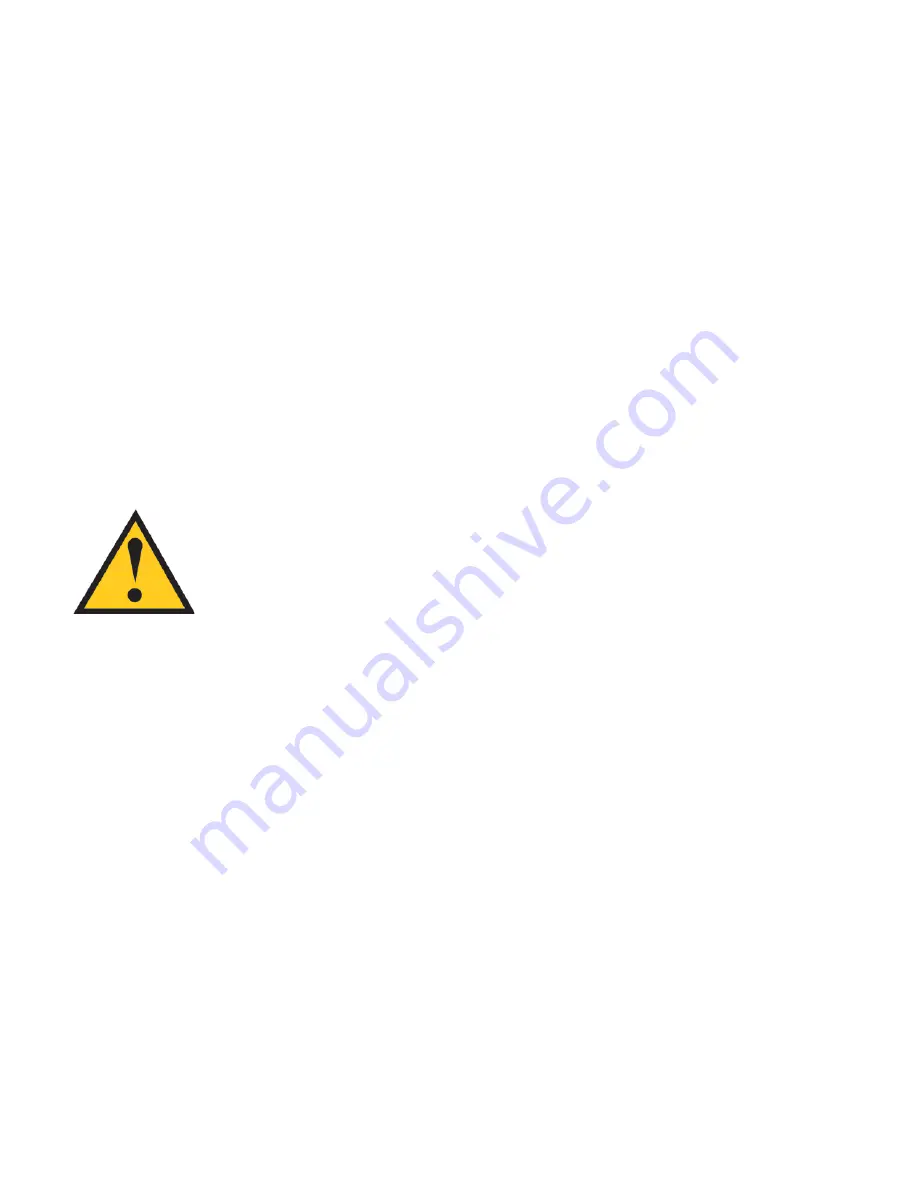
3.
RECOMMENDED SERVICE AND MAINTENANCE
3.1
SCHEDULED
A. Daily – See Section 3.4 for daily cleaning.
B
Monthly – See Section 3.5 for monthly cleaning.
C. Periodic Sanitizing - See sections 3.2 and 3.3 for sanitizing requirements.
D. As needed - Keep exterior surfaces of dispenser (including drip tray and cup rest) clean with a
damp, clean cloth.
3.2
CLEANING AND SANITIZING SYSTEMS
A. General Information
(1) Lancer equipment (new or reconditioned) is shipped from the factory cleaned and sanitized
according to NSF guidelines. The operator of the equipment must provide
continuous maintenance as required by this manual and state and local health
department guidelines to maintain proper operation and sanitization.
NOTE:
The cleaning and sanitizing procedures below pertain to the Lancer equipment identified
by this manual. If other equipment is being cleaned, follow the guidelines established for that
equipment.
(2) Cleaning and sanitizing should be accomplished only by trained personnel. Use sanitary
gloves during cleaning and sanitizing operations. Observe all safety precautions. Follow
instruction warnings on the cleaning product.
(3) Recommended Preparation of Cleaning Solutions.
(a) Cleaning solutions (for example, Ivory Liquid, Calgon, etc.) mixed with clean, potable
water at a temperature of 90 to 110 degrees Fahrenheit should be used to clean
equipment. The mixture ratio, using Ivory Liquid, is one ounce of cleanser to two gallons
of water. A minimum of four gallons of cleaning mixture should be prepared.
NOTE:
Extended lengths of product lines may require that an additional volume of solution be
prepared.
(b) Any equivalent cleanser may be used as long as it provides a caustic-based,
non-perfumed, easily-rinsed mixture containing at least two percent sodium
hydroxide (NaOH).
(4) Recommended Preparation of Sanitizing Solutions.
(a) Sanitizing solutions should be prepared according to the manufacturer’s written
recommendations and safety guidelines. Follow manufacturer’s requirements so that
the solution provides 200 parts per million (PPM) chlorine at a temperature of 90
o
F to
120
o
F. Prepare a minimum of four gallons of sanitizing solution.
NOTE:
Extended lengths of product lines may require that an additional volume of solution be
prepared.
(b) Any sanitizing solution may be used as long as it is prepared according to the
manufacturer’s written recommendations and safety guidelines, and provides 200 parts
per million (PPM) chlorine.
WARNING!
To avoid contamination, do not disconnect water lines when cleaning and
sanitizing syrup lines.
20
P.N. 28-0720/05