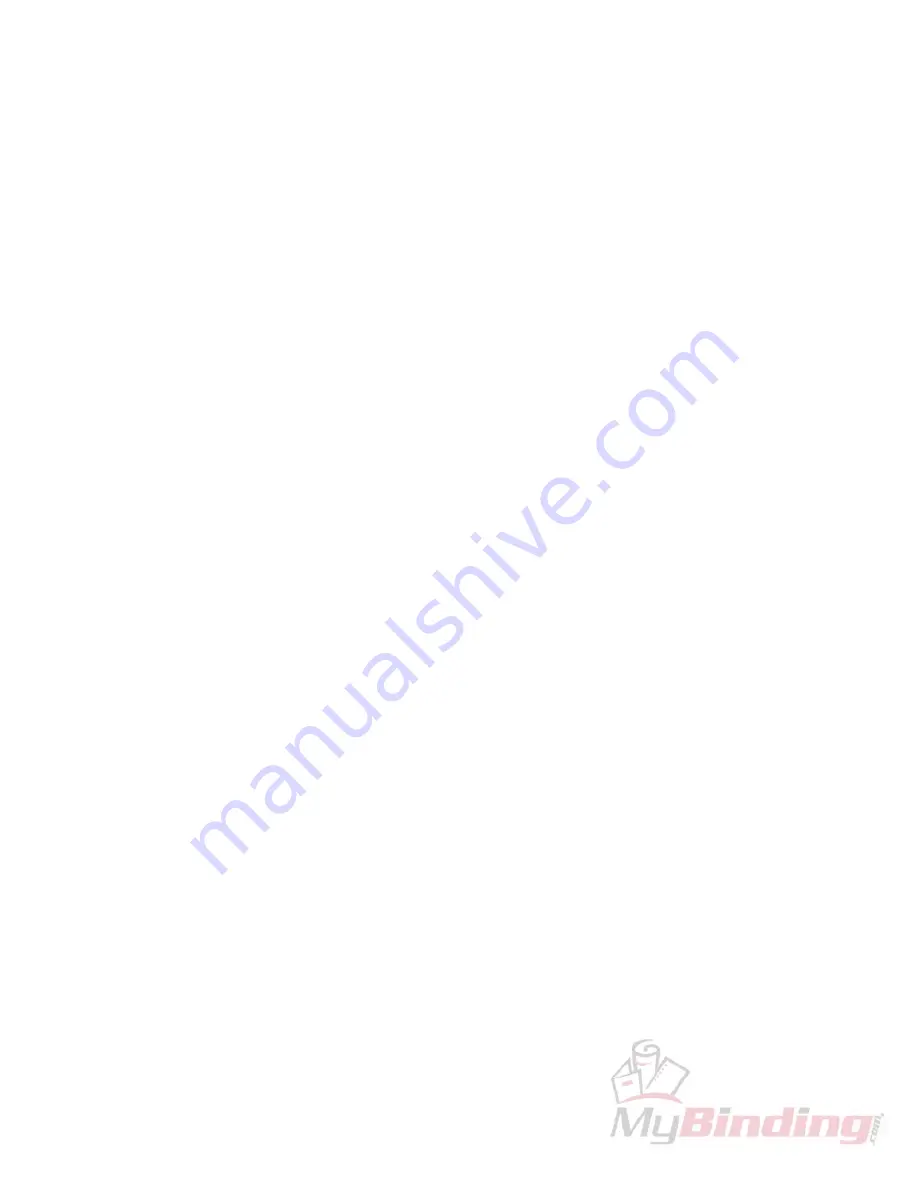
16
3 -3 A P P L IC A T IO N N O T E S F O R P S A L A M IN A T IN G A N D
M O U N T IN G
L A M IN A T IO N :
With the SIGNMASTER 44 laminator now properly threaded with film, it is now
ready for continuous and/or interrupted lamination duty.
The quality of the finished lamination depends on several factors, such as: film
quality, substrate, items to be laminated, lamination pressure, and correct
feeding technique. To assure the highest quality lamination possible, some
degree of experimentation is required. The following are some helpful hints:
•
To remove wrinkles during initial threading and set up, TURN OFF THE
MACHINE, open the laminating rollers. Gently pull the film and backing
release paper at the exit point until all wrinkles are removed. Close the
laminating rollers as film is being pulled taut over the rollers. This will
conserve more material than trying to run the wrinkles out with the laminator.
•
When using release paper to prevent adhesive buildup on the rollers be sure
to closely match the widths of paper and film.
•
When using smaller (widthwise) substrates it becomes most practical to set
up and laminate these subjects as near the center of the roll as possible.
•
Films for protecting images printed on vinyl should be made of vinyl
themselves so that the flexibility of the vinyl substrate is not impaired.
Polyester films are not recommended over vinyl because of their stiffness.
•
When laminating only one side, you must not allow exposed adhesive to go
into the machine. Make sure the material being coated is at least as wide as
the roll of film. If material being laminated is narrower than the film, be sure to
run release paper off of the bottom supply roll. (see options) When not using
release paper be sure to overlap sheets of scrap paper under the film, leaving
no exposed adhesive. Eliminating exposed adhesive will decrease chances
of creating a wraparound.
S U P P L Y R O L L T E N S IO N :
A small amount of tension is needed for most jobs. Too little tension and too
much tension can both cause wrinkling. The right amount of tension is the least
amount that will do the job.
Most tapes and pressure sensitive films do not require a great deal of roll
pressure. Roll pressure is set at the factory and rarely needs adjustment.