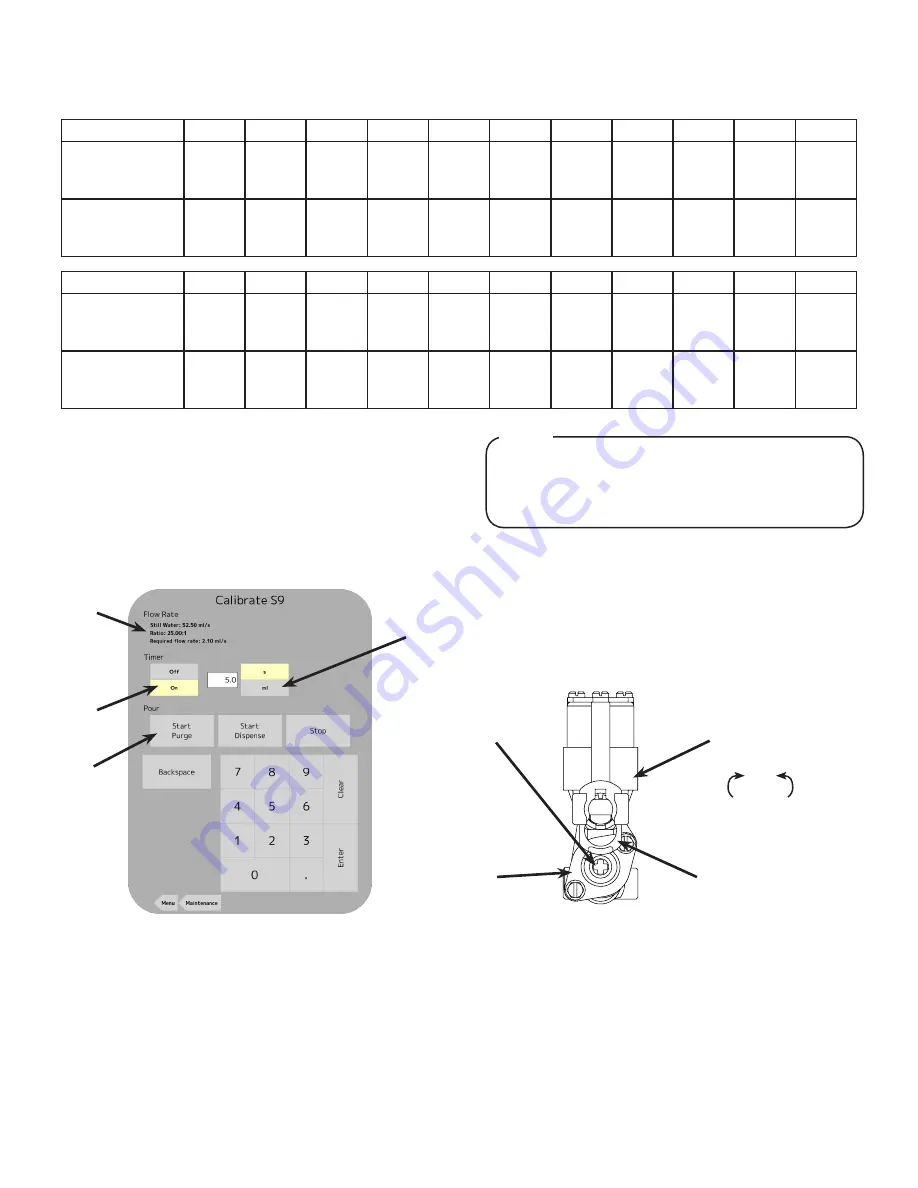
10
Ratio Settings Table:
The table below shows the flow rate for the plain water modules and the volume of syrup dispensed after a 4 second pour, for different
ratio settings (All at a finished drink flow rate of 60 ml/sec):
Ratio
5
5.2
5.4
5.6
5.8
6
6.2
6.4
6.6
6.8
7
Plain Water
Flow Rate (ml/s)
50
50.32
50.63
50.91
51.18
51.43
51.67
51.89
52.11
52.31
52.50
Volume of Syrup
(4 sec.) (ml)
40
38.71
37.50
36.36
35.29
34.29
33.33
32.43
31.58
30.77
30
Ratio
7.2
7.4
7.5
7.6
7.8
8
8.2
8.4
8.6
8.8
9
Plain Water
Flow Rate
52.68
52.86
52.94
53.02
53.18
53.33
53.48
53.62
53.75
53.88
54
Volume of Syrup
(4 sec.)
29.27
28.57
28.24
27.91
27.27
26.67
26.09
25.53
25
24.49
24
Calibrating Flavor Modules
1. From the Maintenance menu, press the
Calibrate
tab on the
far left side of the screen and press the
Calibrate
button for
any designated flavor module.
2. The water flow rate should be set from the calibration of
the plain water module in the previous section and the ratio
should be determined from when the flavor was configured.
(See page 6,
Adding New Brand/Flavor Module
)
3. Set the Timer to the ON position and select seconds (s) as
the desired unit of measurement.
4. Using the keypad, enter in a time of 5 seconds as the preset
dispensing time.
5. With the graduated cylinder placed in a position below the
nozzle, press the
Start Purge
button. The unit will dispense
the designated flavor for 5 seconds.
6. Examine the dispensed volume in the graduated cylinder.
7. If the dispensed volume does not match the value of 10.5 ml,
(see note above) remove the protective cap for the corre-
sponding valve and use a screwdriver to adjust the flavor
flow control.
A
B
C
D
A. Flow Rate/Ratio C. Start Purge Button
B. Timer Icon
D. Unit Icon
The finished drink flow rate was set to 60 ml/sec, which
makes the finished flavor flow rate 2.1 ml/s. In
5 seconds, the volume of syrup that should be
dispensed is 10.5 ml.
NOTE
8. Repeat steps 5-7 if any more bonus flavor flow adjustment is
necessary.
9. Repeat steps 2-8 for any remaining bonus flavor module.
10. Re-install top plate, splash plate, and cup rest. (See page 4)
A
B
C
D
Increase
Decrease
A. Flow Control
B. Valve Retainer
C. Solenoid
D. Valve Body