
so that the
welding nozzle (12)
has enough space between the materials. Start the
welding process with the right pedal of the
pedal unit (7)
(Start weld). The
welding nozzle (12)
now moves into the welding
position. Depending on the pre-heating time set, the
transport rollers (9)
begin to turn after a delay and transport the material.
Guide the material freely or using the optional guides. In the meantime, you can interrupt the welding process with the same
pedal. Continue the welding process until the end. As soon as the welding process has stopped, you can completely end it
using the (Raise Wheel) pedal and remove the material.
Switching Off the Machine
Switch off the air supply via the tab. The machine now automatically goes into cool-down mode. Allow the machine to com-
pletely cool down until the pump switches off. You can then operate the
main switch (5)
and switch off the machine.
Material Tension
Try to feed the material into the welding zone with as little tension in the material as possible. In practice, tension is inevitable
but can be significantly reduced by feeding in the material correctly.
Pay attention to how the material leaves the welding zone too. The still warm weld seam should not immediately fall downward
upon leaving the welding zone. The cooling phase should also be as tension-free as possible. It is advisable to use a table or
other similar object on which the material can rest after it leaves the welding zone.
Speed
Feeding in material requires experience. Personnel new to the process should start with a lower welding speed (and an accord-
ingly lower welding temperature) to get a feel for feeding in the material. The speed can then be increased in increments.
Cold Run-Through
To begin with, practice the welding sequence with a complex shape without swiveling in the
welding nozzle (12).
Set the tab
for the
welding nozzle (12)
to “Manual”. By doing this, you can get a feel for the weld shape without damaging the material to
be processed.
Be Ready to Stop the Welding Process
Be mindful of the fact that you can stop the welding process at any time with the right pedal of the
pedal unit (7)
. In the event
of a material feed error, this enables you to stop the welding process and realign the material. With the adjustable pre-heating
time, you can then completely seal the seam.
Save Formulas
Save formulas in a logical place for repeat orders. This makes it considerably easier to determine parameters when welding the
same material again.
Regular Breaks
Working on the Seamtek 900 AT requires a level of concentration – if you feel stressed, take a break.
Guides
Use the guides that are available as accessories. Correctly adjusted guides guide the material and enable a consistent weld
seam. Ask your distributor for information on the various guides available.