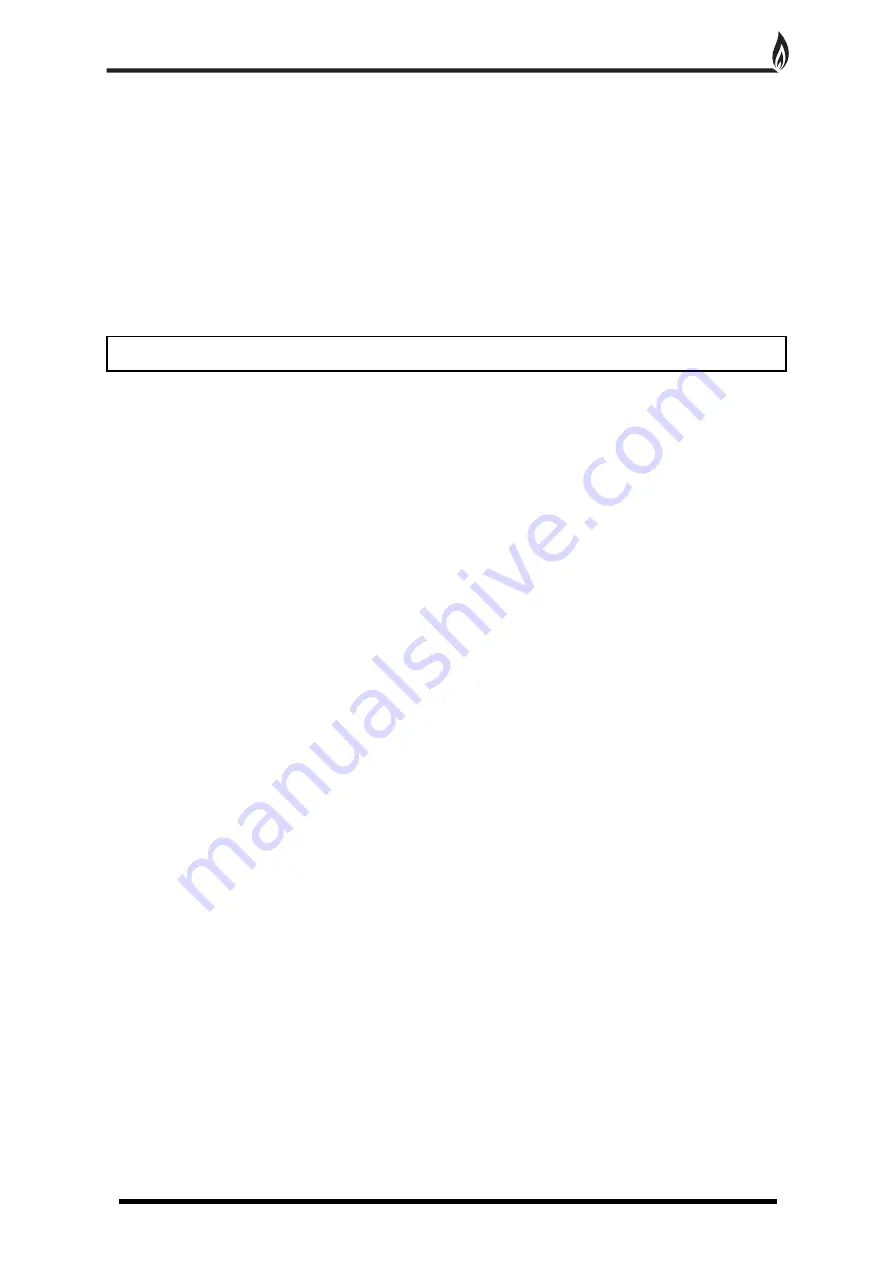
This appliance must only be installed in Great Britain or Ireland.
1. This fire is a natural gas appliance and has been designed for use with the following applications:
a)
Class I
- Conventional brick or stone chimney as used for a solid fuel fire with a cross sectional dimension of
225mm x 225mm (9” x 9”) or a lined flue with a minimum diameter of 175mm (7”), with the fireplace components
conforming to BS1251, or a builders opening a minimum of 560mm high and 406mm wide with a minimum depth
of 230mm to allow sufficient volume for debris collection (unlined chimney 12 dm3 and lined 2 dm3). To obtain this
depth it would not normally be necessary to remove the chair brick. Any permanent flue restrictions or variable
dampers are to be removed or locked in the fully open position. The chimney should also be swept prior to
installation.
b)
Oversized Void
- Where an oversized void is encountered it must be reduced in size by lining with bricks or
blocks or alternatively inserting a metal flue box. The nominal dimensions of the void should not exceed 650mm
wide x 475mm deep x 800mm high BS5871-2.
c)
Class II
- A double walled or insulated metal flue box built to the requirements of BS715 with an insulated flue
having a minimum diameter of 125mm (5”) and a minimum effective overall height of 3 metres (10’).
NOTE
: If the flue box is to be used with an existing brick or stone chimney, a 125mm (5”) minimum diameter
flue liner conforming to BS715 may be used.
2. A non-combustible hearth must be provided to comply with current building regulations. Care should be taken to
prevent any damage being caused to surrounding soft furnishings or decoration, e.g. many embossed vinyl wall
coverings may become discoloured if placed too close to the appliance.
3. A suitable proprietary fire surround with 100
0
c rating may be used with a minimum clearance from hearth to
underside of shelf of 830mm, providing that the depth of shelf is 150mm or less.
4. Where the shelf depth is greater than 150mm, the minimum height clearance should be increased by 25mm
increments for each additional 12.5mm of shelf depth.
5. Minimum width between vertical sides of combustible surround should not be less than 800mm provided the
appliance is central to the surround and the surround legs do not exceed a 150mm profile.
6. If the 150mm profile is exceeded, the width of the surround (and the back panel) should be increased by
25mm for each additional 12.5mm of profile depth.
d)
Pre-cast Flue
conforming to BS 1289 Part 1 (It may be necessary to use a surround with a deeper rebate than
usual to accommodate a flush fit with certain starter blocks. Check the appliance dimensions against individual
applications.
FLUE FLOW TEST
A flue flow test (smoke test) is carried out to check the effectiveness of the flue and to ensure that there is no
leakage into another part of the premises (including any loft), or as appropriate other adjoining premises (this is
particularly important where a number of chimneys combine into a multiple stack).
The flue flow test should be carried out using a suitable smoke pellet which the pellet manufacturer claims to
generate 5m
3
of smoke in 30 seconds burn time.
These gas fires should have the flue flow test carried out with the appliance in position but not connected to the
gas supply so that the smoke test can be carried out with representative flue flow conditions.
A warm flue will be more effective than a cold flue. If the flue is reluctant to draw, which can be initially assessed
by lighting a smoke match at the intended position of the appliance flue connection, introduce some heat into the
flue for a minimum of 10 minutes using a blow torch or other means.
Other factors, such as weather conditions and a combination of materials used to construct the flue can all
influence the flue draught. The pre-heating process may require as much as half an hour before the flue behaves
satisfactory as a blow torch does not represent the volume of heat consistent with the normal appliance operation.
A Flue Flow Test should be checked as follows:
1. Carry out those visual checks as indicated previously, and continue only if satisfactory.
2. Establish that an adequate air supply is available for the combustion of the appliance
3. Close all doors and windows in the room that the appliance is to be installed.
4. Light a smoke pellet at the intended position for the appliance. Place the inset fire case into position.
5. The test is satisfactory if
- there is no significant escape of smoke from the appliance position.
- there is no seepage of smoke over the length of the flue.
- smoke is discharged only from the correct terminal.
VENTILATION
No special ventilation bricks or vents are required in the room containing the appliance, providing that normal
adventitious room ventilation exists. The installer must determine this by carrying out a spillage test.
SPILLAGE TEST
To check for satisfactory clearance of products of combustion, close all doors and windows and leave the fire
burning for ten minutes. Insert a lit smoke match into the left and right hand ducts immediately above the glass
retaing strip. It should NOT be inserted into the central duct. This operation should be carried out before fitting the
trim and louvred panel. All the smoke must be drawn into the flue. If spillage occurs, allow a further ten minutes
and repeat the test. Should spillage still occur turn the appliance off and seek expert advice. To continue the test:
If an extractor fan is situated in the room the test should be repeated with the fan running. If there is a connecting
room with an extractor fan the test should be repeated with all the doors to that room open and the extractor fan
running.
INSTALLATION REQUIREMENTS
4