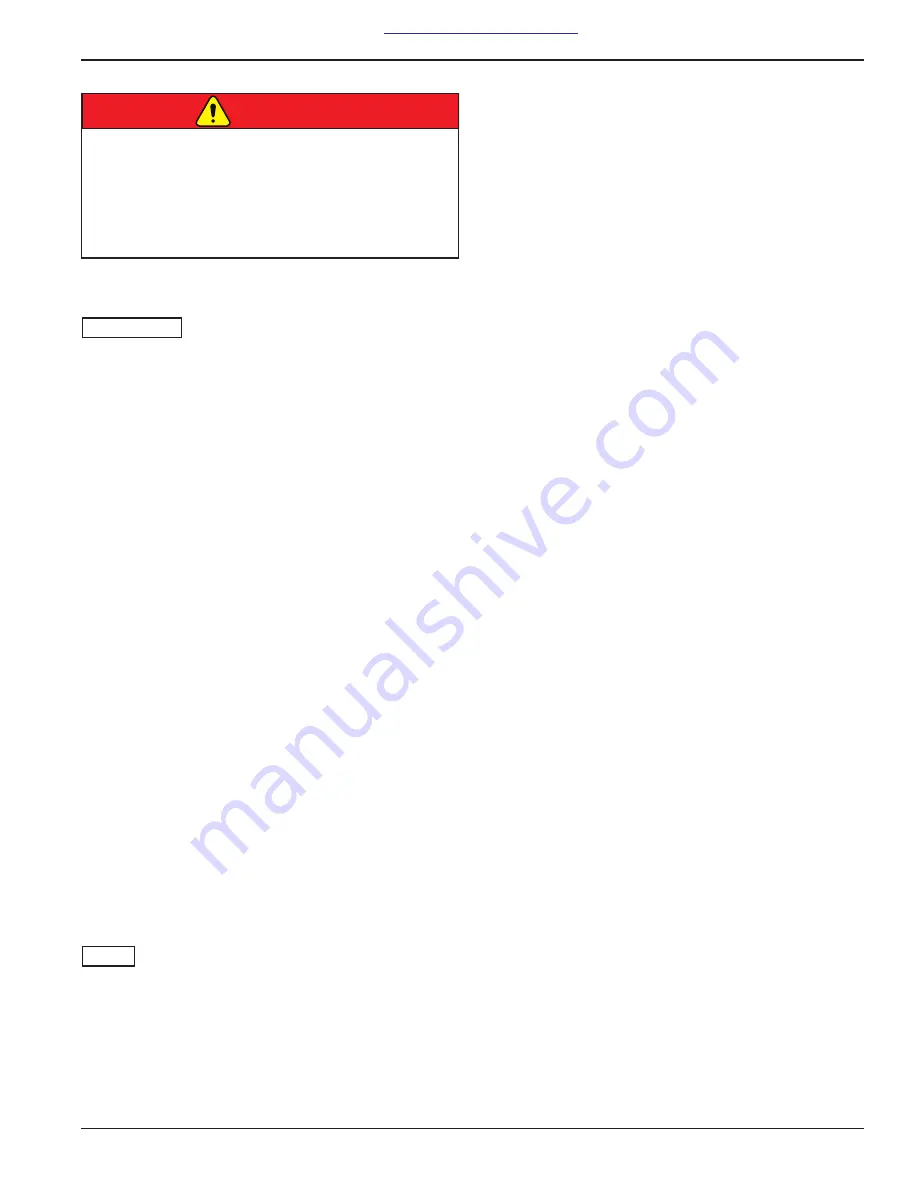
INTRODUCTION AND SAFETY INFORMATION
1-3
DANGER
Transporting Safety
IMPORTANT
It is the responsibility of the owner/operator to
comply with all state and local laws.
1. When transporting the implement on a road or
highway, use adequate warning symbols, reflectors,
lights and slow moving vehicle sign as required. Slow
moving tractors and towed implements can create a
hazard when driven on public roads. They are
difficult to see, especially at night.
2. Do not tow an implement that, when fully loaded,
weighs more than 1.5 times the weight of the towing
vehicle.
3. Carry reflectors or flags to mark the tractor and
implement in case of breakdown on the road.
4. Do not transport at speeds over 20 MPH under good
conditions. Never travel at a speed which does not
allow adequate control of steering and stopping.
Reduce speed if towed load is not equipped with
brakes.
5. Avoid sudden stops or turns because the weight of
the implement may cause the operator to lose control
of the tractor. Use a tractor heavier than the
implement.
6. Use caution when towing behind articulated steering
tractors; fast or sharp turns may cause the implement
to shift sideways.
7. Keep clear of overhead power lines and other
obstructions when transporting. Know the transport
height and width of your implement.
Attaching, Detaching, and Storage
NOTE
The implement jack stands must be stored “off machine”
for all
folding machines
during transport and field
operation. This is true for both front and rear jack stands.
1. Do not stand between the tractor and implement
when attaching or detaching implement unless both
are not moving.
2. Block implement so it will not roll when unhitched
from the tractor.
3. Store in an area where children normally do not play.
Maintenance Safety
1. Understand the procedure before doing the work.
Use proper tools and equipment.
2. Make sure all moving parts have stopped.
3. Do not make adjustments or lubricate implement
while it is in motion.
4. Block the implement so it will not roll when working
on or under it to prevent injury.
High Pressure Fluid Safety
1. Escaping fluid under pressure can be nearly invisible
and have enough force to penetrate the skin causing
serious injury. Use a piece of cardboard, rather than
hands, to search for suspected leaks.
2. Any fluid injected into the skin must be surgically
removed within a few hours or gangrene may result.
3. Avoid the hazard by relieving pressure before
disconnecting hydraulic lines.
Protective Equipment
1. Wear protective clothing and equipment.
2. Wear clothing and equipment appropriate for the job.
Avoid loose fitting clothing.
3. Because prolonged exposure to loud noise can
cause hearing impairment or hearing loss, wear
suitable hearing protection, such as earmuffs or
earplugs.
Chemical Safety
1. Agricultural chemicals can be dangerous. Improper
use can seriously injure persons, animals, plants, soil
and property.
2. Read chemical manufactures instructions and store
or dispose of unused chemicals as specified.
3. Handle chemicals with care and avoid inhaling
smoke from any type of chemical fire.
4. Store or dispose of unused chemicals as specified by
the chemical manufacturer.
Prepare for Emergencies
1. Keep a First Aid Kit and Fire Extinguisher handy.
2. Keep emergency numbers for doctor, ambulance,
hospital and fire department near the phone.
• Do not allow anyone to ride on the tractor or
implement. Riders could be struck by foreign
objects or thrown from the implement.
• Never allow children to operate equipment.
• Keep bystanders away from implement during
operation.
Summary of Contents for 2511 IN-3-30 2511 N-4-30 2511 N-5-30
Page 28: ...2 20 F 1040 0123 STANDARD SPECIFICATIONS TABLE OF CONTENTS NOTES...
Page 46: ...3 18 F 1040 0123 ASSEMBLY INSTRUCTIONS TABLE OF CONTENTS Table provided for general use NOTES...
Page 56: ...5 2 F 1040 0123 TROUBLESHOOTING GUIDE TABLE OF CONTENTS NOTES...
Page 58: ...6 2 F 1040 0123 QUICK START GUIDES TABLE OF CONTENTS Table provided for general use NOTES...