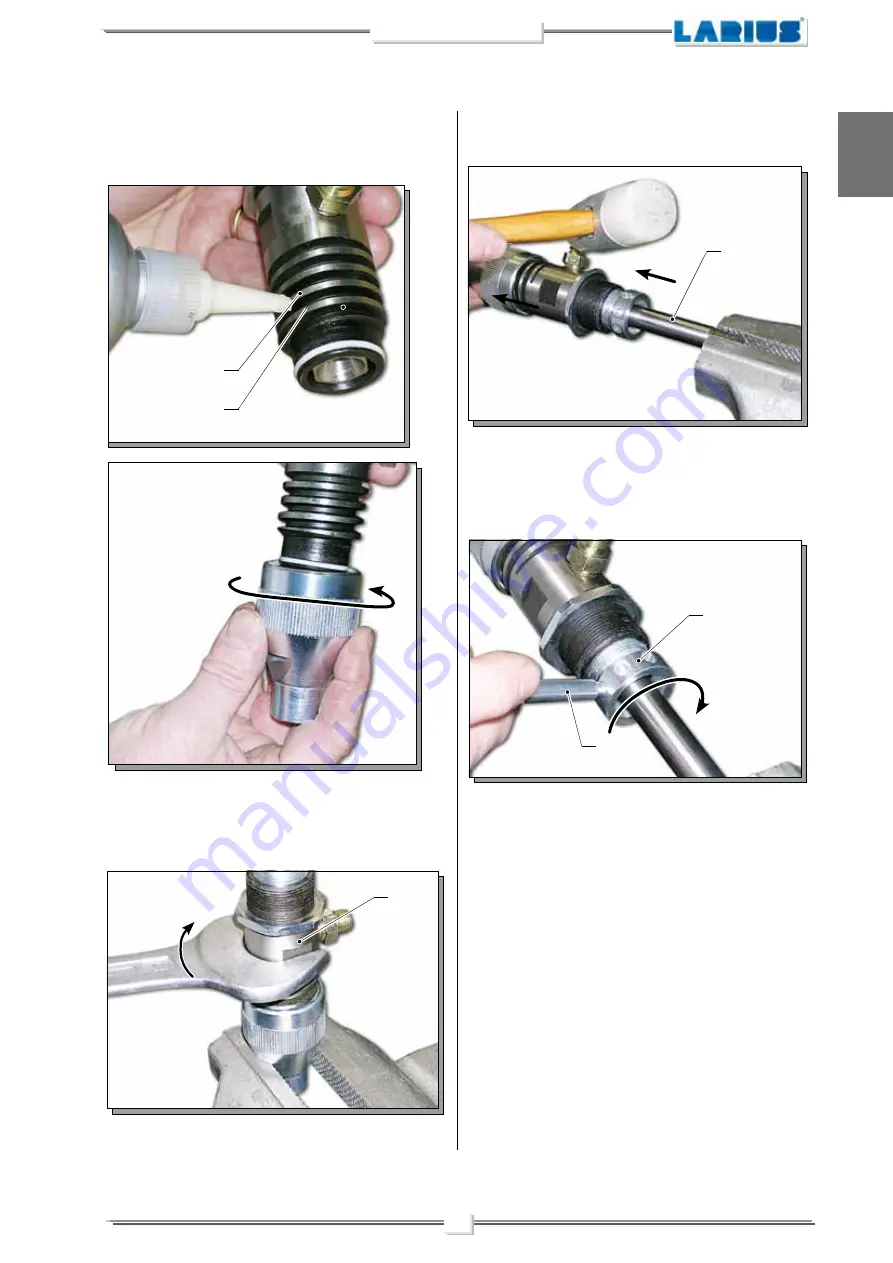
27
EXCALIBUR LINER
English
•
Put liquid Teflon on the first two turns (
N30
) and (
N31
) to avoid
the two components coupled as shown from unscrewing.
•
Use a 36 mm spanner to screw on the pump unit (
N9
).
•
Make the piston stem (
N18
) fitted previously complete a full
stroke as shown.
•
Use the pin (
N11
) supplied to tighten the gasket compression
ring nut (
N10
).
Close this until it is fully touching, without forcing.
CORRECT POSITIONING OF THE PUMP UNIT
Once the unit has been refitted, proceed as follows:
•
Check the position of the con rod, which should be positioned
at its lower stopping point.
•
Put the entire pump unit (
N9
) inside the reduction cover (
N32
)
as shown.
N31
N30
N9
N18
N10
N11