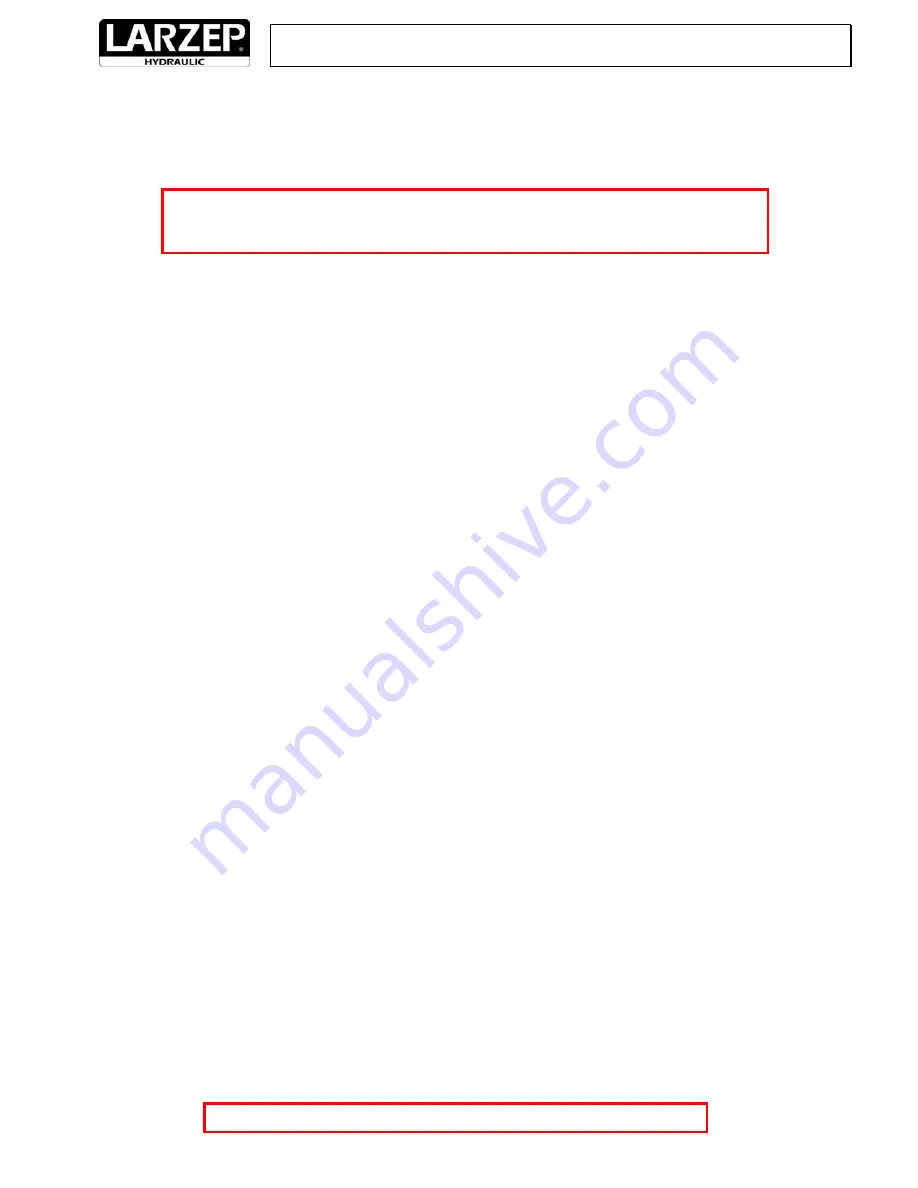
7
Manual de Instrucciones
/ Instruction Manual
Bomba de Aluminio W20507, W21107
Aluminium Hand Pump
CYLINDER-HAND PUMP INSTRUCTIONS
Unpack and visually check all the components, making sure that there are no oil leaks, loose or damaged couplers, damaged threads, etc. Never
use components that are damaged or appear to be in poor condition.
Assemble the device in accordance with the instructions given in the diagram, first checking that you have all the necessary material.
Check the correct installation and perfect functioning of the device without load, in accordance with the procedure outlined below:
WARNING:
The plastic shipping plug is used to trap any residue oil from leaking out of port during shipment. Do not operate pump with the plastic
shipping plug installed, oil may expel if pump is operated with this plug installed.
1.
Release the pump drive lever by removing the hook from the lever-holder housing.
2.
Pump manually with the drive screw open (rotate a few times to loosen) in order to fill the pump’s internal circuit with oil.
3.
Close the drive screw by turning clockwise manually. You do not need to close too tightly.
4.
Now pump using the drive lever. First, fill the hose with oil. The number of strokes required will depend on the length of the hose and the flow
supplied by the pump piston. With two-speed pumps, the large piston will be activated during the load-free movement for rapid advance, and
when the device comes into contact with the load, the pump automatically transfers over to the second stage and only the oil supplied by the
small piston will be available up to 700 kg/cm
2
, which is the maximum pressure for the device.
5.
Once the hose is full of oil, the cylinder piston will start to advance.
6.
If the cylinder has a mechanical limit switch capable of withstanding the maximum device pressure, continue pumping until the limit switch is
reached.
7.
If any control elements (pressure gauges) are available, you will be able to see how the pressure increases along with the effort required to
move the lever.
8.
Keep pumping until you obtain the maximum pressure (700 kg/cm
2
). In this way you will be able to check the correct functioning of the safety
valve and the absence of oil leaks in the installation.
9.
Maintain pressure in the installation for a short period of time (1 minute) without pumping, in order to check the correct functioning of the
pump’s check valve.
10. Gently open the pump’s drive screw (by turning anticlockwise) in order to protect the fall of the pressure gauge needle. Do not force the drive
screw open. The cylinder will not move back more quickly because the screw is looser. A couple of turns will be enough.
11. If the cylinder has a return spring (SM, SMP, SMX, SH, TE, T, SAM, SAH, SATM, CY, KC) the piston will move back automatically. The return
speed may be slow in some applications. In this case, we recommend the use of double effect cylinders. In the case of load return cylinders
(SP, SPR, SX, SL, SSR, STR, STX, SAT), you will need to push the piston back using more or less force, depending on the size and position
of the cylinder.
12. In cylinders without a mechanical end of stroke (SSR, STR, STX) this type of test cannot be carried out. If you do not have a test bench, you
will have to test the installation using the actual load in the application. This operation should be carried out with extreme care by experienced
personnel and maximum safety measures should be applied.
13. Repeat the processes as many times as necessary until you are comfortable handling the device.
14. If using close or check valves, or working with various cylinders via flow distributors, remember to take into consideration the effect these
accessories may have on the functioning of the device, and establish an operating procedure in order to avoid unwanted effects.
15. These pumps can be operated in horizontal and vertical position. When using the hand pump in the vertical position it is imperative to place the
hand pump with pump head facing down towards the earth and the pump handle facing upwards towards the sky.
MAINTENANCE
Oil level check.
-
Check oil level regularly. Drain oil and refill with Larzep oil every 12 months. If pump is used in dirty environments, change the oil more
often. Filter the oil before filling up the pump
-
This check must be carried out with the cylinder fully retracted. Excessive amount of oil in the tank will lead to internal pressures which will
hamper the function of the pump.
-
Remove vent/fill cap from reservoir and fill the reservoir only to level mark shown on pump.
-
Remove air from the system if necessary. For that: close release valve; position hand pump at higher elevation than tool and the tool with
the coupler higher than the moving end; fully advance the tool, open release valve to retract tool several times to expel the trapped air in
pump circuit. Repeat the above steps as necessary until all of the air is expelled from pump’s hydraulic circuit. Re-check oil level after
removing air.
-
Return vent/fill cap to proper position.
Once the equipment is being used the areas exposed to wear and oxidation must be cleaned and greased.
The pumps must always be handled and repaired by qualified personnel.
Apply 2 rounds of teflon around all 3/8” NPT male threads of the system, in the thread direction,
leaving the first wire of the thread free of tape to prevent the tape breaking.
Tightening Torque: 100 Nm.