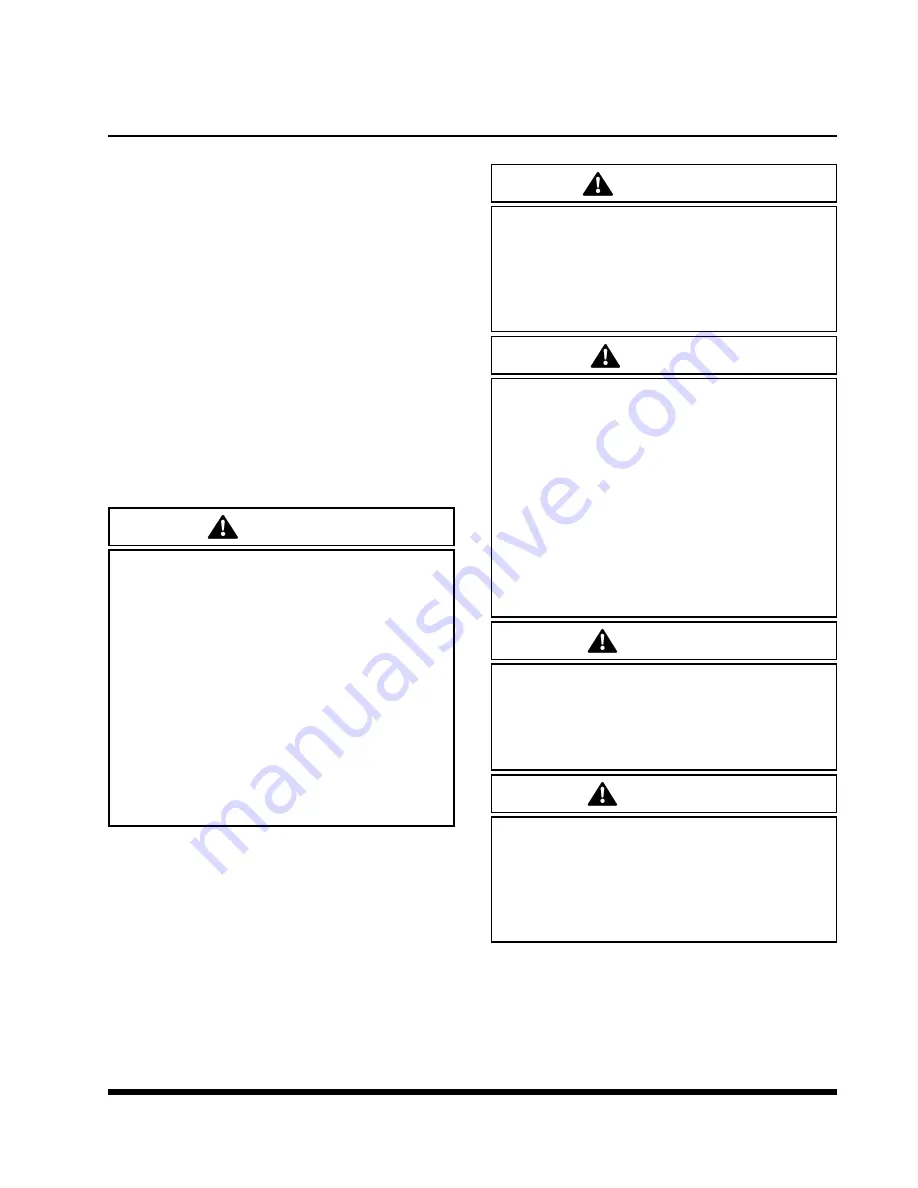
3
ASSEMBLY PROCEDURES
It is very important that your new
2210 Series
Weatherproofer
be properly assembled, adjusted,
and lubricated before use. Illustrations to assist
with the assembly process are provided in Section
2, “Standard Specifications”. Illustrations are pro-
vided in this section to show proper shank, disc
gang, and mounting bracket spacings. Remove
paint from grease fittings and replace any that are
damaged or missing. Be sure to replace bolts,
clips, etc. in the same place from where they were
removed.
To insure assemblies are aligned,
insert all
bolts and leave the nuts loose until completion
of final assembly
. Use lockwashers or flat wash-
ers where called for. Spread all cotter pins.
After completion of final assembly, tighten all
nuts
evenly
to prevent misalignment, distortion, or
binding. Tighten all bolts and nuts to the recom-
mended torques shown in
Table 2-1, “Standard
Bolt Torques.”
DANGER
DISC BLADES ARE EXTREMELY
SHARP. EXERCISE EXTREME CARE
WHEN WORKING ON OR NEAR DISC
BLADES. DO NOT ALLOW DISCS TO
ROLL OVER OR FALL ONTO ANY BOD-
ILY
PART.
DO
NOT
ALLOW
WRENCHES TO SLIP WHEN WORKING
NEAR DISC BLADES. NEVER PUSH
WRENCHES TOWARD DISC BLADES.
DO NOT CLIMB OVER MACHINE
ABOVE DISC BLADES. FAILURE TO
STAY CLEAR OF DISC BLADE EDGES
CAN CAUSE SERIOUS PERSONAL IN-
JURY OR DEATH.
WARNING
DO NOT ATTEMPT TO LIFT HEAVY
PARTS (SUCH AS THE FRAME, DISC
GANGS, ROCK SHAFT, AND PULL
HITCH) MANUALLY. USE A HOIST OR
A FORK LIFT TO MOVE THESE PARTS
INTO POSITION.
DANGER
TO PREVENT ACCIDENTAL LOWER-
ING:
1. ALL HYDRAULICALLY ELEVATED
EQUIPMENT MUST BE LOCKED OUT
USING THE CYLINDER LOCKOUTS:
2. LOWER EQUIPMENT TO THE
GROUND WHILE SERVICING OR
WHEN IT IS IDLE.
FAILURE TO TAKE MEASURES TO
PREVENT ACCIDENTAL LOWERING
MAY RESULT IN SERIOUS PERSONAL
INJURY OR DEATH.
CAUTION
BE SURE DEPTH STOPS ARE EQUAL
LENGTHS ON ALL CYLINDERS. USING
UNEQUAL DEPTH STOP LENGTHS
CAN CAUSE PERMANENT EQUIP-
MENT DAMAGE.
CAUTION
BE SURE TO BLEED THE HYDRAULIC
SYSTEM OF ALL AIR IN LINES AFTER
INSTALLATION. FAILURE TO BLEED
THE SYSTEM OF ALL AIR CAN RE-
SULT IN IMPROPER MACHINE OPERA-
TION.
3-1
Summary of Contents for 2210
Page 6: ......
Page 8: ......
Page 12: ...NOTES 2 4...
Page 13: ...2 5 Figure 2 1 2215 3 30 Shank Disc Spacing NOTE DISC GANG ANGLE SHOWN IS 20o...
Page 14: ...2 6 Figure 2 2 2215 4 24 Shank Disc Spacing NOTE DISC GANG ANGLE SHOWN IS 20o...
Page 15: ...2 7 Figure 2 3 2215 4 30 Shank Disc Spacing NOTE DISC GANG ANGLE SHOWN IS 20o...
Page 16: ...2 8 Figure 2 4 2215 5 24 Shank Disc Spacing NOTE DISC GANG ANGLE SHOWN IS 20o...
Page 17: ...2 9 Figure 2 5 2215 5 30 Shank Disc Spacing NOTE DISC GANG ANGLE SHOWN IS 20o...
Page 18: ...2 10 Figure 2 6 2215 6 30 Shank Disc Spacing NOTE DISC GANG ANGLE SHOWN IS 20o...
Page 19: ...2 11 Figure 2 7 2217 5 30 Shank Disc Spacing NOTE DISC GANG ANGLE SHOWN IS 20o...
Page 20: ...2 12 Figure 2 8 2217 6 30 Shank Disc Spacing NOTE DISC GANG ANGLE SHOWN IS 20o...
Page 21: ...2 13 Figure 2 9 2217 7 24 Shank Disc Spacing NOTE DISC GANG ANGLE SHOWN IS 20o...
Page 22: ...2 14 Figure 2 10 2217 7 30 Shank Disc Spacing NOTE DISC GANG ANGLE SHOWN IS 20o...
Page 23: ...2 15 Figure 2 11 2217 8 30 Shank Disc Spacing NOTE DISC GANG ANGLE SHOWN IS 20o...
Page 24: ...2 16 Figure 2 12 2217 9 24 Shank Disc Spacing NOTE DISC GANG ANGLE SHOWN IS 20o...
Page 26: ...3 2 Figure 3 1 2217 Frame Assembly...
Page 28: ...3 4 Figure 3 2 2215 Rockshaft Installation Figure 3 3 2215 Gauge Wheel Cylinder Installation...
Page 30: ...3 6 Figure 3 4 2217 Rockshaft Installation Figure 3 5 2217 Gauge Wheel Cylinder Installation...
Page 34: ...3 10 Figure 3 7 Pull Hitch Installation...
Page 36: ...3 12 Figure 3 8 Rigid Riser Disc Gang Installation...
Page 38: ...3 14 Figure 3 9 Flex Disc Gang Installation...
Page 40: ...3 16 Figure 3 10 Spring Shank Installation...
Page 45: ...4 3 Figure 4 2 2210 Series Lubrication Schedule...
Page 47: ...4 5 Figure 4 4 2210 Series Spacer Block Placement...
Page 50: ...NOTES 4 8...
Page 52: ...NOTES 5 2...