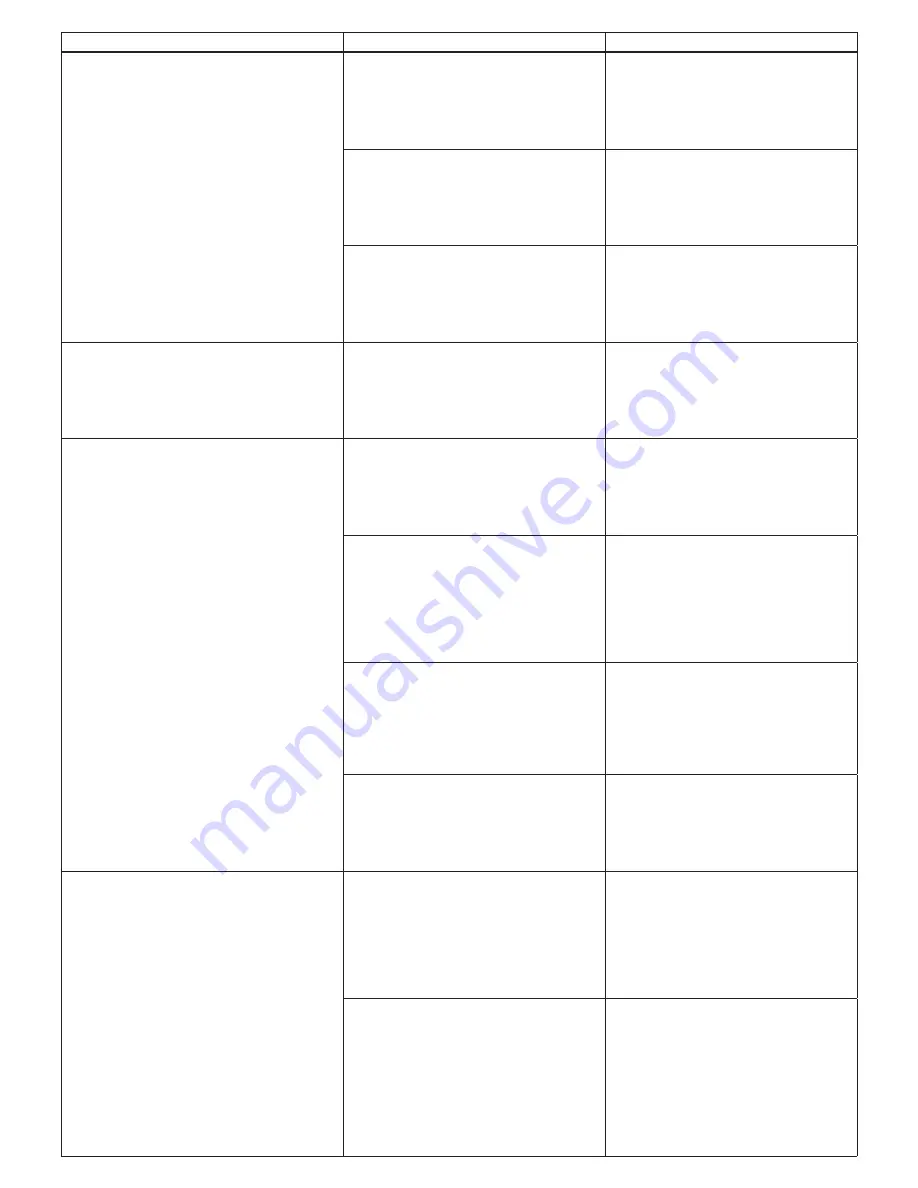
PAGE 23
Problem
Possible Cause
Solution
12. Error – 103 = Control valve motor ran too
long and was unable to find the next cycle
position
a. Motor failure during a backwash
a. Check motor connections then Press
NEXT
and
REGEN
buttons for 3
seconds to resynchronize software
with piston position or disconnect
power supply from PC Board for 5
seconds and then reconnect.
b. Foreign matter built up on piston and
stack assemblies creating friction and
drag enough to time out motor
b. Replace piston and stack assemblies.
Press
NEXT
and
REGEN
buttons for
3 seconds to resynchronize software
with piston position or disconnect
power supply from PC Board for 5
seconds and then reconnect.
c. Drive bracket not snapped in properly
and out enough that reduction gears and
drive gear do not interface
c. Snap drive bracket in properly then
Press
NEXT
and
REGEN
buttons for
3 seconds to resynchronize software
with piston position or disconnect
power supply from PC Board for 5
seconds and then reconnect.
13. Error – 104 = Control valve motor ran
too long and timed out trying to reach home
position
a. Drive bracket not snapped in properly
and out enough that reduction gears and
drive gear do not interface
a. Snap drive bracket in properly then
Press
NEXT
and
REGEN
buttons for
3 seconds to resynchronize software
with piston position or disconnect
power supply from PC Board for 5
seconds and then reconnect.
14. Error -106 = MAV/ SEPS/ NHBP/ AUX MAV
valve motor ran too long and unable to find the
proper park position
Motorized Alternating Valve = MAV
Separate Source = SEPS
No Hard Water Bypass = NHBP
Auxiliary MAV = AUX MAV
a. Control valve programmed for ALT A or
B, nHbP, SEPS, or AUX MAV with out
having a MAV or NHBP valve attached to
operate that function
a. Press
NEXT
and
REGEN
buttons for
3 seconds to resynchronize software
with piston position or disconnect
power supply from PC Board for 5
seconds and then reconnect. Then re-
program valve to proper setting
b. MAV/ NHBP motor wire not connected to
PC Board
b. Connect MAV/ NHBP motor to PC
Board two pin connection labeled
MAV MTR. Press
NEXT
and
REGEN
buttons for 3 seconds to
resynchronize software with piston
position or disconnect power supply
from PC Board for 5 seconds and then
reconnect.
c. MAV/ NHBP motor not fully engaged with
reduction gears
c. Properly insert motor into casing, do
not force into casing. Press
NEXT
and
REGEN
buttons for 3 seconds
to resynchronize software with piston
position or disconnect power supply
from PC Board for 5 seconds and then
reconnect
d. Foreign matter built up on piston and
stack assemblies creating friction and
drag enough to time out motor
d. Replace piston and stack assemblies.
Press
NEXT
and
REGEN
buttons for
3 seconds to resynchronize software
with piston position or disconnect
power supply from PC Board for 5
seconds and then reconnect.
15. Error – 107 = MAV/ SEPS/ NHBP/ AUX
MAV valve motor ran too short (stalled) while
looking for proper park position
Motorized Alternating Valve = MAV
Separate Source = SEPS
No Hard Water Bypass = NHBP
Auxiliary MAV = AUX MAV
a. Foreign material is lodged in MAV/ NHBP
valve
a. Open up MAV/ NHBP valve and check
piston and seal/ stack assembly for
foreign material. Press
NEXT
and
REGEN
buttons for 3 seconds to
resynchronize software with piston
position or disconnect power supply
from PC Board for 5 seconds and then
reconnect.
b. Mechanical binding
b. Check piston and seal/ stack assembly,
check reduction gears, drive gear
interface, and check MAV/ NHBP
black drive pinion on motor for being
jammed into motor body. Press
NEXT
and
REGEN
buttons for 3 seconds
to resynchronize software with piston
position or disconnect power supply
from PC Board for 5 seconds and then
reconnect.