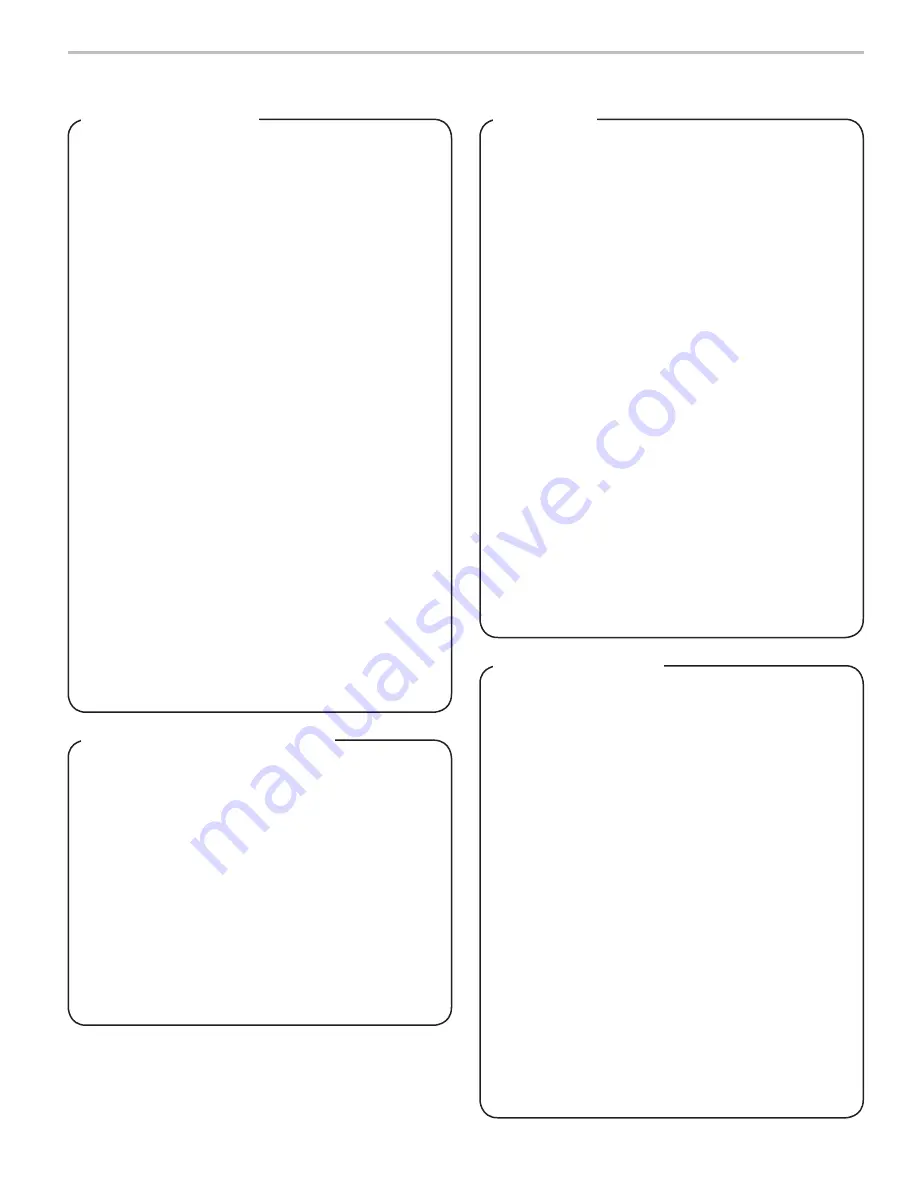
3
•
The dispenser is for indoor use only
•
This appliance is intended to be used in commercial
applications such as restaurants or similar.
•
This appliance should not be used by children or
infirm persons without supervision.
•
This appliance is not intended for use by persons
(including children) with reduced physical, sensory
or mental capabilities, or lack of experience and
knowledge, unless they have been given supervision
or instruction concerning use of the appliance by a
person responsible for their safety.
•
This appliance can be used by children aged from 8
years and above and persons with reduced physical,
sensory or mental capabilities or lack of experience
and knowledge if they have been given supervision or
instruction concerning use of the appliance in a safe
way and understand the hazards involved.
•
Cleaning and user maintenance shall not be
performed by children without supervision.
•
This unit is not a toy and children should be advised
not to play with the appliance.
•
The min/max ambient operating temperature for the
dispenser is 40°F to 90°F (4°C to 32°C).
•
Do not operate unit below minimum ambient operation
conditions.
•
Should freezing occur, cease operation of the unit and
contact authorized service technician.
•
The maximum tilt for safe operation is 5°.
•
This appliance must be installed and serviced by a
professional.
!
Intended Use
•
Follow all local electrical codes when making
connections.
•
Check the dispenser name plate label, located behind
the splash plate
for correct electrical requirements of
unit.
DO NOT
plug into a wall electrical outlet unless
the current shown on the serial number plate agrees
with local current available.
•
Each dispenser must have a separate electrical
circuit.
• DO NOT
use extension cords with this unit.
• DO NOT
‘gang’ together with other electrical devices
on the same outlet.
• WARNING:
Always disconnect electrical power to the
unit to prevent personal injury before attempting any
internal maintenance.
•
The resettable breaker switch should not be used as
a substitute for unplugging the dispenser from the
power source to service the unit.
•
Only qualified personnel should service internal
components of electrical control housing.
• WARNING:
Make sure that all water lines are tight and
units are dry before making any electrical connections
•
If this dispenser is installed in an area that is
susceptible to ±10% variation of the nominal line
voltage, consider installing a surge protector or similar
protection device.
F
Power
IMPORTANT SAFETY INSTRUCTIONS
• WARNING:
Carbon Dioxide (CO2) is a colorless,
noncombustible gas with a light pungent odor. High
percentages of CO
2
may displace oxygen in the
blood.
• WARNING:
Prolonged exposure to CO
2
can be harmful.
Personnel exposed to high concentrations of CO
2
gas
will experience tremors which are followed by a loss
of consciousness and suffocation.
• WARNING:
If a CO
2
gas leak is suspected, immediately
ventilate the contaminated area before attempting to
repair the leak.
• WARNING:
Strict attention must be observed in the
prevention of CO
2
gas leaks in the entire CO
2
and soft
drink system.
5
Carbon Dioxide (CO
2
)
•
Provide an adequate, potable water supply. Water
pipe connections and fixtures directly connected to
a potable water supply must be sized, installed, and
maintained according to federal, state, and local
codes.
•
The water supply line must be at least a 3/8 inches
(9.525 mm) pipe with a minimym of 25 PSI (0.172
MPA) line pressure, but not exceeding a maximum of
50 PSI (0.345 MPA). Water pressure exceeding 50
PSI (0.345 MPA) must be reduced to 50 PSI (0.345
MPA).
•
Use a filter in the water line to avoid equipment
damage and beverage off-taste. Check the water filter
periodically, as required by local conditions.
• CAUTION:
The water supply must be protected by
means of an air gap, a backflow prevention device
(located upstream of the CO
2
injection system)
or another approved method to comply with NSF
standards.
A leaking inlet water check valve will
allow carbonated water to flow back through the pump
when it is shut off and contaminate the water supply.
• CAUTION:
Ensure the backflow prevention device
complies with ASSE and local standards. It is the
responsibility of the installer to ensure compliance.
!
Water Notice