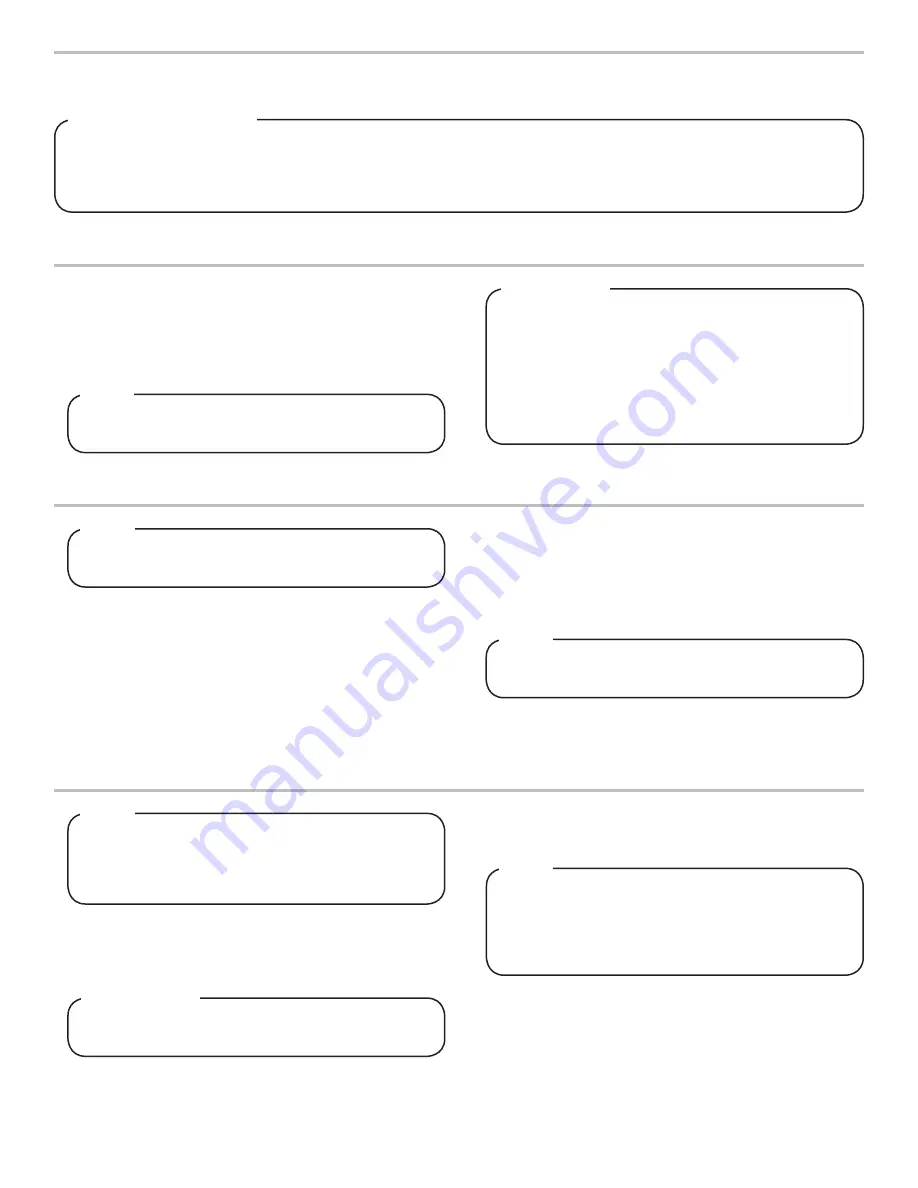
9
INSTALLATION
Unpacking the Dispenser
1. Set shipping carton upright on the floor then cut package
banding straps and remove.
2. Open top of carton and remove interior packaging.
3. Lift carton up and off of the unit.
4. Remove accessory kit and loose parts from ice compartment.
If unit is to be transported, it is advisable to leave the
unit secured to the plywood shipping base.
NOTE
Selecting/Preparing a Counter Location
The dispenser should only be installed in a location
where it can be overseen by trained personnel
NOTE
This manual was developed by Lancer Corporation as a reference guide for the owner/operator and installer of this dispenser.
Please read this manual before installation and operation of this dispenser. See pages 20 - 23 for troubleshooting or service
assistance. If the service cannot be corrected please call your Service Agent or Lancer Customer Service. Always have your
model and serial number available when you call.
Read This Manual
To avoid personal injury or damage, do not attempt to
lift a unit without help. For heavier units, use of a
mechanical lift may be appropriate. Units are equipped
with automatic agitation. The unit may activate
unexpectedly. Do not place hands, or foreign objects
into the ice storage compartment. Unplug dispenser
from the power source, when unit is being serviced,
cleaned, or sanitized.
!
WARNING
1. Select a level, well ventilated location that is in close
proximity to a properly grounded electrical outlet, within
five (5) feet (1.5 m) of a drain, a water supply that meets
the requirements shown in the Specifications section found
on pages 2-3, and away from direct sunlight or overhead
lighting
4. Select a location for the remote carbonator, syrup pumps,
CO
2
tank, syrup containers, and water filter (recommended).
NSF listed units must be sealed to the counter or have
four (4) inch legs installed.
NOTE
2. The selected location should be able to support the weight
of the dispenser and ice after the counter cut out is made.
Total weight (with ice) for this unit could exceed 400 pounds
(181.4 kg).
3. If installed directly on the counter, unit must be sealed to the
counter-top with an FDA approved sealant.
The installation, and relocation if necessary, must
be carried out by qualified personnel with up-to-date
knowledge and practical experience, in accordance with
current regulations.
NOTE
1. Inspect the counter location where the unit is to be installed
then make counter cut-out, (See
Specifications
section on
page 2 or Cut-out Diagrams on page 41 for counter cut-out
dimensions).
Counter cut-out must be accurate, according to unit
specifications.
!
ATTENTION
Dispenser Installation
2. Once the counter cut-out is made, lower the unit into the
counter and seal rim to the counter using an approved
silicone sealant.
The unit can extend up to 23 inches (58.42 cm) below
the counter, including the shipping risers, which
Lancer recommends be left attached to the unit. Should
the dispenser ever require removal, the shipping risers
will protect the inlet tubes from being damaged.
NOTE