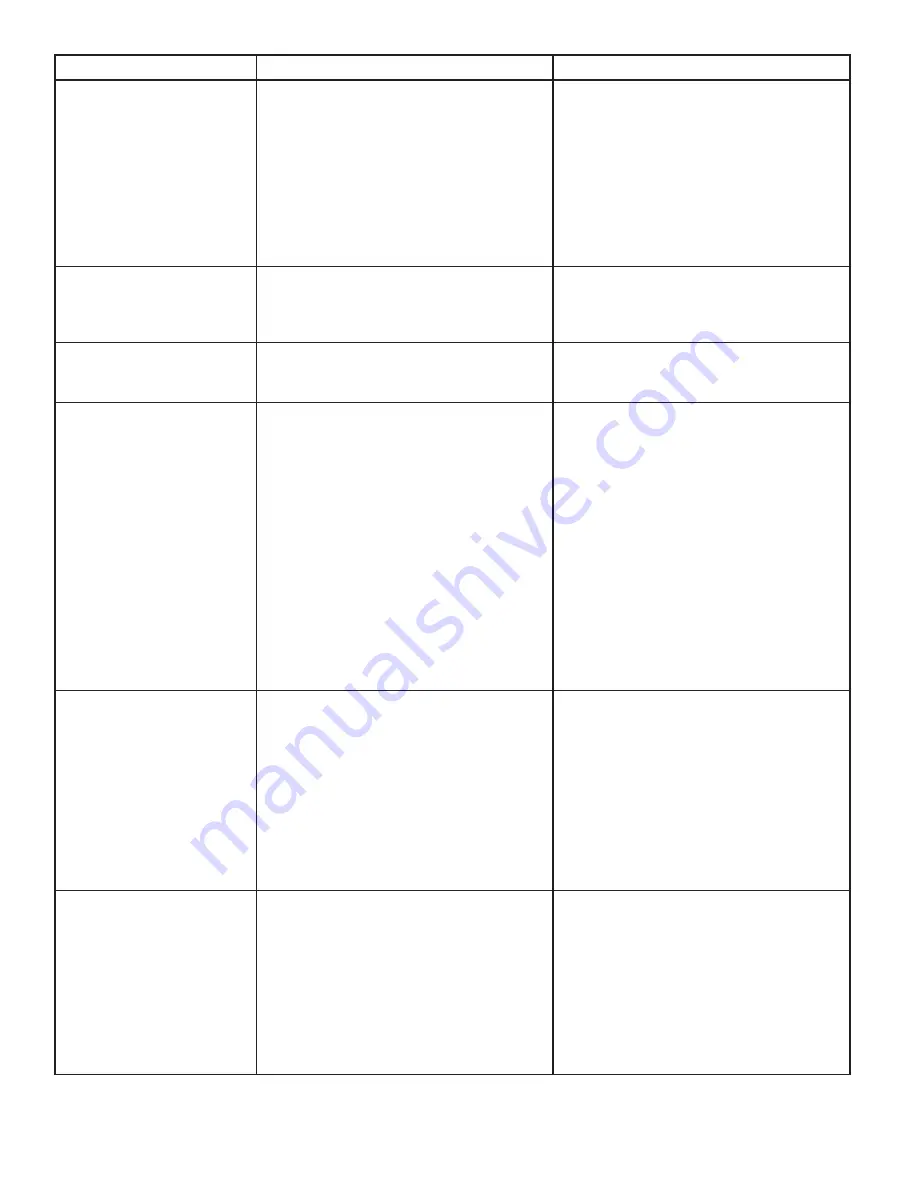
20
TROUBLE
CAUSE
REMEDY
Insufficient syrup flow.
1.
Insufficient CO
2
pressure to BIB pumps.
2.
Shutoff on mounting block not fully open.
3.
Foreign debris in syrup flow control.
4. Defective BIB pump.
1. Adjust CO
2
pressure to BIB pumps to 80
psi (0.552 MPa) (min. 70 psi (0.483 MPa).
Do not exceed manufacturer’s
recommendations.
2.
Open shutoff fully.
3.
Remove syrup flow control from valve and
clean out any foreign material to ensure
smooth spool movement.
4. Replace pump.
Valve will not shut off.
1. Debris in paddle arms.
2. Solenoid plunger sticking.
1. Activate valve a few times to free debris.
Clean out any foreign material.
2. Replace solenoid coil.
Water continually leaking at
connections.
1. Loose water connections.
2.
Flare seal washer leaks.
1. Tighten water connections.
2.
Replace flare seal washer.
Water only dispensed, no
syrup. Or syrup only dispensed,
no water.
1. Syrup BIB empty.
2.
Water or syrup shutoff on mounting block
not fully open.
3.
Improper or inadequate water or syrup
supply.
4. CO
2
pressure to syrup pump too low.
5. Stalled or inoperative BIB pump.
6. Kinked line.
7. CO
2
regulator malfunction.
1.
Replace syrup BIB as required.
2.
Open shutoff completely.
3.
Remove valve from mounting block &
open shutoffs slightly. Check water &
syrup supply. If no supply, check unit for
other problems. Ensure BIB connection is
engaged.
4. Check the CO
2
pressure to the pump to
ensure it is between 70-80 psi (0.483-
0.552 MPa).
5. Check CO
2
pressure and/or replace pump.
6. Remove kink or replace line.
7. Repair or replace CO
2
regulator as
required.
Syrup only dispensed. No
water, but CO
2
gas dispensed
with syrup.
1.
Improper water flow to dispenser.
2. Carbonator pump motor has timed out.
3.
Liquid level probe not connected properly
to PCB.
4. Defective PCB assembly.
5.
Defective liquid level probe.
6. Weak or defective carbonator pump.
1.
Check for water flow to dispenser.
2.
Reset by turning the unit OFF, then ON
by using the circuit breaker on the power
supply or momentarily unplugging unit.
3.
Check connections of liquid level probe to
PCB assembly.
4. Replace PCB assembly.
5.
Replace liquid level probe.
6. Replace pump.
Excessive foaming.
1. No ice in bin.
2. Incoming water or syrup temperature too
high.
3. CO
2
pressure too high.
4.
Water flow rate too high.
5.
Nozzle and diffuser not clean.
6. Air in BIB lines.
1.
Fill bin with ice and allow coldplate to
re-stabilize.
2. Correct prior to dispenser.
3. Adjust CO
2
pressure downward, but not
less than 70 psi (0.483 MPa).
4. Re-adjust and reset ratio.
5. Remove and clean.
6. Bleed air from BIB lines.
Summary of Contents for Sensation 44
Page 25: ...25 Flavor Shot Box Plumbing Diagram Unit Plumbing Diagram ...
Page 26: ...26 Wiring Diagram 115 Volt ...
Page 27: ...27 Wiring Diagram 220 240 Volt ...
Page 29: ...29 ...